Expert Statement: Rino Woyczyk, Drees & Sommer
ISPE and its members are developing the roadmap to introduce Industry 4.0, also called the Smart Factory, at the pharmaceutical industry as Pharma 4.0 – an operating model that is interconnected, meaning that the digital tools allow for a fully connected network to enable direct communication between all levels in an organization.
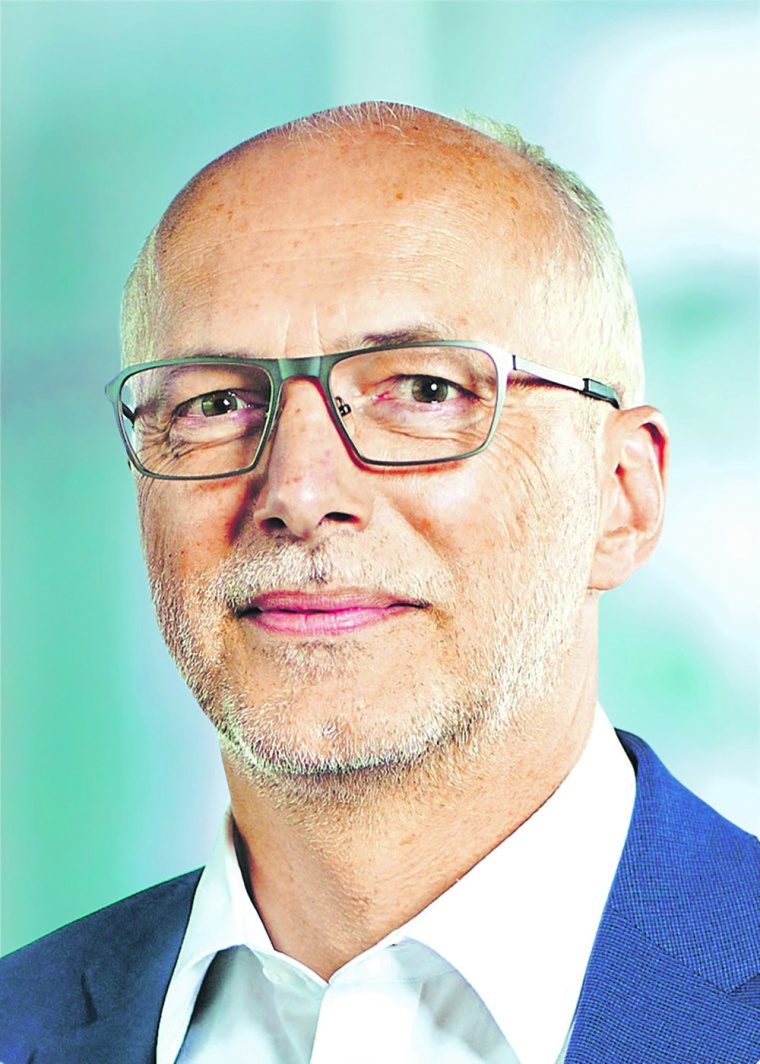
Despite the transformational potential of digitalization, the pharma industry has historically been slower than other sectors in adopting digital tools, such as cloud storage, artificial intelligence (AI), machine learning (ML), blockchain, and remote communication technologies, and in making associated changes in workplace culture and strategic priorities. Now, however, the Covid-19 pandemic may be accelerating the pace of change.
What are the digitalization trends in the industry? What is the business case to develop and implement digital tools and digitalization strategies? And how can organizations introduce and use them?
CHEManager asked executives and industry experts to share their views on digitalization trends in the pharmaceutical industry and challenges on the way to realize the sector’s digital transformation. We proposed to discuss the following aspects:
- What do you think are the key digitalization trends in the pharmaceutical industry?
- What do you consider to be the most important benefits of digitalization in the pharmaceutical industry?
- Is your company involved in systematic, ongoing action to digitalize operations?
- At present, digitalization in the pharmaceutical industry is immature. In your view, what are the biggest obstacles that need to be overcome in the digitalization of the sector?
- How would you rate the digital maturity level of your company?
“Modular digital construction planning
offers maximum user orientation via
defined modules that can be quickly exchanged as needed.”
Rino Woyczyk: For construction projects in the life sciences segment, with its stringent safety, speed and flexibility requirements, two approaches are particularly promising when it comes to digitalization: modular construction and building information modeling (BIM). Linking these two methods forms a powerful digital duo that allows, amongst other things, faster, more reliable and more cost-effective realization of production buildings and labs.
The key to efficient modularization is the digitalization of the design using a BIM model, a process whereby a “digital twin” of the building is created. The building model is consistently modular. Recurring spaces and structures are only modelled once and stored as catalogue models. Examples of such modules are the furnishing modules for user-defined expansions, such as laboratory units, offices and meeting rooms, cloakrooms and kitchens, including their entire development and all of their technical equipment.
Modules from the catalogue are added to the project model according to user preferences. The result is a building design that is developed like a product. The components can be put together according to the customer’s wishes within a coordinated set of rules, and the planning becomes more or less a configuration.
The innovative modular planning approach in combination with a complete digital representation of the building is opening up new dimensions. The buildings of the new pRED research center in Basel, most of which are equipped with laboratories, are set up using this method, and the requirements are very high, due to the necessary laboratory installations and especially the demand for flexibility in the buildings.
Modular digital construction planning offers maximum user orientation via defined modules that can be quickly exchanged as needed. It allows for the quick conversion of labs instead of new construction or renovation. Even in highly customized architecture, the digital duo leads to economical construction and operation and reduces the planning effort as possible errors are already identifiable in the “digital twin”. Thus, it enables a proverbial “quantum leap” towards enormously transformable buildings, perfectly tailored to a particular use and produced to the highest quality standards.