Revolutionizing Green Chemical Production with Ultrasound
Biorefining allows low-carbon feedstocks – such as lignocellulosic biomass – to be processed into intermediate chemicals that can be made into renewable plastics for the automotive industry. Sonichem has developed a breakthrough biorefinery technique that uses ultrasonic energy alongside mild organic acids to fractionate softwood sawdust into hemicellulose sugars, microcrystalline cellulose and high-quality lignin.
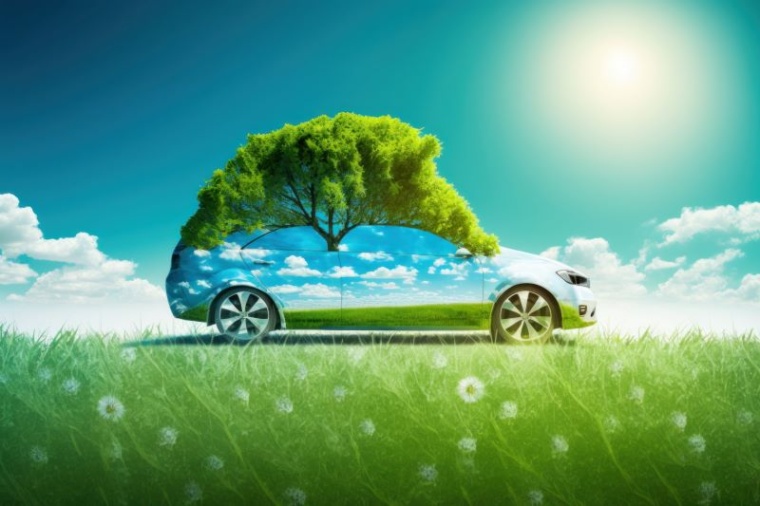
Biorefining offers an answer for vehicle manufacturers, allowing low-carbon feedstocks — such as lignocellulosic biomass — to be processed into intermediate chemicals that can be made into renewable plastics. This approach has the potential to replace fossil-derived chemicals and lower carbon emissions during automotive production. However, existing biorefining technologies are often inefficient, wasteful and unprofitable, using energy-intensive processes that consume large volumes of toxic petrochemical-derived acids and aldehydes. Ironically, these methods generate significant greenhouse gas emissions that make them environmentally unsustainable.
Exploring the Potential of Ultrasonics for Sustainability
Sonichem Technologies is a small UK company founded with the aim of converting woody biomass into green platform chemicals using ultrasound. The company’s breakthrough biorefinery technique uses ultrasonic energy alongside mild organic acids to fractionate UK-sourced softwood sawdust into its three main constituents: hemicellulose sugars, microcrystalline cellulose and high-quality lignin. This sawdust is a by-product of sustainable forestry operations, and would otherwise simply be burned or left to rot, releasing all the stored carbon back into the environment. Conversely, all the biomass that enters the Sonichem process is upcycled into pure platform chemicals with virtually no waste. The ultrasonic technique also requires significantly less energy than conventional fractionation methods, resulting in green chemicals with a low carbon footprint.
The renewable hemicelluloses, microcrystalline cellulose and lignin generated by this innovative process can be used as additives or low-carbon feedstocks for green platform chemicals to manufacture renewable plastics for a wide range of applications. For example, the hemicelluloses — sugars that provide flexibility and integrity to plant cell walls — can be dehydrated into furfural, a compound that confers properties such as corrosion resistance, thermosetting and physical strength to furan resins. They can also be used as a polyfurfuryl alcohol (PFA) precursor to help multiple sectors, such as the construction industry, become more sustainable. Hemicellulose sugars can even be converted to other high-value building blocks — including xylitol and sorbitol for pharmaceutical, dental care, and food and beverage applications — and show promise as feedstocks for production of bio-based surfactants, films, natural dyes and renewable jet fuel.
Microcrystalline cellulose has strong binding properties, making it a reliable filler and excipient in pharmaceutical formulations, personal care products, performance composites, and foods and beverages. Cellulose is also routinely modified at a huge scale in the chemicals industry to create building blocks for the production of packaging films, adhesives, sealants and even explosives. It can even be broken down further into glucose for use in fermentation, flavor and fragrance, and fuel applications.
