Carbon Footprinting as a Competitive Advantage
Chemical industry's pivotal role in sustainability; Carbon accounting as a game-changer for competitiveness
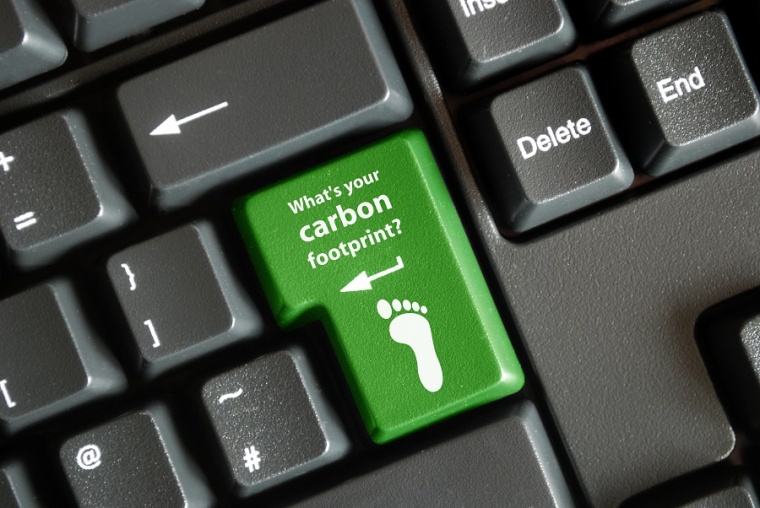
If you ever wondered why the chemical industry is often referred to as a hidden champion in the global effort to transform to a sustainable economy, simply ask yourself: What do industry sectors like discrete manufacturing, life sciences, construction, or consumer products have in common? They are all dependant on the chemicals industry, to produce their products. The impact of this is immense, with some reports estimating that over 95% of all manufactured goods rely on some form of industrial chemical products.
Now combine this initial situation with the rise of legislation on carbon emissions worldwide, like the European Commission’s European Climate Law that sets a legally binding target of net zero greenhouse gas emissions by 2050. Moreover, the EU Corporate Sustainability Reporting Directive (CSRD) will require companies with over 250 employees to report GHG emissions including value chain emissions (Scope 3). This increase in regulations will go hand in hand with increased audit and assurance requirements that typically do not lend themselves well to homegrown tools or simplified calculators. Having this in mind, it is critical that chemical companies are not only able to measure and improve the carbon footprints of their products, but also to report and share them along the downstream value chain.
Current Challenges of Carbon Accounting
To reach this target state, two prerequisites need to be fulfilled: data quality and data access. Regarding quality data, companies currently largely rely on averages and secondary data instead of using primary data from their operations and suppliers when assessing carbon footprints. This hinders them to truly understand where their own emission hotspots are and how they can improve them. There is also a challenge referring to how the data itself is being accounted. Currently, there are standards and protocols (with GHG Protocol Corporate Accounting and Reporting Standard most widely used) as well as sector guidelines (e.g., the various Environmental Product Declaration) that companies can voluntarily adopt. Initiatives like the Partnership for Carbon Transparency (PACT) at World Business Council for Sustainable Development (WBCSD) criticize that the inconsistent use of such methodologies results in insufficient accounting, reporting and exchange of emissions data. SAP joined WBCSD in 2021 as an innovation partner for PACT to join forces in defining a uniform standard that can be used regardless of industry.
When it comes to data access, it is important to stress that this does not only refer to having access to a companies’ own operations data (Scope 1 and 2 emissions). More and more companies are extending the scope of their climate commitments to their value chains (Scope 3). For most, this is where 80% or more of emissions can be found. For chemical companies — that are at the start of the value chain — this means they also need to focus on being able to share their carbon data with their downstream ecosystem. In order to calculate their product footprint, they also need reliable data from their suppliers. This is where the complexity lies. Many suppliers are not sophisticated enough and there is a lot of manual work involved. Data needs to not only be reliable but also comparable to other suppliers as well as auditable.
Industry networks like the Catena-X Automotive Network are already early indicators of what the future holds in terms of both data quality and data sharing along the value chain. Catena X started with the goal to provide an open and collaborative data ecosystem along the entire automotive value chain, one of its use cases is dedicated to the standardised measurement of real carbon data that can be shared with all network participants. With the automotive industry being an important customer, it is no wonder to see global players like BASF and Henkel on the list of members.
But chemical customers are not only participating in the networks of other industries — they are also working on creating their own methodologies and carbon data networks through industry consortia like Together for Sustainability (TfS). The TfS calculation guideline, published in September 2022, is being considered by many chemical customers as a way to calculate and compare Scope 3 data from suppliers.
