Well Prepared for the Future with Supply Chain Assessment
Interview with Klaus-Peter Jung, Partner at the Miebach Consulting Group
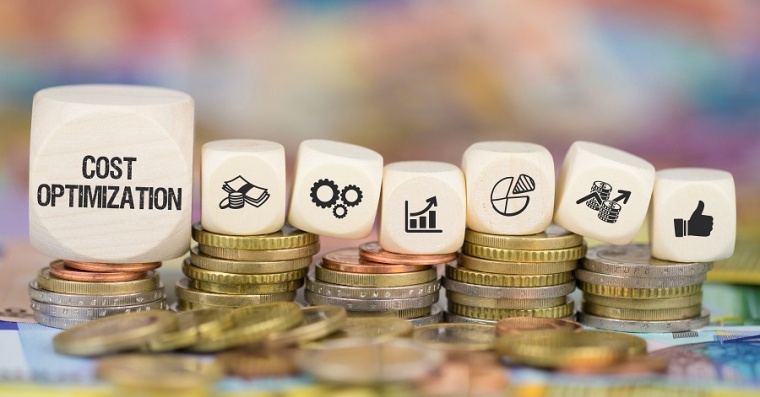
Due to the current very challenging economic and geopolitical situation, cost-cutting measures seem unavoidable for many companies. The German chemical industry is also feeling the massive headwind and is preparing for the onset of the downturn with cost-cutting programs, some of which are worth millions. But which measures make sense? Which will have a lasting effect and not just postpone necessary investments for the future? CHEManager asked Klaus-Peter Jung, Partner and Head of Industry for the Chemical Industry, Beverages and Logistics Service Providers at the Miebach Consulting Group, about a possible solution, the Supply Chain Assessment. The questions were asked by Birgit Megges.
CHEManager: Mr. Jung, where do most companies start their savings programs?
Klaus-Peter Jung: The desire for savings programs is great, and so is the need in some companies — but many companies quickly run out of ideas after the usual measures, such as restricting travel expense policies and the employment of consultants. The bigger question is how and where costs can be reduced, even in the short term, without laying off well-qualified personnel in exchange for high severance payments, which will be lacking again in six months or a year due to the shortage of skilled workers.
Many purchasers are currently finding out that pushing down purchase prices while facing persistent inflation and rising personnel and energy costs is quickly reaching its limits.
So where do we start? Many companies in the chemical industry are currently sitting on high inventories of raw materials, packaging and finished goods — still resulting from the pandemic. Due to the current reduced demand in some segments, „replenishment freeze“ — where it can be implemented — is particularly effective in the short term. In addition, the impending crisis provides sufficient reason to rethink core issues such as the production footprint, the distribution network, and portfolio complexity.
„Not carrying out optimization projects now simply means postponing their positive effectiveness by months or even years.”
In your experience, why are the measures taken in many cases not effective in the long term?
K.-P. Jung: Many measures are aimed at postponing necessary actions to avoid cash out today. While this is effective in the short term, it only postpones growth, optimization, or capacity problems to the near future where they will be magnified when the economy strengthens again. Not carrying out optimization projects now simply means postponing their positive effectiveness by months or even years. Investment projects in the chemical industry usually have a planning and implementation horizon of several years — to suspend them now means that the necessary capacities will not be available when demand picks up again.
The situation is even more serious when it comes to staff reductions — these usually cost considerable amounts in the short term in order to free up employees who will then be desperately sought on the market again in 6 – 18 months and not found due to the shortage of skilled workers.
What does your approach look like?
K.-P. Jung: One starting point can be a supply chain assessment, the aim being to identify and implement starting points for holistic cost optimization in the supply chain. In this process, all the stones are turned over and examined to determine the extent to which savings potentials are slumbering there, and how these can be leveraged within a manageable period of time.
For example, the focus can be the procurement, production, or distribution network, but also all supply chain processes from planning to purchasing and inventory management to service provider control. This is agreed individually with the customer in order to develop and implement concrete measures quickly and efficiently.
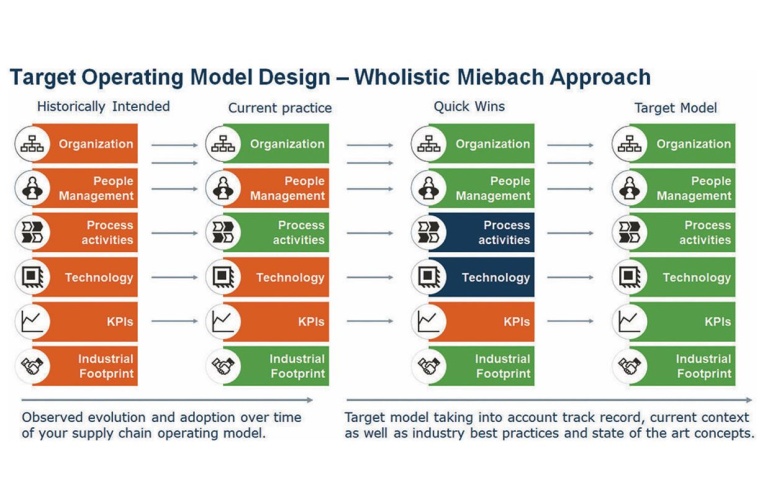
Can you explain in detail your approach to holistic cost optimization in the supply chain?
