Curiosity, Disillusionment, Persistence, Success
Given the challenges the pharmaceutical industry is facing – secure material supply, reduce operation cost and increase flexibility, enhance sustainability and safety, innovate and reduce time-to-market – the sector is poised for a breakthrough of flow chemistry.
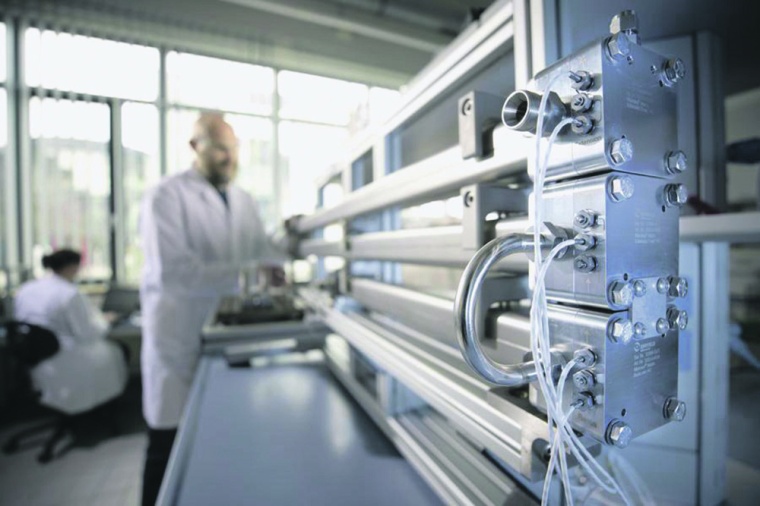
Around 1995, the path of the microreaction technology platform began when Wolfgang Ehrfeld, then professor and head of the Institute of Microtechnology in Mainz, Germany, was driven by the question: If the topic of „micro“ has led to enormous performance increases and innovations in electronics, why should this not be possible in the field of process technologies?
Microreaction technology means channel dimensions in the micro and millimeter range with significantly improved surface-to-volume ratios compared to established process technologies and shorter mixing times. For fast, highly exothermic reactions, there is considerable potential for improving product quality, product yield, raw material and energy requirements, process safety and manufacturing costs and EBIT, with attractive capital payback times.
Advantages of microreaction technology are fast and good mixing and excellent heat transfer performances, enabling higher selectivities and yields while lowering raw material requirements. Besides, the number of by-products and the energy demand for their separation (downstream processing) is reduced. About 70% of energy costs correspond to the separation of by-products. In terms of safety, fast, explosive, and highly exothermic reactions involving toxic substances can be run in much smaller reactor volumes compared to batch reactors.
Developing New Synthesis Pathways
However, micrometer-scale channel dimensions are not suitable for use in production because they are too prone to clogging, do not meet the robustness requirements of a production operation and allow only relatively small throughputs. For production, therefore, a scale-up to the millimeter scale is necessary, which retains the advantages of microtechnology in terms of heat transfer performance and mixing speed. In the scale-up process, the transition of channel geometries from the micrometer to the millimeter scale already takes place in the laboratory. Conversions, yields, process parameters and product qualities determined in this way in laboratory can be transferred directly to conditions in production reactors with same channel geometries. A scale-up step on a pilot scale is no longer necessary, although of course pilot tests with real raw material qualities from production to investigate fouling, cleaning procedures and longtime stability of the process cannot be dispensed with. The integrated scale-up concept leads to a quick scale-up to production.
From our point of view, a few segments have emerged as particularly attractive for the application of microreaction technology: pharmaceuticals, fine and specialty chemicals, agrochemicals, and chemical ingredients for consumer care products and food and beverages.
“Continuous approaches can contribute
to developing new optimized
synthesis pathways.”
In many industries in Europe and the US, postponing of innovation is quite common, the pharmaceutical and fine chemicals industries included. However, continuous optimization is and will remain an increasingly important issue for companies in order to keep up with the current pace of technological evolution and to be innovative. Redesign of a chemical process is mandatory for a transfer from a batch to a continuous process. It is probably due to this time effort that people fall back on the original manufacturing method instead of running processes continuously and thus more efficiently, sustainably and safely. Continuous approaches can contribute to developing new optimized synthesis pathways. However, the priority of the pharmaceutical industry is the on-time delivery of life-saving drugs.
Increasing Flexibility and Sustainability
Active pharmaceutical ingredients (APIs) are usually produced in multi-step synthesis processes due to the very often complex structure of the molecules. Take lithiation as a simple two-step example: In a batch process, the addition reaction step proceeds very slowly because the unstable and highly reactive intermediates decompose rapidly. The reaction must be run at extremely low temperatures (-48°C) while the continuous process can be run at room temperature because of the excellent heat exchange, effective mixing and precise control of process. This results in less by-product formation and therefore higher yields, making the process safer and „greener“. Besides, energy savings due to avoiding cryogenic conditions make the continuous process highly cost effective.