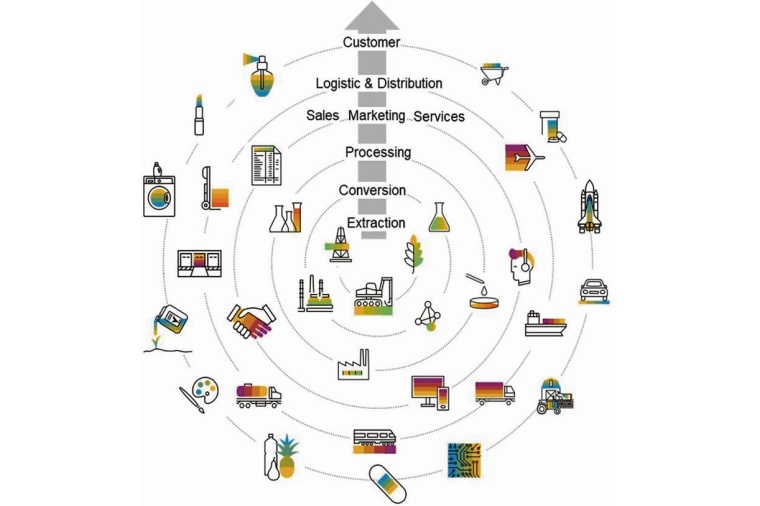
It Takes a Holistic and Integrated Approach
SAP developed a platform application that enables organizations to share product carbon information with their customers and vendors, empowering them to measure and reduce their carbon footprint while promoting transparency throughout the supply chain. This is all done while keeping in mind that suppliers need a very low barrier of entry to participate as well as a platform that is able to scale across one or more industries. Being involved in networks like Catena-X from the start gives SAP a deep expertise in carbon data exchange.
The product footprint data can either be calculated in SAP Sustainability Footprint Management or from another calculation tool. This data can then flow through to customers downstream using technology such as SAP’s newly launched Sustainability Data Exchange (SDX). With SDX companies can exchange product carbon footprint (PCF) data while also complying with global standards. Having a standardized format to record and share data helps companies move from estimated sustainability values to actual and accurate product-level data. Hereby accelerating their journey toward net zero by providing them standardized audit-ready sustainable values.
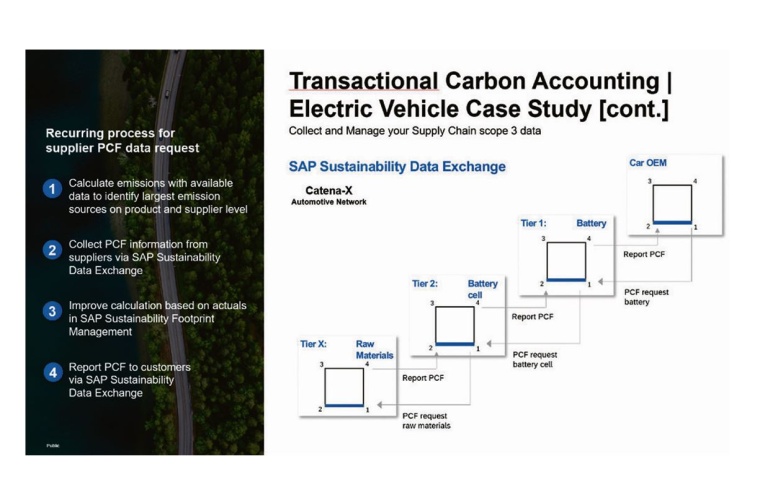
Reinventing the “R” in ERP
The current situation, where carbon accounting is often done using spreadsheets and global averages instead of actuals for carbon footprints, needs to evolve towards precise and holistic transactional accounting. WBCSD and SAP have joined forces calling for a transformation of the carbon accounting system. A green ledger as part of a company’s ERP will allow customers to account emissions in the same fashion as financials and goods movements. The information provided by a green ledger will enable deep insights and effective decision-making. This approach is complemented through integrations with SAP solutions which calculate footprints. Hereby embedding footprint into backend business processes as well as business steering while managing carbon flows management and exchanges along the value chain. Standardized data formats including common data semantics facilitate the implementation and grant for scalable adoption. Emissions on both corporate and product level are consistently managed alongside financial data to achieve profitable trade-offs between cost efficiency and resource use.
The Sustainable Business Imperative
To be future-proof, chemical companies will need to continue to transform their business with sustainability at the core of their strategy. With both regulators and customers increasingly expecting them to be able to measure and report their carbon footprints, operating sustainably will be one of the decisive competitive advantages going forward.
