A Digital Twin for the Cold Chain
The virtual cold chain is a modern software approach to save time and minimize for the shipment of temperature-sensitive goods by determining the lane-specific optimum level of thermal protection.
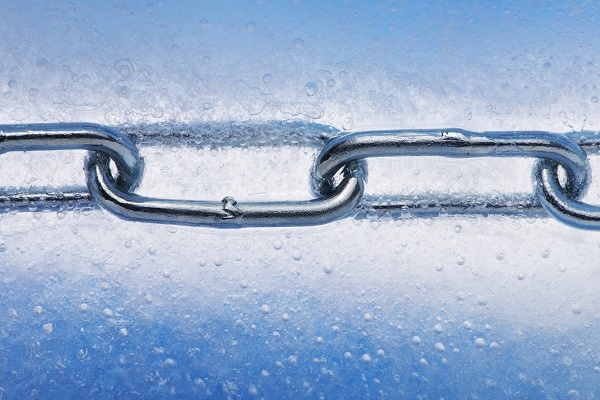
The virtual cold chain is a modern software approach to save time and minimize costs in the cold chain. Pharma companies use it to simulate the shipment of temperature-sensitive goods and determine the lane-specific optimum level of thermal protection, to only invest in what is necessary. This computer-based approach is faster, cheaper, and more reliable than classical physical testing, because it requires no physical shipments and can be used to test thousands of potential scenarios.
The global distribution of temperature-sensitive ingredients and products is a central challenge in modern supply chains. Lately, the criticality became particularly apparent during the distribution of Covid-19 vaccines. The pharmaceutical products had to be kept between 2 °C and 8 °C, below -20 °C, or even as low as -70 °C, during delivery across a multitude of origins and destinations.
One core task for a reliable and efficient cold chain is to determine the optimum combination of packaging and logistics service: too little thermal protection leads to unacceptable temperature excursions, compromising the quality of the payload; too much protection results in unnecessarily high costs and carbon emissions. Given the variety of thermal conditions in which goods are shipped, there is no one-fits-all optimum solution; each setup has a specific optimum. Some might require an expensive container and pharma-level logistics, others might work in light protection and general cargo. Often the optimum lies somewhere in the middle, and a decision has to be made to invest in better container insulation, or to book higher logistics service levels with temperature-controlled facilities.
Physical Testing is Limited by Nature
The quest for finding and validating the optimum combination can be attempted by physical testing against expected temperature conditions. This classical strategy is naturally limited, because it provides only a snapshot of the real conditions a shipment will experience: In reality, ambient conditions are different for each month and each departure time, there can be flight delays, re-routings, traffic delays, temperature-controlled storages might not be available. To capture each scenario would require thousand of tests, which is impossible to achieve — unless you are taking the virtual approach.
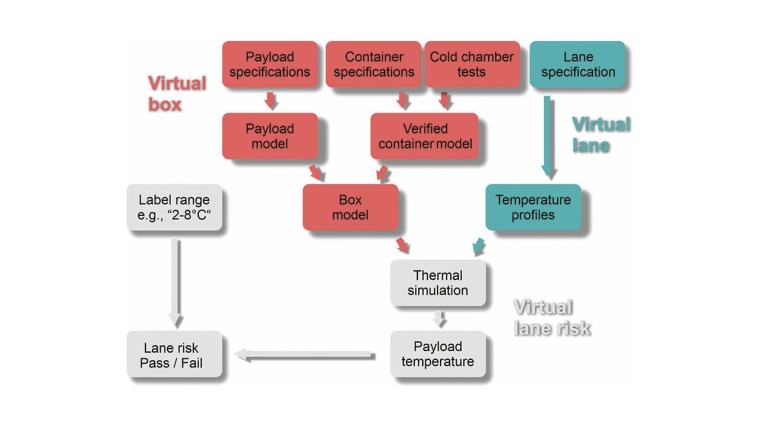
Virtual Lane Risk Assessment
The virtual approach is based on accurate thermodynamic simulation of the distribution process. It takes only a few minutes to simulate a lane of, e.g., 100 h duration. With parallelized simulations, thousands of scenarios can be tested in a matter of hours. In contrast, physical testing cannot be accelerated: it always takes 100 h to physically test a 100-h-lane in a climate chamber or by dummy shipments.
To run a virtual lane risk, a digital twin of the distribution process is established: (a) The container is represented by a virtual box model; its thermophysical parameters are validated to ensure that the model is a suitable representative in any realistic ambient conditions. (b) The lane is virtualized using specifications from the logistics provider and combined with potential risk scenarios. Lane segments in which the container is exposed to ambient conditions are modeled by including historical ambient temperature data from proximate weather stations for the last years. Delays, lane variations, solar irradiation are included as additional scenarios, if relevant. All potential scenarios are evaluated by thermodynamic simulation software, thus generating the equivalent of thousands of historical test shipments.
Total Cost of Ownership
The simulation results show if and under which conditions a temperature excursion is to be expected. To determine the most cost-effective solution, the analyst can combine risk and costs for any container in their supplier’s portfolio and run a total cost of ownership analysis to single out the optimum solution. This approach can be executed for any lane, and all containers on the market: simple passive containers, vacuum-insulated boxes, pallet shippers with phase-change materials, dry ice containers, and reefers.
