On the surface everything seems fine, but are people following the rules because they’re told to, or because they really want to? Is safety behavior so deeply embedded in the organization that it has moved from a reactive culture to a proactive one?
The pandemic of the past few years has meant that safety behaviors have lost traction in many companies. Older operators have left, and their replacements aren’t always so familiar with best practice. There’s also big pressure to deliver on targets, so the appeal of cutting corners to get the job done quickly is always there – and can even be rewarded. Gradually it becomes acceptable to work in a certain way and nobody corrects these bad habits.
A Shared Responsibility. A Shared Focus
The way forward is to build your safety culture from the shop floor up. It must be clear exactly what role leadership will play and what operators should and shouldn’t do. Only when leadership creates the right focus and support, and only when operators feel that safety is a vital part of their responsibility, will everyone believe that they’re moving forward together.
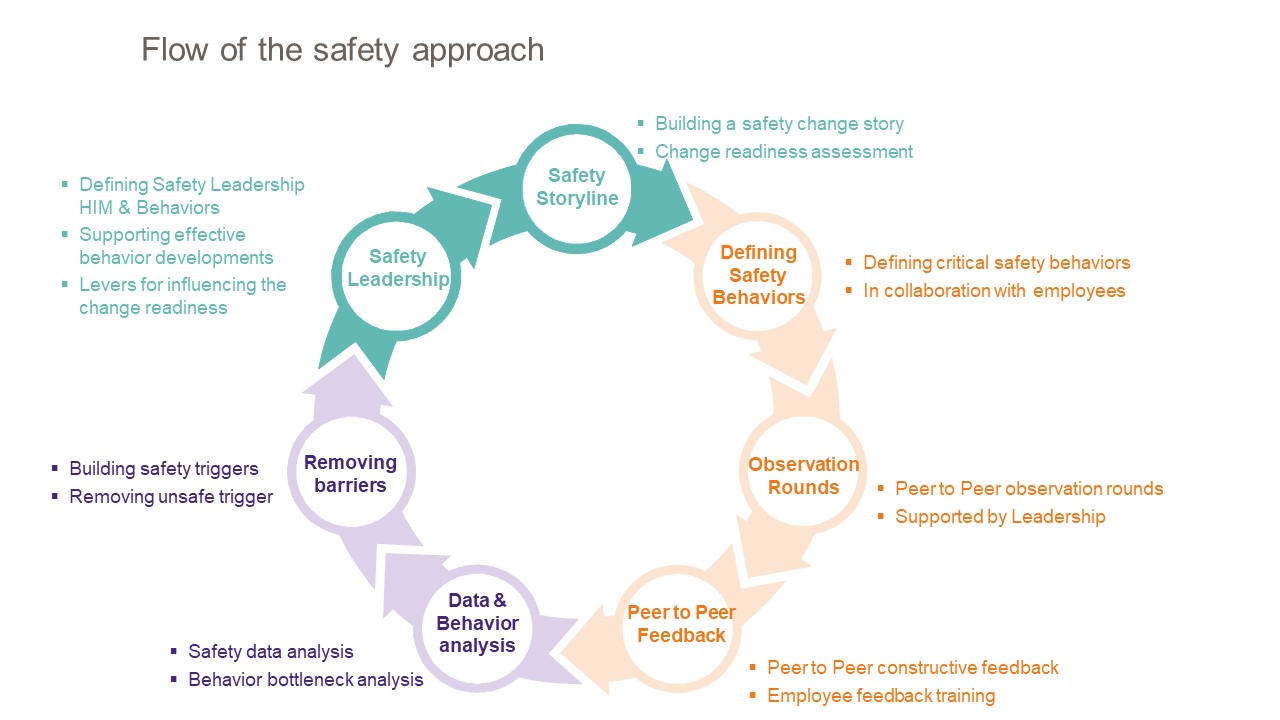
That’s why it’s crucial that operators help define the desired safety behaviors. They must take the lead in the observational safety rounds, give peer to peer feedback and ensure that everyone is doing what they’re supposed to be doing. This is the essence of shared responsibility.
Create a New Momentum
You have to start with a clear, expectation driven program from the bottom up that will create concrete, observable, standardized ways of working. Leaders must set expectations and have everyone contribute to them. The people on the shop floor must do regular activities that provoke observation and action. They must also create the right interactions between the front line leaders and the operating teams. Observations and deviations should be fed back into the normal operational reviews in their daily meetings to create valuable data that enables everyone to see how well things are developing. These new safety behaviors must become second nature. That way the threshold for safety behavior excellence becomes easier and easier to achieve because it’s now a daily fact of life. It energizes everyone, enabling them to not only observe the behavior of colleagues, but also to be much more aware of their own behavior.
Develop “I Want to” Safety Behaviors with the Operators
The way you develop and implement your safety behavior program is crucial. It can be tricky to build something from the bottom up, because as well as being involved in the new safety program people obviously have to complete their own work. So, you have to give them the right tools and support so that they willingly adopt this new approach.
Let’s be honest, there are a lot of gray areas for safety on any site and not everything can be 100% defined within a safety program. So, the first thing to do is to examine these grey areas, do a thorough safety analysis and make a safety risk map to identify where most unsafe behaviors are occurring. Once these have been identified, discuss everything with the operators and jointly define the ideal behaviors, so that what they have to focus on amongst themselves has already been defined by them.
Then when they do the observation rounds, they must really focus on these gray areas and if they see that the defined safety areas are not being followed, they need to have a conversation amongst themselves. First, they need to agree what has been observed, then the observer operator needs to ask the other operators why they behaved in that way? You need to know why someone shows a certain kind of behavior before you can jointly agree the steps to correct it. The data from these conversations should be collected anonymously so that operators are not judging each other but working together to improve safety behavior. Once the data has been collected leaders should openly and honestly analyze it with the operations team and really dive into the reasons why someone behaves in a certain way. Everyone needs to understand exactly what is going on because “I have to” and “I want to” are about the intrinsic motivation of human beings. Behavior is never a coincidence and if you don’t understand why people behave a certain way, you can’t change their behavior.
Remember, it takes time to develop “I want to” safety behaviors. If you want them to become habits, people need to own them and perform them over a period of time. Integrating really effective safety behavioral change has been difficult for many companies. Now it’s time for a new approach that will deliver a big impact.
Authors: Lucas van Engelen, International Expert Human Dynamics, and Michiel Van Den Boomen, Vice President, EFESO Consulting