Additionally, manufacturers are dependent on effective supply chain processes. This has become much more apparent after the outbreak of the Covid pandemic. Critical delays in the supply of raw materials can have a significant impact on projects. Pandemic-related disruptions of transportation links have been a major challenge for many chemical companies. Producing key raw materials instead of sourcing them is becoming more essential for companies and definitely more profitable under companies’ perspectives. Microreaction technology can be the key to success right here, as required quantities can be produced selectively and sustainably in a short time with low hold-up and space requirements.
Sustainability can be viewed from two sides here, from an environmental perspective and from an economic perspective. The environmental aspect of flow chemistry/microreaction technology combines two factors: the lower formation of by-products — which leads to higher yields and smaller amounts of raw materials — and the abdication of additional solvents — which do not have to be separated later in cost-intensive steps. Process reliability also plays a major role. The much smaller internal volumes of the micro and millireactors, do not have to be filled or emptied like batch reactors, what prevents the risk of explosions and fires. From an economic point of view, cost savings can be established through improved product quality, raw material savings, reduced space requirements, sustainable plant safety, lower energy consumption, and, in consequence, more favorable CO2 balances
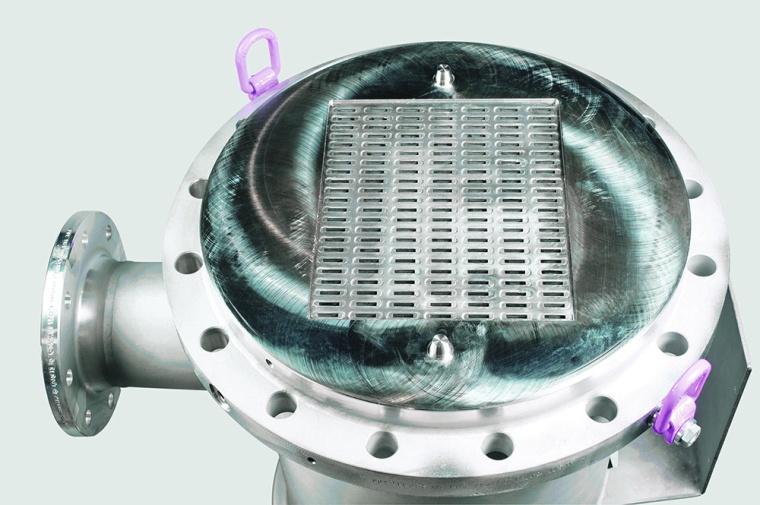
Making the Transition
Thus, the principles of Green Chemistry can be perfectly met by the application of flow chemistry/microreaction technology. Flow chemistry applications are inherently safer because they require comparably smaller reaction volumes and lower amounts of solvents and chemical substances. The risk of environmental exposure from chemical substances is almost non-existent, and processes can be scaled up easily and quickly without the need for the optimization of reaction conditions.
Considering these advantages suggests the question: why is flow chemistry, and in particular microreaction technology, not already established process technology? The answer is multilayered.
“The principles of Green Chemistry
can be perfectly met by the application
of flow chemistry / microreaction technology.”
Developing continuous processes requires significant financial investment for most companies. Therefore, direct evidence of the return on investment (ROI) is critical for a company to make the transition. Drivers for moving from batch to flow processes include reducing capital expenditures (CAPEX) and operating expenses (OPEX), as well as significantly increasing process safety and product quality.
Any development cycle consists of the following phases: curiosity, disillusionment, persistence and success. At the very beginning, microreaction technology was known as a „panacea“ for all process engineering problems, whereupon curiosity led to the integration of the technology, which quickly turned into the disillusionment phase. At that time, the technology was still far from being ready to survive, especially in production. New developments take an average of about 30 years to be established in the market. Now, we are in the persistence phase, whereby transition to the success phase has already started in some cases. Given the challenges the pharmaceutical industry is facing — secure material supply, reduce operation cost and increase flexibility, enhance sustainability and safety, innovate and reduce time-to-market — the question regarding the breakthrough of flow chemistry is: if not now, when?
