Plexiglas Offers a Raft of Automotive Solutions
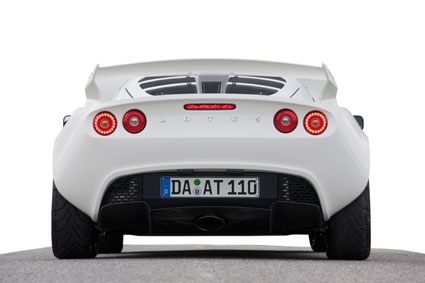
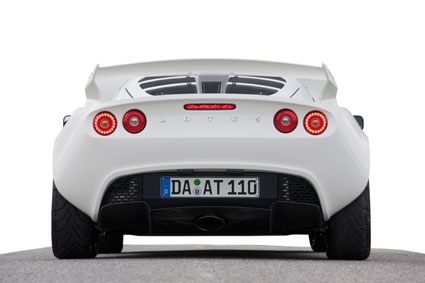
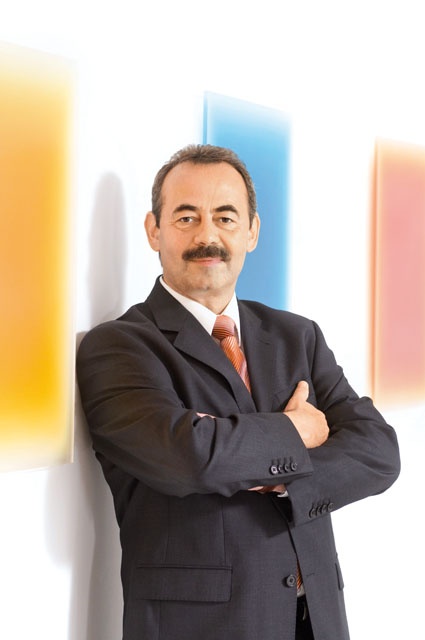
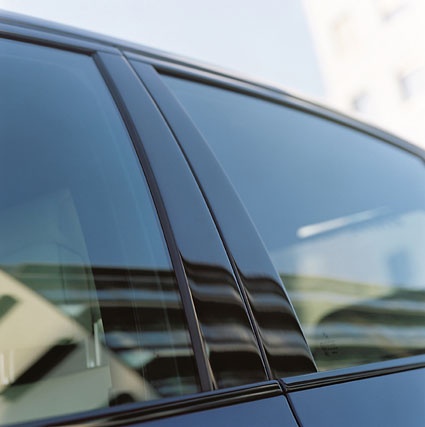
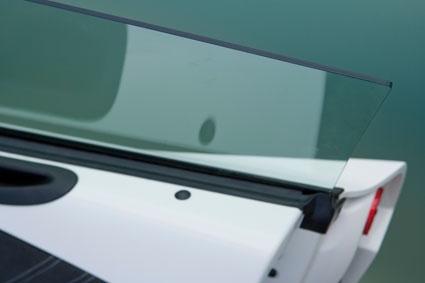
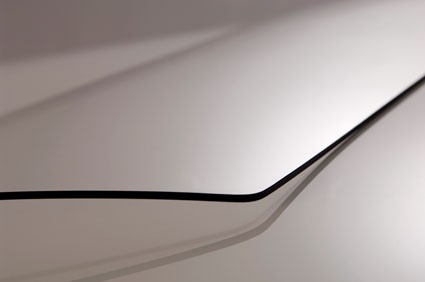
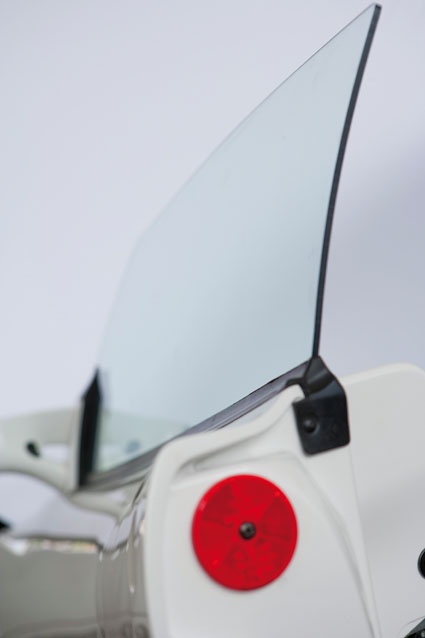
VIP - Visions In Plastics: The automotive industry is one of the most significant target markets. One main reason for this is the declared goal of automotive manufacturers to launch lighter-weight vehicles on the market.
