CESIO 2019: Performance – Solution – Success – Surfactants
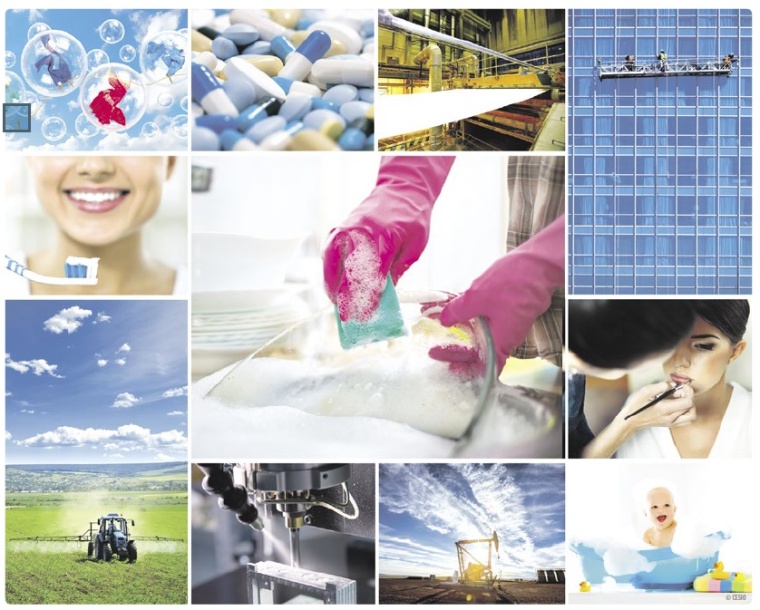
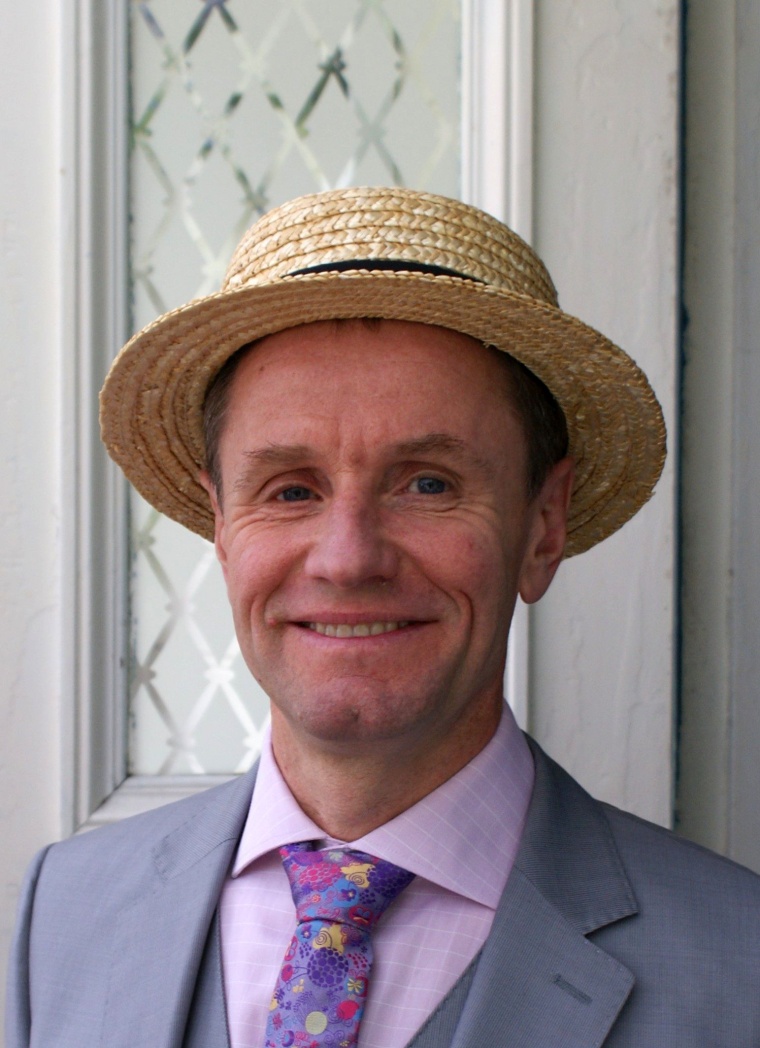
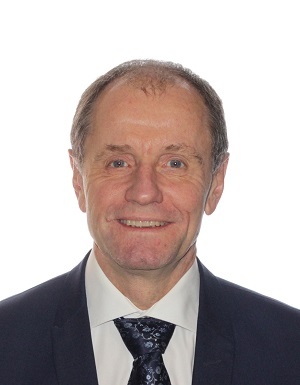
Surfactants are used in a wide spectrum of applications — from detergents to crop protection, from cosmetics to the oil & gas industry. This broad range of use, among other things, will be at the center of interest of the 11th World Surfactants Congress to be held in Munich in early June 2019. Exactly 35 years after the first World Surfactants Congress held in 1984, Munich will again host this event organized on behalf of CESIO, the European Committee of Organic Surfactants and their Intermediates. CESIO 2019 will be a combination of a scientific congress and a business convention. In the run-up to the event, Michael Reubold asked Staffan Asplund, president of CESIO and Surfactants R&D Director at Nouryon, to provide a status report on the surfactants business and technology, as well as a sneak preview on what will be discussed in Munich.