Authors:
Joachim Heck, CEO,
and Anne Kaaden, Head of Marketing, Ehrfeld Mikrotechnik, Wendelsheim, Germany
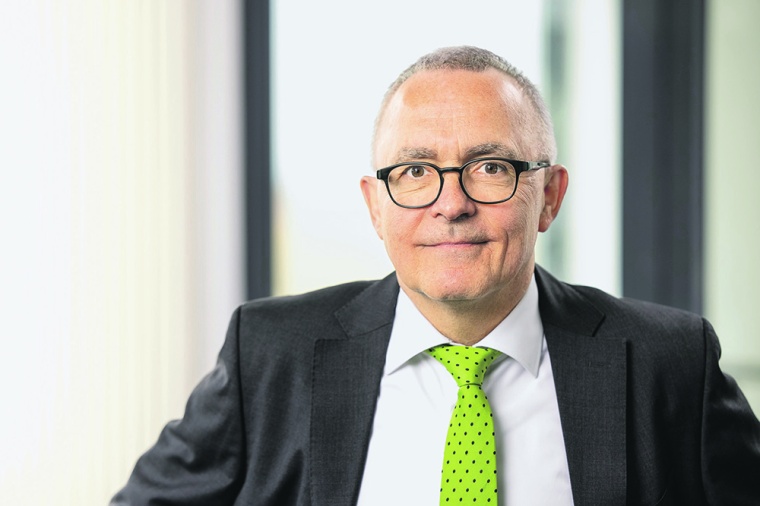
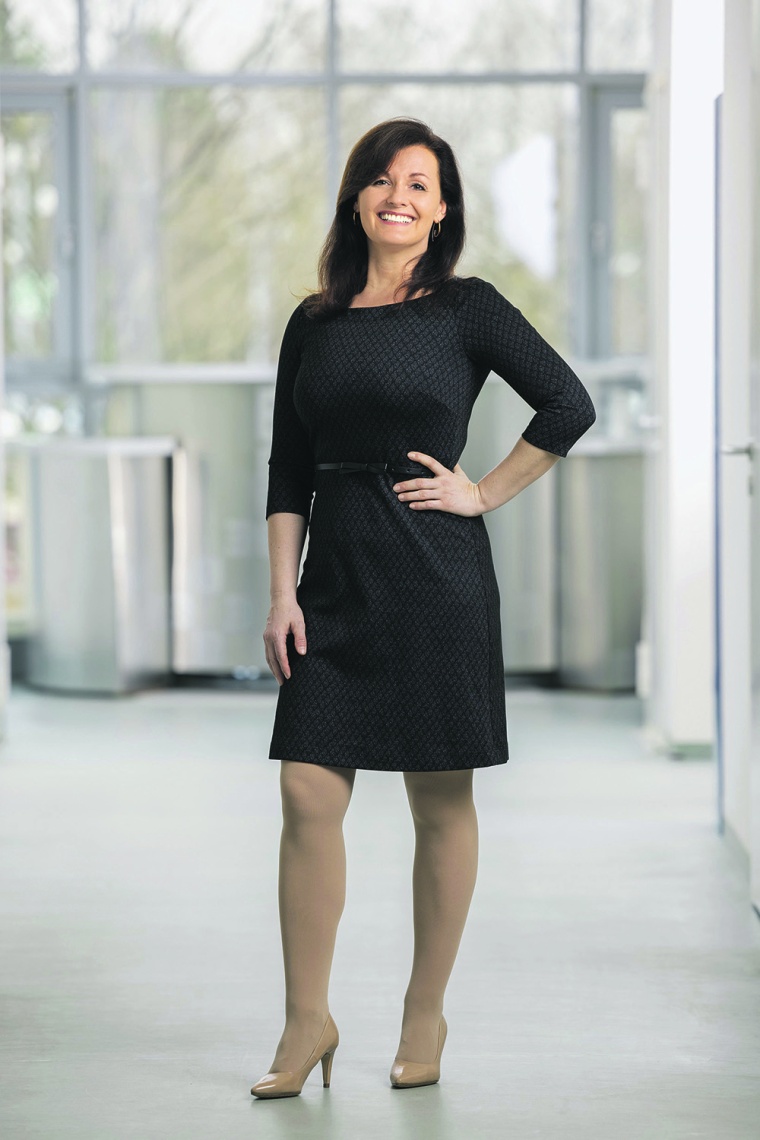
_______________
Experts in Flow Chemistry
Ehrfeld is the pioneer in implementing the technology platform of micro and millireactors as process technology. Offering a complete product portfolio of pharma-compliant metallic equipment from laboratory to production scale the company is able to guide customers in implementing the technology platform and run through the experience curve as quickly as possible. The modular microreaction system (MMRS) enables easy start-up on a laboratory scale, similar to a Lego building block system. The design of the production equipment is based on established equipment concepts, including the Miprowa tube-bundle reactors, whose tubes are replaced by rectangular channels, and which are used especially in applications in specialty chemical industries, and the plate heat exchangers with the FlowPlate and ART reactors, which are particularly suitable for fine chemical and pharmaceutical industries.
Further reading: CHEManager asked executives and industry experts to share their views on drivers as well as barriers for the use of flow chemistry and the prospect for this technology in the pharmaceutical sector.