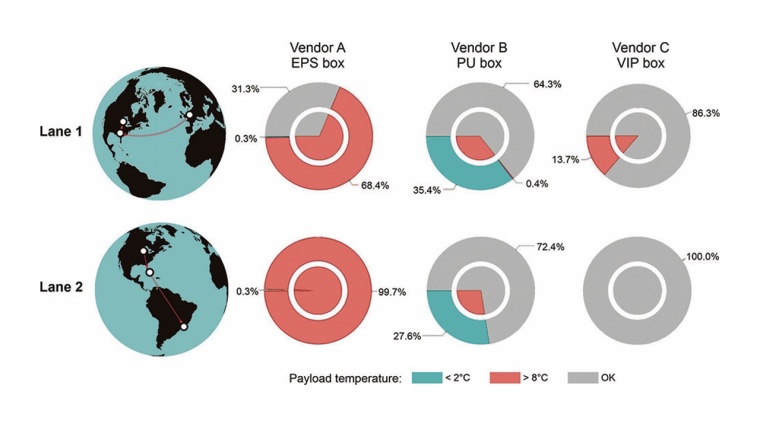
Fast Analysis of Large Data Volumes
A major advantage of this approach is that it is not necessary to collect big data from physical shipments. All data are available before any shipment has been carried out. Statistically, virtual lane risk assessments are even more reliable because thousands of scenarios can be tested, unlike in physical testing. If a thousand of scenarios is not enough, make it a million. Everything is possible. At the end the question is not “Why should I use a virtual approach?”, it is “Why not?”: the virtual cold chain is faster, it can be used before any physical shipments, it is more reliable because it uses more data, it strengthens the scientific foundation of your qualification process to augment your conformity with GDP guidelines, and it is cheaper, because it only involves the costs of the software without any physical shipments or testing.
Authors
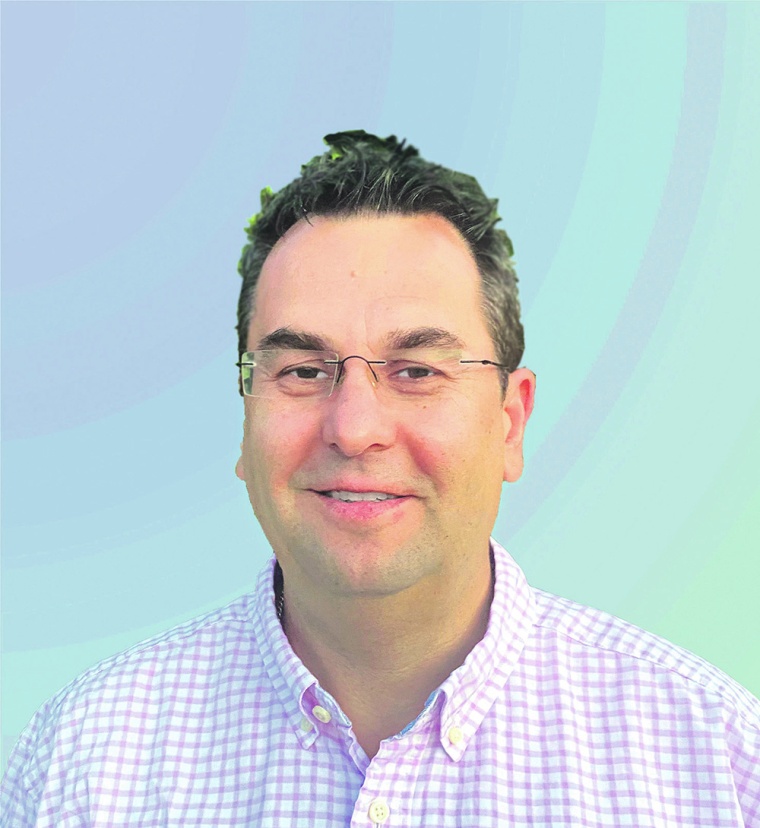
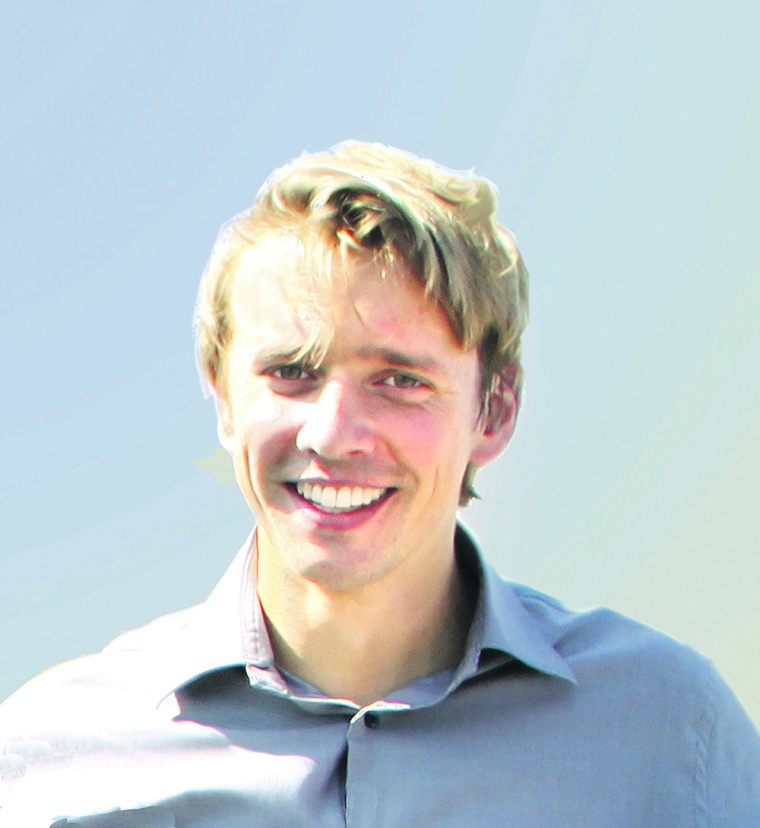