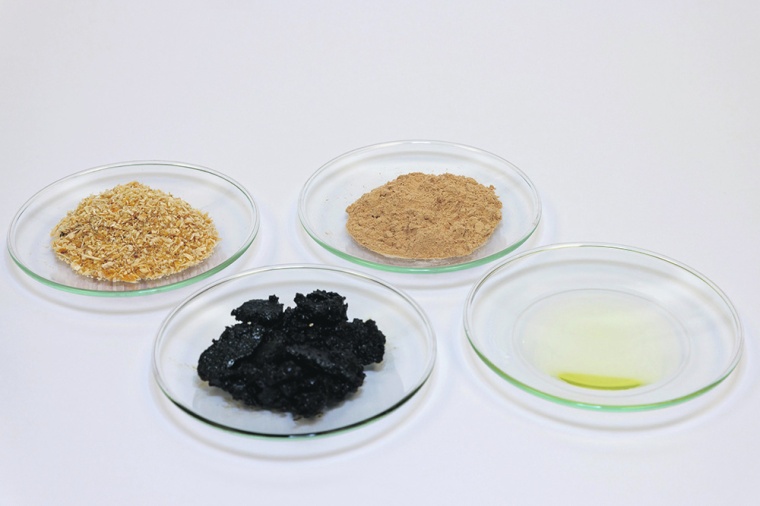
The Limitless Potential of Lignin
Arguably the greatest value of this unique ultrasonic fractionation process lies in the production of high-quality, sustainable lignin. Lignin is the world’s second most abundant renewable biopolymer, and is also the only known aromatic polymer found in nature, making it a plentiful and low-toxicity alternative to the finite feedstocks made from petrochemicals. Lignin is extremely versatile, possessing innate hydrophobic, flame-retardant, antimicrobial and UV-resistant properties, and can be added to industrial composites to confer these benefits and improve flow. The material is also known as nature’s binder, and can be used instead of certain fossil fuel-derived chemicals — such as the toxic petrochemical phenol — to produce resins for composites, including those required to build wind turbines. Demand for bio-based platform chemicals for this application in particular will only continue to grow in the coming years, as more countries seek to transition to renewable energy sources.
Sonichem lignin is different from the lignin obtained using the conventional Kraft process. Kraft lignin contains sulfur, which corrodes metals — such as processing equipment and steel reinforcement bars embedded in cement — raising safety concerns as well as environmental issues. It is also very high in molecular weight, giving it low solubility. Consequently, Kraft lignin is challenging, time consuming and expensive to process into useful products, with goods produced using Kraft lignin often demonstrating inferior mechanical properties. Sonichem lignin, on the other hand, has a very low molecular weight — one of the lowest in the world — is of high purity, and does not contain any sulfur. These features give it high reactivity and solubility in a host of common solvents — such as ethanol and acetone — and polymers, for instance in the production of bioderived carbon fibers.
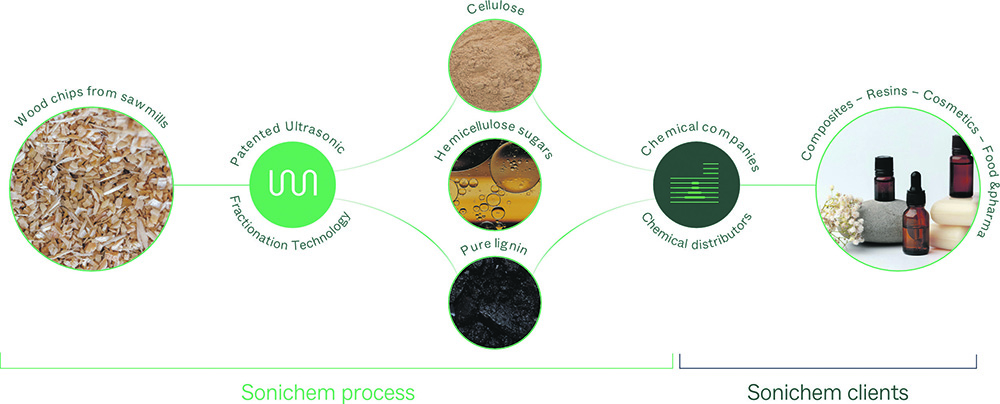
Sonichem’s biorefinery technique uses ultrasonic energy alongside mild organic acids to fractionate softwood sawdust into hemicellulose sugars, microcrystalline cellulose and high-quality lignin. © Sonichem
Driving Change in Automotive Manufacturing
Sonichem has recently launched an international project in collaboration with industry leaders CPI, the National Composites Centre, Scott Bader, SHD Composites and Polestar. The project, entitled ‘Carbon-neutral agroforestry-derived resins to materials for automotive applications (CARMA)’, will apply Sonichem’s patented technology to the development and commercialization of bio-based feedstocks made from the company’s high-quality lignin. These feedstocks can be used in the production of sustainable, cost-effective replacements for the platform petrochemicals that are currently used to produce plastics, resins and composites for automotive manufacturing. CARMA will extend Sonichem’s pioneering ultrasound approach to the transport industry, driving the sector toward net zero, enhancing the UK’s bioeconomy, and helping to establish a resilient national lignin supply chain. Producing home-grown green plastics also aligns with the UK Government’s focus on resource-efficient, sustainable industrial materials, as it could significantly reduce the UK’s reliance on imported composite materials, which currently amounts to approximately £250-260 million per year.
Trailblazing ultrasonic technology has the potential to enable large-scale green chemical production across the UK, supporting bio-based plastic manufacture for use in multiple applications. The high-quality, bioderived chemicals generated through Sonichem’s revolutionary technique could help to decarbonize numerous industries, reducing the nation’s reliance on polluting, finite petrochemicals.