Monica Gassmann, Global Head of Sustainability in Industries,
and Michael Sambeth, Enterprise Architect for Process Industries, SAP, Walldorf, Germany
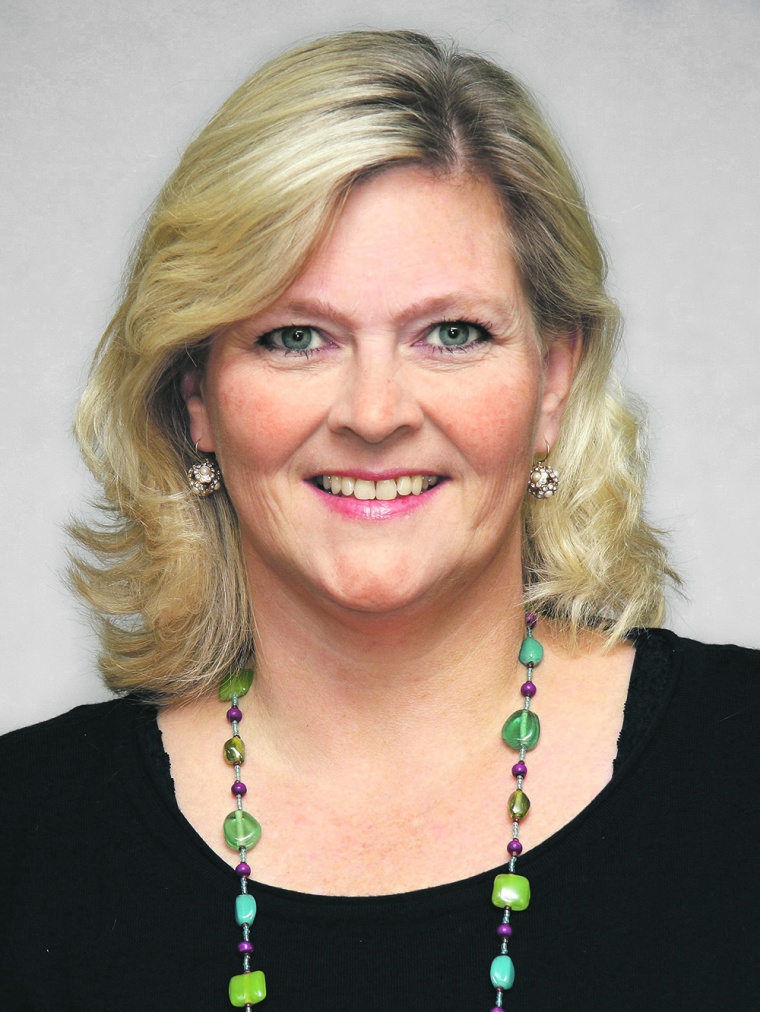
Monica Gassmann is Global Head of Sustainability in Industries at SAP and has spent her whole career in and around the chemical industry before becoming responsible for all 25 industries at SAP. She joined SAP in 2000 and has a background in International Business and Production and Inventory Management
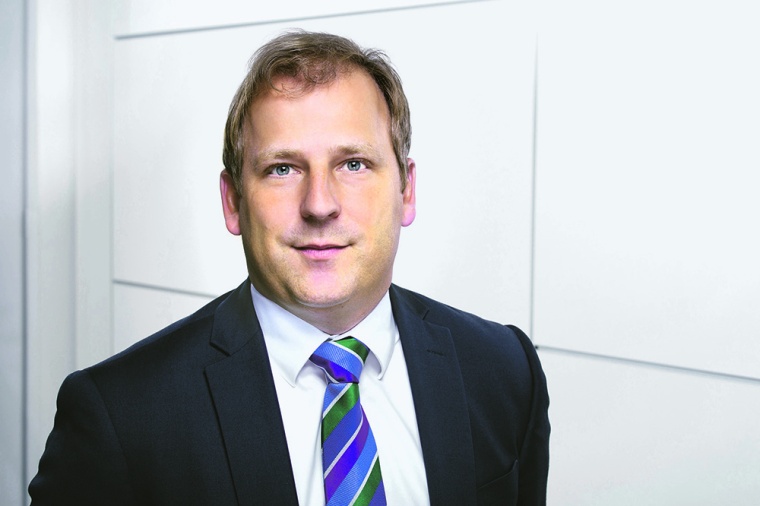
Michael Sambeth joined SAP in 2002. His current position is Enterprise Architect in the SAP industries organization for Process Industries. With his work he focuses on Sustainability Management helping chemical and pharma companies evolving their IT and data landscape towards efficient ESG management. Michael has a background in business administration, computer science and social sciences based on a diploma from Mannheim University and an MBA from Quadriga University Berlin.