Expert Statement: Srividya Ramakrishnan, Dr. Reddy’s Laboratories
Executives and industry experts share their views on drivers as well as barriers for the use of flow chemistry in pharmaceutical manufacturing and the prospect for this technology in their industry sector.
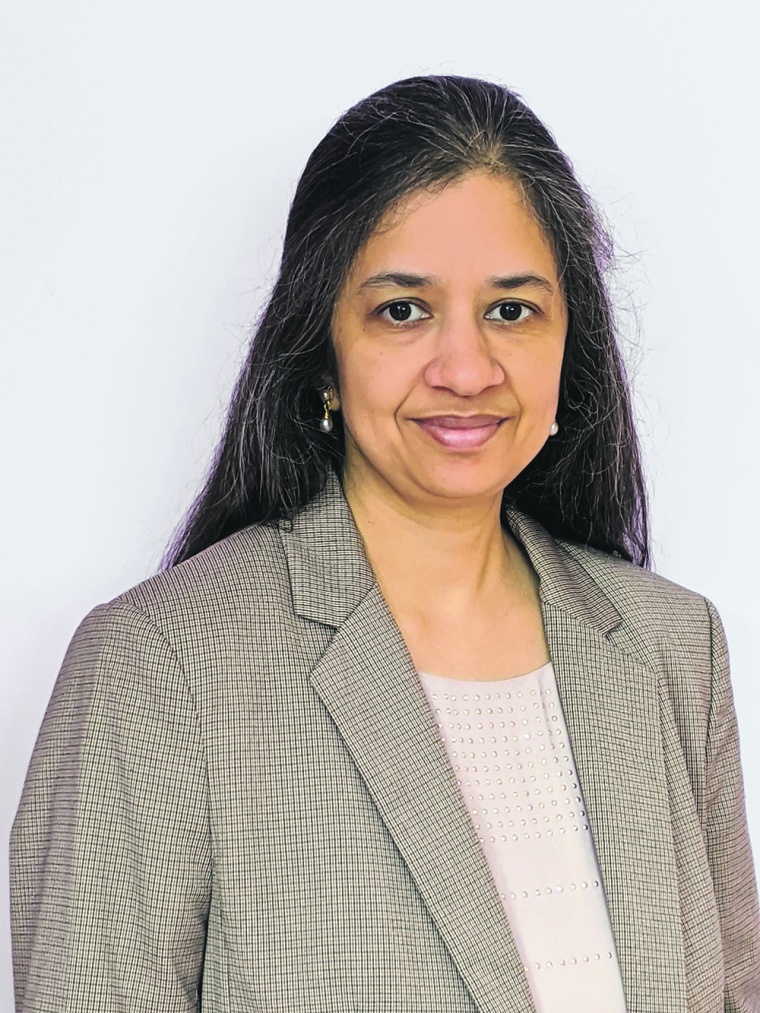
Continuous Manufacturing (CM) — also called Flow Chemistry or Micro Reaction Technology (MRT) — is a technique that has been gaining global importance over the past decade as a result of improved process control and reduced operating costs, leading to increased manufacturing profits and a competitive edge. Recent years have shown that the reason for a company to change from “batch” to “flow” have been varied, often depending on the sector, process type of interest and scale of operation. Supply chain security and improvements in process sustainability are strong emerging drivers for the adoption of CM.
With the product key, the infrastructure needed varies greatly and depends on the available chemistry, cost of goods, volumes required and the hazard profile of a transformation. The modularity and flexibility of continuous flow set-ups enables the development of small, agile production plants that can be used for the manufacture of multiple products — with easy re-configuration allowing for rapid product changeover.
Following on from this, the ease of replicating these small footprint systems represents an opportunity for manufacturers to develop a process and subsequently deliver production units across multiple countries to serve the local product demands. This is in stark contrast to the current approach of a single large-scale plant, with warehousing used to manage supply chain disruptions.
With all of these benefits, a logical question follows: Why the slow adoption of MRT?
CHEManager asked executives and industry experts to share their views on drivers as well as barriers for the use of flow chemistry and the prospect for this technology in their industry sector. We proposed to discuss the following aspects:
- In your opinion, what are the strongest drivers (success factors) of the implementation of flow chemistry processes?
- Which barriers are slowing down or impede the implementation of flow chemistry processes?
- What does it need for flow chemistry to be implemented more widely?
The strongest drivers are process safety, speed, cost, quality, and sustainability.
The enhanced mixing, mass and heat transfer in flow reactors, and the ability to precisely control the residence time and operate at extreme conditions provide an opportunity to explore novel process windows. Flow can boost reactions by running at temperatures and pressures considered unsafe in batch while significantly minimizing solvent usage. By controlling the residence time, the kinetics can be precisely optimized to increase the purity and decrease impurities.
The ability to intensify and handle hazardous reactions in flow significantly improves green chemistry metrics and reduces raw material costs, resulting in sustainable manufacturing at a lower price. With an effective control strategy, continuous manufacturing provides greater assurance on quality.
The biggest barriers are sunken capital and scarcity of talent. Considering the sunken capital into batch plants, any further investment into continuous may be difficult to rationalize based on return-on-investment alone. Hence, the benefits should be evaluated holistically to encourage adoption.
“The ability to
handle hazardous reactions in flow significantly
improves green chemistry
metrics.”
As this is an evolving technology, experienced talent is scarce and few undergraduate chemistry curriculums include flow chemistry.
At Dr. Reddy’s, we utilize flow chemistry for hazardous and cryogenic reactions, which are safer in flow and with lower operating expenses. We are also in the process of commissioning a modular plant for an intermediate to API process encompassing multiple reactions and unit operations. The driver to adopt this is a move towards sustainable manufacturing with improved green metrics, lower operating costs, and minimal manual operations. All this helps us in our mission to accelerate access to high quality and affordable medicines.