Tune Your Warehouse
The changes in customer needs and market requirements have not only been changing because of the pandemic influences within the last year, but traditional business models were quickly considered outdated in the current environment.
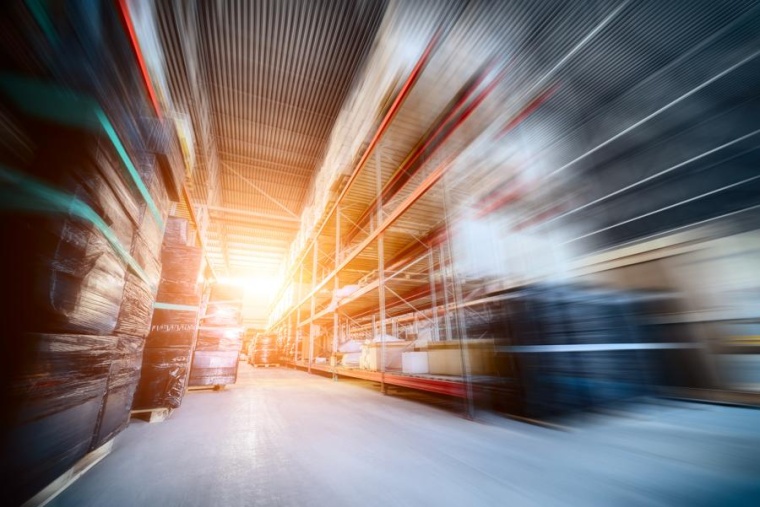
The ones who have an adaptable warehouse and distribution concept are now pleased to react flexibly to the future needs. But what happens to those who struggle with outdated technical equipment, old IT systems, or even both?
There is a way to solve this challenge if you combine technological and logical measures — even in areas with high regulatory constraints like in the pharma & life science industry! But what should you actually do if your warehouse no longer meets customer and market requirements?
Some of our clients in the last almost 50 years claimed that they needed a warehouse extension but did not have the budget for it. They did not believe that smaller steps would be able to help to improve their logistics situation.
Very often the logic is: “If the warehouse reaches the capacity limit, intelligence can’t make the pallets smaller, fewer of them, or the warehouse bigger, as we do not have the power to influence the stock level itself!” This is often followed by the opinion that additional intelligence, algorithms and logic only help to suggest rearrangements, but the potential is not real, as “the old technical equipment will not be ready for this technological leap”. This view of the situation will become a self-fulfilling prophesy unless one starts looking at it in a more holistic way: It is not solely the planning, the logic, or the techniques, but the joint approach that is able to improve logistics significantly.
The first approach for reducing stock levels is not in the influence of the warehouse managers, but e.g., in changes of market demands, sourcing strategies, and internal alignments — especially for work in progress.
Implement Changes
The answer for optimization of these factors can be given by a resilient simulation study in a digital twin, where stock levels can be optimized in a multi-echelon approach, integrating the different levels of supply in the digital twin to prove how much the risk level changes and what kind of stock level is truly needed — instead of increasing stock levels based on the gut feeling of human planners.
But to implement the changes in daily work, the acceptance of staff (especially at the planning level) is needed first. In order to get this acceptance all processes should be aligned with a decent and integrated S&OP approach (Sales & Operations Planning), or better, with a full IBP integration (Integrated Business Planning). To learn this new way of working cannot be done overnight and requires proper change management. This does not mean to set up hasty training sessions shortly before going live after a decision has been made, but accompanying the whole process of change “with the people” and not “against the people”, gaining acceptance and buy-in on the changes right from the conceptual level. Finally, more important than to teach the new processes is to make the staff to “unlearn” the old ones.
If these kinds of optimization potentials are utilized, the next step should lead to a retrofit and/or tuning of intralogistics automation. This part of retrofitting and tuning of the existing logistics center or the existing automation is a cost-optimal and efficient alternative to new construction. The optimization includes processes and existing IT solutions, space, warehouse technology as well as people & organization.
