Expert Statement: Shawn Walker, Veranova
Executives and industry experts share their views on drivers as well as barriers for the use of flow chemistry in pharmaceutical manufacturing and the prospect for this technology in their industry sector.
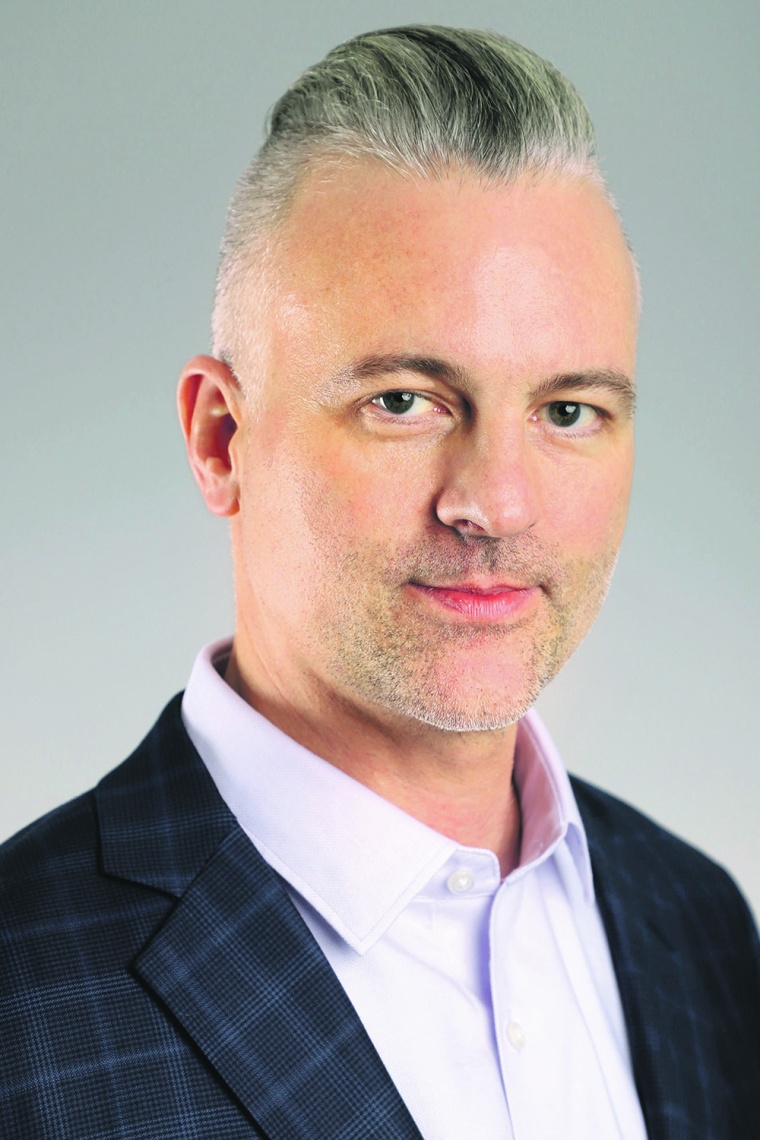
Continuous Manufacturing (CM) — also called Flow Chemistry or Micro Reaction Technology (MRT) — is a technique that has been gaining global importance over the past decade as a result of improved process control and reduced operating costs, leading to increased manufacturing profits and a competitive edge. Recent years have shown that the reason for a company to change from “batch” to “flow” have been varied, often depending on the sector, process type of interest and scale of operation. Supply chain security and improvements in process sustainability are strong emerging drivers for the adoption of CM.
With the product key, the infrastructure needed varies greatly and depends on the available chemistry, cost of goods, volumes required and the hazard profile of a transformation. The modularity and flexibility of continuous flow set-ups enables the development of small, agile production plants that can be used for the manufacture of multiple products — with easy re-configuration allowing for rapid product changeover.
Following on from this, the ease of replicating these small footprint systems represents an opportunity for manufacturers to develop a process and subsequently deliver production units across multiple countries to serve the local product demands. This is in stark contrast to the current approach of a single large-scale plant, with warehousing used to manage supply chain disruptions.
With all of these benefits, a logical question follows: Why the slow adoption of MRT?
CHEManager asked executives and industry experts to share their views on drivers as well as barriers for the use of flow chemistry and the prospect for this technology in their industry sector. We proposed to discuss the following aspects:
- In your opinion, what are the strongest drivers (success factors) of the implementation of flow chemistry processes?
- Which barriers are slowing down or impede the implementation of flow chemistry processes?
- What does it need for flow chemistry to be implemented more widely?
Although the pharmaceutical industry has historically relied on batch or semi-batch manufacturing processes for pharmaceutical ingredients, there is growing awareness of the benefits of continuous manufacturing using flow chemistry. These benefits include enhanced process safety through the more efficient removal of heat in flow processes compared to batch manufacturing, the ability to produce and rapidly react unstable or short half-life intermediates, as well as improving access to chemistry that has been historically challenging to scale-up in batch, such as photochemistry, electrochemistry, and high temperature/pressure processes.
In addition, small volume continuous manufacturing provides the flexibility of using a modular equipment footprint, where individual unit operations (including reaction, work-up extraction/distillation, and product crystallization) can be conducted on portable skids. This cost-efficient approach requires less manufacturing space, minimizes downtime due to equipment turnover, and supports like-for-like tech transfer, as the same equipment used for process development can be assembled or shipped for manufacturing.
“In the pharmaceutical industry,
there is growing awareness of the benefits of
continuous manufacturing using flow chemistry.”
Manufacturing with flow chemistry is also more amenable to the use of process analytical technology (PAT) tools to increase process control, reduce variability, and assure product quality. Looking to the future, the application of machine learning tools and artificial intelligence should also aid the development of self-optimizing reaction systems and automated process characterization based on modulating flow chemistry parameters such as temperature, feed rate, residence time etc.
In summary, due to the advantages highlighted above, global health authorities as well as the pharmaceutical industry and their partner (CDMO) organizations are increasingly looking to implement flow chemistry processes for the efficient preparation of high-quality pharmaceutical ingredients.