Authors: Adrian Black, CEO, and Andy West, Chief Chemist, Sonichem Technologies Ltd., Southampton, UK
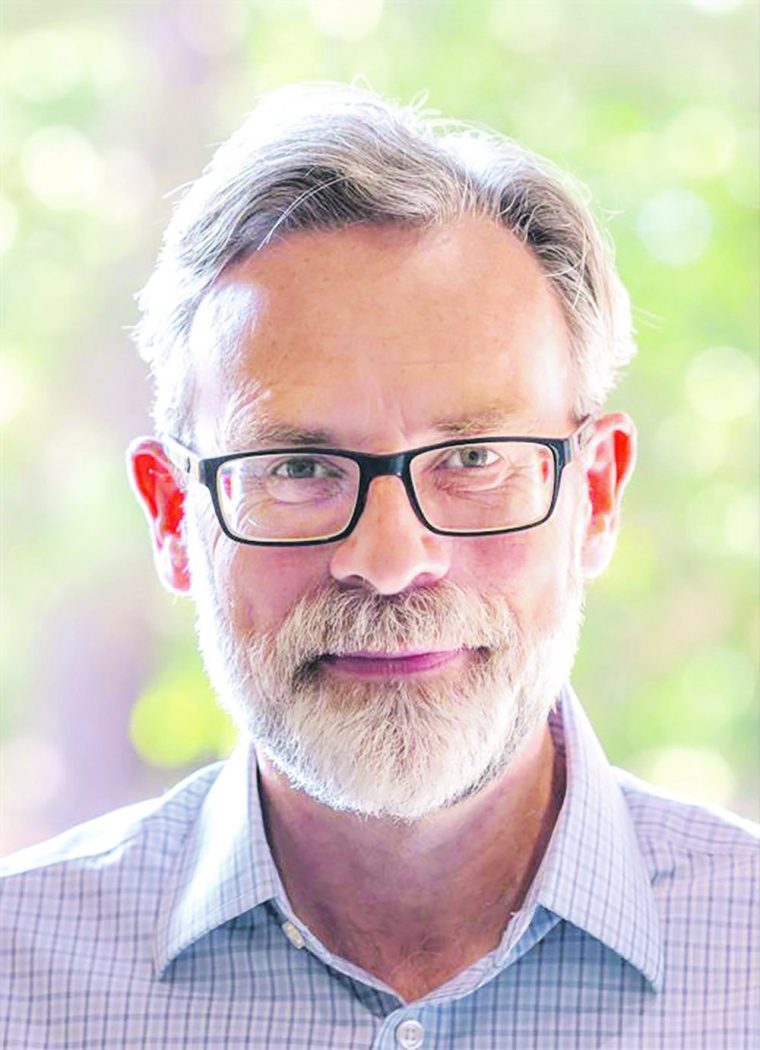
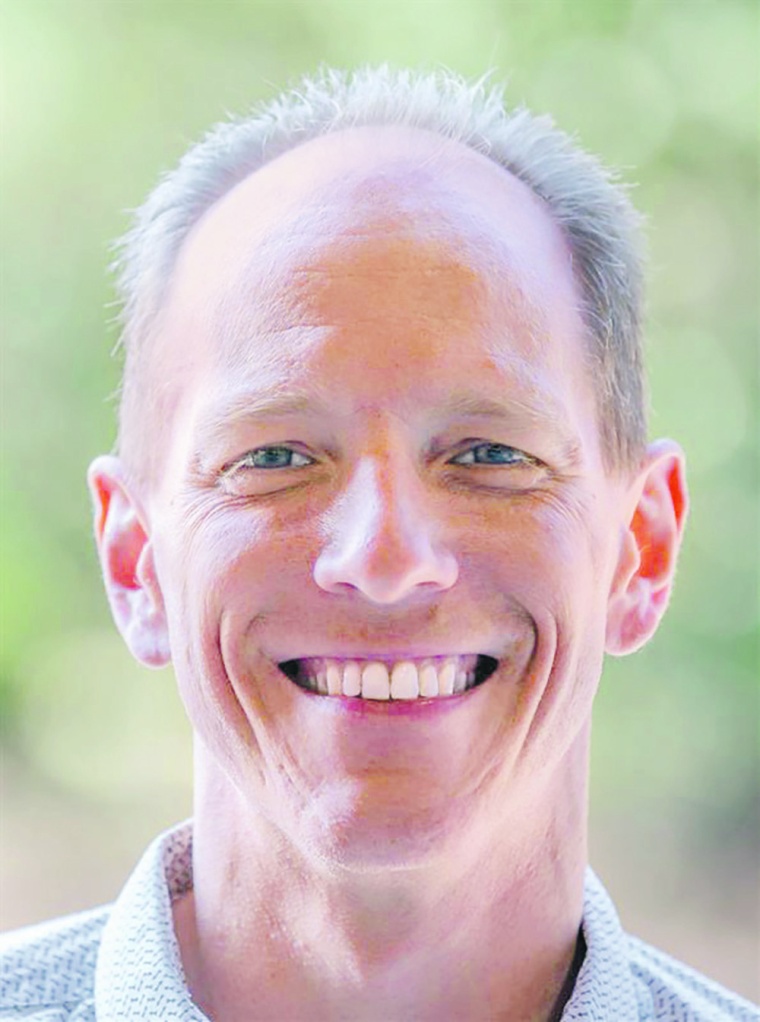