For the logistic optimization with a retrofit/tuning, the following issues could be addressed in questions like:
How can we get additional throughput?
Some examples of how this can be done include: shortcuts in conveyors, partly automating heavily loaded bottlenecks, or HRC (human robot collaboration) in selected areas with the help of an AGV (automated guided vehicle), or even AMRs (autonomous mobile robots). The effectiveness should be confirmed beforehand by a simulation in a digital twin which avoids misinvestments.
What are the typical quick wins to get additional capacity?
Discussing or challenging the stock level with other departments regarding sourcing strategy, etc., should be the first step. If not fruitful, then the already mentioned Multi-Echelon Inventory Optimization (MEIO, again based on a digital twin) will help to confirm the results and convince the concerned colleagues that other parts of their network can act as a backup. But if all of the above mentioned does not help, then the physical modifications of warehouse and/or racking have to be considered, like changing the height of pallet locations to avoid “dead space”, or even thinking of a higher-density storage technique (of course always depending on throughput demands).
Which systems and technologies need to be replaced to ensure the availability of the overall system, and which approach fits best to my goals?
This question is not easily answered, especially regarding which kind of new technology to choose. The best answer is a clear: “it depends!” since the answer definitely demands a deeper analysis to fit to the specific needs of the situation.
Some of the new technical possibilities will bring benefits, especially when processes are supported by Cyber Physical Systems (CPS) for a smart relieve of people from manual workload. Workstations, workpieces and transport equipment are networked in such a way that they communicate with each other and prepare the next process step. Production planners monitor progress and only intervene in the event of deviations.
Previous steps in development of these systems were done by supporting elements like pick-by-technologies (pick by light, pick by voice or pick by vision using smart glasses). New possibilities are also offered by intelligent load carriers, which always know their stock and re-order independently if necessary.
Warehouse and production are connectable by internal transport. Autonomous forklifts allow automatic unloading of goods deliveries. AGV/AMR navigate independently optically or by laser. New generations of technologies are more easily adaptable then the ones before. Implementing an AGV (automated guided vehicle) was much more complicated than an AMR (autonomous mobile robot) which is not dependent on fixed routes, is a simpler installation and is able to reroute if unknown obstacles block its path.
How is the implementation carried out during operation and how can we make sure that transition goes smoothly?
This question is one of the most crucial ones to be aware of before the implementation starts and while the transitional concept is developed. While there is no standard procedure, there is one common step: Simulate the changes in your digital twin before the implementation starts and confirm the feasibility with established service-levels in order to safeguard your investments and rocesses.
Successful optimization begins with a holistic view of processes, IT solutions, technologies and people & organization. Miebach uses simulation as the best way to quickly examine capacities and obstacles, weaknesses and potentials of these cost and value drivers. The simulation and data analysis tools support our clients in determining the optimal adaptation of your existing system and its effects on the overall network.
But all in all, a digital twin will become a central component of the ongoing digitization and optimization of processes. It continually presents a virtual copy of the logistics, the production system and the products. This means that order status, machine availability, stock levels, transport capacities, current position, processing status, quality defects and other information can be called up at any time. Changes to the real system can be realistically tested on the digital twin at any time in advance, and that ability will be a “must have”.
Be sure to include internal experts or an external partner when planning or implementing your warehouse tuning and/or retrofit. An external partner should have experience supervising the entire retrofit and tuning process from design through go-live in multiple projects, as each is unique. Your goal is to improve your performance, and not beta-test a new technology for an integrator.