K.-P. Jung: The background of the supply chain assessment is the analysis of the existing so-called target operating model, consequently of the entire set-up or the „production system supply chain management.“ As a rule, an analysis is carried out in the following dimensions: First, organization including interfaces and degree of centralization; second, employees, their qualifications and their skills; third, supply chain processes; fourth, technologies and tools such as planning tools, control towers or dashboards; fifth, KPIs and reporting; and sixth, the industrial footprint, by which network and partners are meant.
These dimensions describe the target operating models in supply chain management and exist — intentionally or unintentionally — in every company. The first three criteria describe so-called qualitative soft dimensions, while the last three are aimed at quantifiable hard dimensions. Short-term cost saving potentials are mostly oriented towards the latter hard dimensions, but optimization of these is usually not possible without taking the first three criteria into account. Therefore, the approach is set-up for a holistic cost optimization.
“In most cases, a multi-stage approach is chosen, with short-term cost reductions as quick wins in the first step and medium-term development potentials being addressed in a second step.”
In most cases, these aspects were once defined in terms of how they should be lived, these are called Historically Intended. Deviating from this, an actual state has emerged over time, referred to as Current Practice, which partly still corresponds to the formerly defined state, and partly differs from it — whether positively or negatively.
The supply chain assessment analyzes both the defined and the actual state and, based on this, identifies both quick wins that can be realized in the short term and optimization potential that should be aimed for in the medium term, or target model. In addition to the current track record — what is working well and should be retained versus what is not working well —, current conditions, for example, planned conversion to S4 Hana prohibits measure XY in the short term, industry best practices and state of the art concepts are considered.
These are a number of criteria that need to be analyzed. How do you ensure that the evaluations are not arbitrary?
K.-P. Jung: This is not done arbitrarily, but by means of a standardized scale. Based on the research and consulting firm Gartner, so-called maturity levels have been defined for a wide variety of dimensions and processes, which enable an objective evaluation and classification of the company. Thus, in each project, there is usually an evaluation not only by the external party but also an internal assessment of the status quo by the customer.
The determination of which quick wins can be implemented in the short term and which level of maturity should be aimed for in the medium term is also worked out together with the customer. In most cases, a multi-stage approach is chosen, with short-term cost reductions as quick wins in the first step and medium-term development potentials being addressed in a second step. Together, we work out what effects will result from further development and how these should be structured in terms of both content and timing.
In which areas of a company can this type of assessment be applied?
K.-P. Jung: The implementation of this assessment can be extended to all supply chain processes, be it purchasing, production planning, inventory management, S&OP or customer service. Cost reduction potentials usually arise both in the process itself, such as the reduction of resource requirements or the avoidance of interface losses, as well as in the result of the optimized processes, for example by increasing the quality of the planning results, the improvement of capacity utilization or the reduction of working capital.
Have you already been able to gather experience that proves the success of the approach?
K.-P. Jung: Concrete project examples have impressively demonstrated the short-term effectiveness of a supply chain assessment. Short-term savings potentials that do not jeopardize medium-term success were identified, for example, in the tool-supported centralization of supply chain planning processes or the reduction of „Covid inventories“, and medium-term savings potentials were identified in the review of the production footprint with greater specialization of individual locations.
It is particularly important to emphasize that not only individual aspects are considered and may counteract other measures or framework conditions, but that short-term optimization is in line with a medium-term target operating model in order to master the feared crisis, but also to be well prepared for the subsequent upturn.
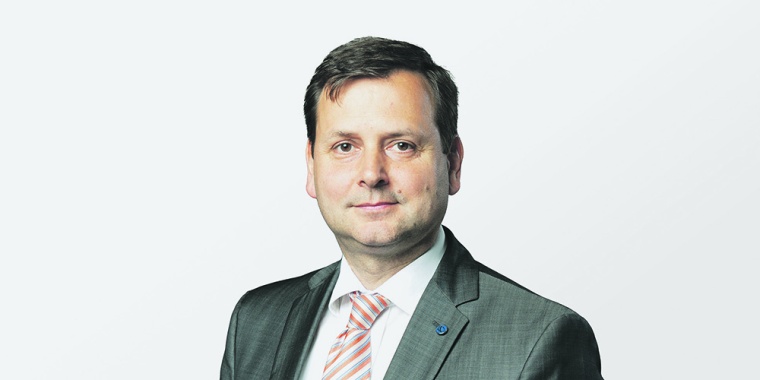
Klaus-Peter Jung is Partner and Head of Industry for the Chemical Industry, Beverages and Logistics Service Providers at the Miebach Consulting Group. Jung joined Miebach Consulting in the year 2000, after receiving his doctorate at the University of Marburg in the chair of Logistics. For more than 25 years he has been advising clients in supply chain and logistics on a national and international level. His consulting mandates include well-known companies in the logistics sector, the chemical industry and international manufacturers from the breweries and soft drinks sectors.