Lightweight construction is an important prerequisite for reducing CO2 emissions and for electric cars. And Plexiglas stands for smart design solutions, in car interiors as well as for add-on body parts.
"Glazing made of Plexiglas is big at the moment," says Rudolf Blass, who is responsible for this sector in the Acrylic Polymers Business Line at Evonik Industries. "Plexiglas sheets are about 40-50 % lighter than conventional glass sheeting. This is obviously of great interest for car manufacturers. We have projects underway around the world," Blass says. A prototype of the Lotus Exige racecar with a windscreen and side windows made of Plexiglas has already hit the track several times, and the material is being used in a small Chinese car of the Chang'an brand that has gone into serial production, where it is used as a glazing element.
A Clear Advantage
The advantages are clear. Apart from weight saving, they include the excellent transparency of PMMA, its extremely high weather resistance and superior formability, which opens up entirely new design possibilities as compared with conventional glazing made of mineral glass. In taillights and turn signal lamps, the molding compounds have proven their worth for decades, not least due to their outstanding optical properties and colorfastness. And material developers are already one step ahead of the game. Their current focus is on integrating a variety of functions. IR-reflective glazing and integrated photovoltaic cells can already be installed in car roofs, for example. The heat-reflective property (the so-called Cool Touch effect) of the non-transparent material Plexiglas Heatstop has already been successfully put to use in a car roof. Altogether, non-transparent PMMA applications for automotive exteriors are highly popular, for example high-gloss black pillar panels, spoilers or mirror housings. These non-transparent exterior car body parts hit the market about 10 years ago, with the material setting new standards in this field. Meanwhile, more than 40 models by all well-known OEMs include non-transparent applications, partly because of the stylish appearance, but also because these parts are easier to produce and therefore more cost-effective for manufacturers. PMMA components with molded-in color do not need to be coated, for instance. What is more, to the delight of drivers, small scratches can be quite easily removed by polishing, unlike scratches on paintwork.
Freedom Of Design
Design also plays an increasingly important role in car interiors. Whereas the emphasis used to be on functionality, today, a classy appearance and pleasant haptic properties are major quality considerations. Many models, especially small cars, favor trendy interior design and colorful lifestyle features. PMMA molding compounds offer virtually boundless opportunities in this respect. There are many conceivable applications, some of which are already being mass-produced. These include PMMA instrument panel covers, central bevel covers, air nozzle covers or door handle recesses, or parts of the rear-view mirror. Here too, the costs compare favorably with other material variants.
But there are many other reasons for choosing PMMA molding compounds. Foremost among them is that decorative elements can be manufactured in any shape or color. Polished molds produce surfaces with brilliant gloss (Class A), whereas textured molds enable precise mold surface reproduction. Added to this, colored molding compounds, even when used in interiors, are economical to process. There is no need for coating or laminating, which saves up to 40 % of the component costs. And the material's high surface hardness prevents scratches. The CoverForm system solution is available for especially demanding applications. In this process, developed by Evonik and KraussMaffei, the component is sealed with an acrylate-based scratch-resistant coating while still in the mold. It is ready for installation straight from the mold, without any further fabrication. In addition to its high scratch resistance, this coating also offers very good chemical resistance. That is why components produced by the new process also pass the so-called suntan lotion test. It may come as a surprise to learn that these lotions can inflict substantial damage on plastic components and attack their surfaces in the long term.
Modern Lighting
Not surprisingly, lighting design is another issue that is coming to the fore in automotive interiors. After all, despite being technical and functional, cars are mainly meant to address the emotions. These are often the decisive purchase factor, and lighting design can go a long way towards brightening sales prospects. Light creates a special ambience that speaks directly to the senses. Evonik has given thought to this and developed a completely new grade of PMMA molding compound for car lighting: Plexiglas LED. It can be used in injection-molding applications for instrument panel lights, switches, navigation screens and much more. The light sources are energy-efficient LEDs (light-emitting diodes), which feed light into the components via their edges and provide extremely uniform illumination. This completely does away with disturbing hot spots. The molding compounds offer efficient light-diffusion properties for homogenous area lighting of the light guides required for interior automotive design, and create the desired atmosphere.
As these examples show, PMMA remains the material of choice in the automotive sector, both for interior and exterior applications. This is due to its virtually unlimited creative possibilities and excellent functionality. So the industry can wait with bated breath to see what Plexiglas will come up with next.