Author: Achim Sponheimer, Partner & Head of Pharma, Miebach Consulting GmbH, Frankfurt am Main, Germany
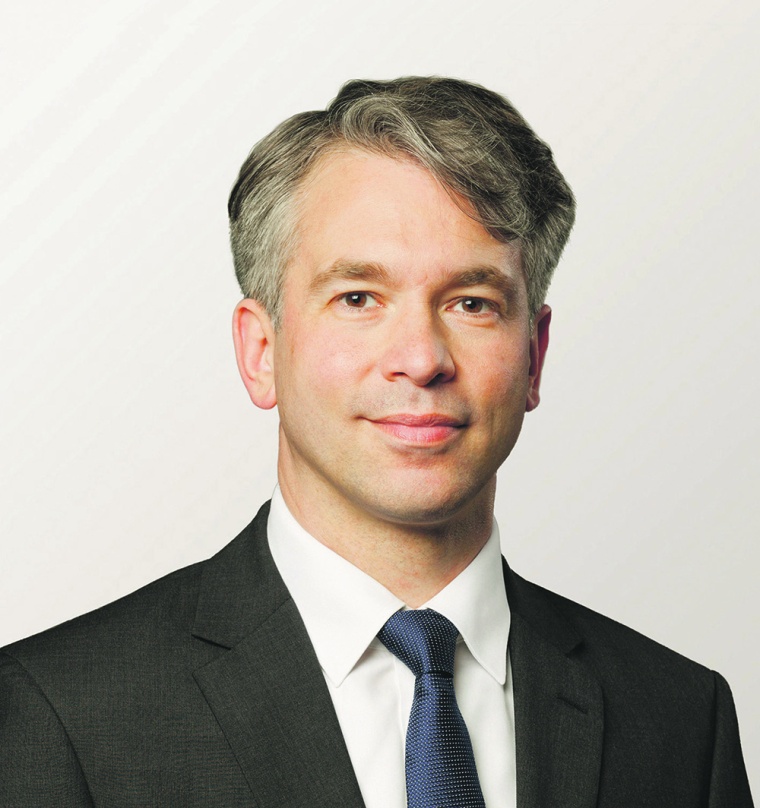
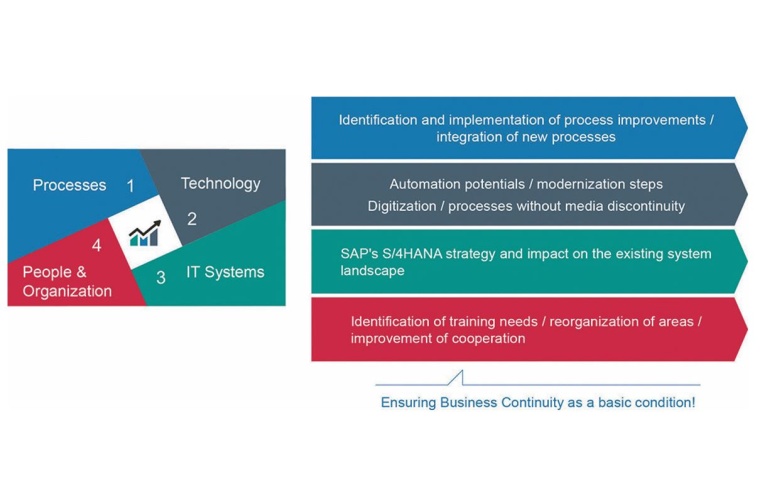
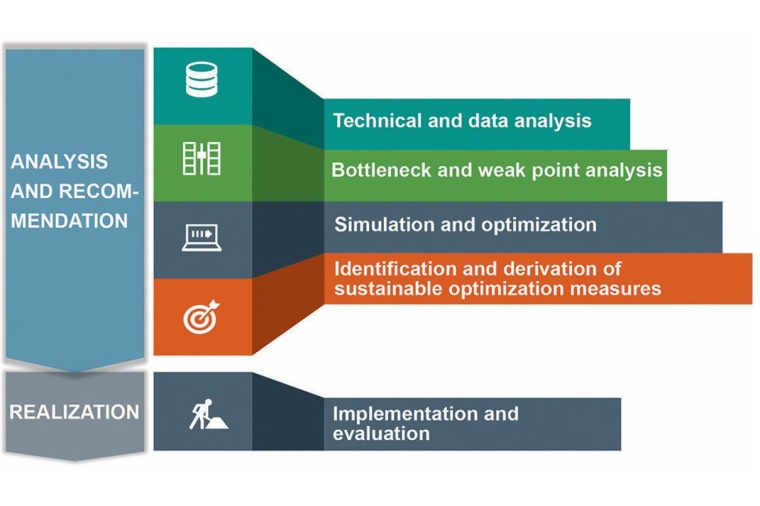
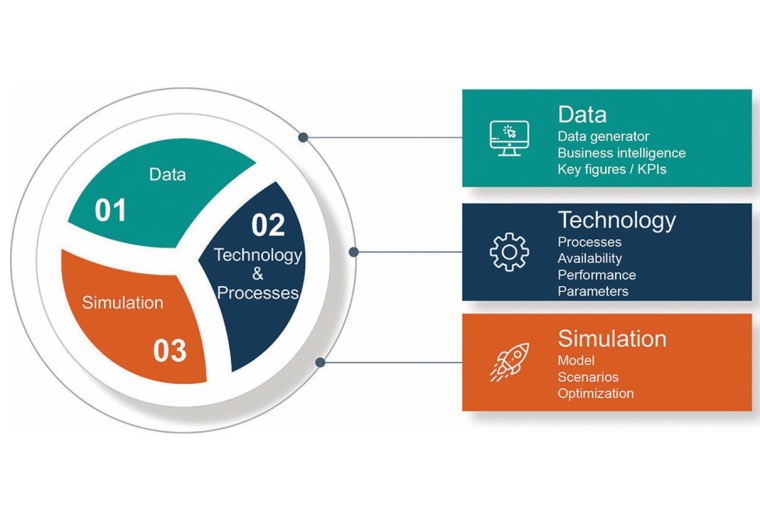
most read

MSD to Acquire Verona Pharma for $10 Billion
MSD, known as Merck & Co. in the US and Canada, recently announced it will acquire Verona Pharma, a biopharmaceutical company focused on respiratory diseases, for approximately $10 billion.
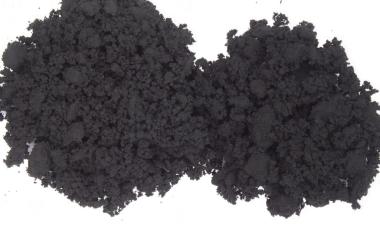
Orion Announced Plans to Shut Down Carbon Black Plants
Carbon black manufacturer Orion Engineered Carbons plans to rationalize production lines in North and South America and EMEA.

Ineos Invests £30 Million to Slash Emissions at Hull Site by 75%
Ineos has completed a major £30 million investment at its Hull manufacturing site, converting the facility to run on clean-burning hydrogen instead of natural gas. This results in a 75% cut in carbon emissions.
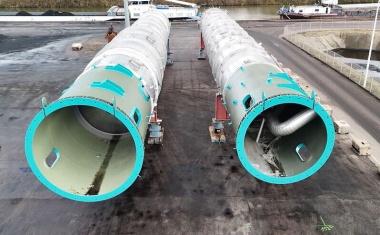
Arkema Launches Acrylic Acid Purification Project
Arkema has announced the launch of its Carat Project at its Carling site in France. This initiative aims to enhance the capabilities and sustainability of the facility, which specializes in producing acrylic monomers and superabsorbent polymers.

BASF Divests Two Joint Ventures in China
BASF has divested its shares in the joint venture companies, BASF Markor Chemical Manufacturing (Xinjiang) Co., Ltd. and Markor Meiou Chemical (Xinjiang) Co., Ltd. in Korla, China, to Verde Chemical Singapore Pte. Ltd.