CHEManager: Mr. Asplund, what is the point of departure, so to say, for the surfactants industry to meet at CESIO 2019, how do you characterize the current market situation?
Staffan Asplund: What we can derive from the published production figures of our industry, the overall market situation for surfactants in Europe is stable, with limited growth in specific areas. This situation has been consistent the past few years. But if we see into the different surfactant groups and fields of applications, there is a general trend from commodities to specialty surfactants, which makes it even more important to develop surfactant systems that are specifically focused on the customer’s need.
How have the global and the European market for surfactants developed in recent years and what are your growth expectations for the years to come?
S. Asplund: Whether there is a recession or a peak in our business trends, the consumers still need food, do their laundry, wash the dishes, use personal care products and wear textiles. They may spend more money in a booming situation and buy less or cheaper products in a downturn, but we can say that the overall surfactant market in Europe is a mature business with modest volume growth.
New capacity has come on stream but the trend from commodities to specialties has led to more complex chemistries requiring more processing time, which has compensated the growth and stabilized the total output of surfactants on a high level.
Nevertheless, our growth expectations are “restrained positive” — in the past we have discovered new applications for existing surfactants and the industry continues to innovate in this way.
We develop new business models that are not necessarily based on growing volumes, but on higher effectiveness and quality of the surfactant systems.
The congress theme of CESIO 2019 is "performance — solution — success — surfactants". Why did you pick this theme, what is the story or message?
S. Asplund: Surfactants in solutions and at interfaces — scientifically just fascinating! But surfactant science is not an end in itself — surfactants are the basis to solve challenges involving all kinds of interfaces and applications. Surfactants are the key to providing successful solutions for consumers, e.g. related to cosmetics or household applications, or for professional uses such as I&I or agrochemicals and many others. This is because surfactants, are fundamental to achieving the desired product performance. And just as surfactants work across interfaces, so innovation happens at interfaces, not only between the science and application, but also between different disciplines and applications. That is why it is crucial to meet and communicate across borders!
The reason why we have chosen the motto for our CESIO 2019 congress as “performance — solutions — success — surfactants” is to demonstrate that there is an ongoing process in our industry to better understand the application conditions of the future surfactant value chain.
Because of their versatility and performance, surfactants have a very large range of applications. What are the most important in terms of market value?
S. Asplund: More than 50% of the surfactants which are sold in the EU are used for household detergents, by far the largest application in terms of volume and total market value. We assume that approximately 10% are used for personal care as well as for textile finishing. Another 5% are I&I application — so we can say that three quarters of the total volume are sold to four fields of applications. The remaining 25% are used in many specific applications, e.g. crop protection, leather and paper manufacturing, oilfield or the construction industry. In terms of sales value, the picture is quite similar, though specialized performance products tailored to specific applications will trade at a higher unit value.
Do you see a trend among customers to reduce complexity of product formulations and reduce the use of surfactants?
S. Asplund: The more complex the product formulation, the more surfactants are needed as key ingredients that help to combine substances, which otherwise would be incompatible or adversely affect the components’ value. In the field of household detergents, our customers have been quite successful in substituting some chemicals in their formulations by enzymes. Many producers of surfactants have started to test and develop systems that contain surfactants together with enzymes. In other applications, customers are looking for processes and formulations that are more energy-efficient and need less resources overall, like crop protection requiring less active ingredients to achieve the same result or recycling road surfaces to save on energy and natural resources. These challenges demand better insight into the interaction of surfactants and other ingredients, and this in turn opens up new opportunities.
What are the main drivers of surfactant innovation and what will it need to take advantage of them?
S. Asplund: Surfactants are used in many applications, each with their own drivers, so it is really a multitude. Trying to generalize a bit, there are a few clear trends: eco-friendly solutions and bio-based products is an important trend although surfactants have been made from bio-based raw materials for many years. Related drivers are sharper regulations and voluntary certifications like eco-labels, providing clarity and confidence to downstream users in a variety of markets, including cleaning, personal care, asphalt and agrochemicals. Also important are solutions that allow users to use less resources, be it material or energy. Examples include low-temperature cleaning, laundry technology with reduced water use and more energy-efficient industrial processes. To successfully capitalize on these trends, surfactant suppliers will need a thorough understanding of their target applications as well as the ability to innovate in collaboration with customers and technology providers.
What fields of applications do you consider as being in the focus of research and development, what are currently the hot topics in surfactants R&D?
S. Asplund: As indicated above, there are many “hotspots” as surfactants are essential chemicals in many formulations and industrial processes, it is difficult to pick out just a few. An important overriding theme is the deeper understanding of complex mixtures of surfactants and other components like polymers, enzymes and small particles. These advanced formulations are scientifically fascinating and offer exciting business opportunities that I hope to see at our conference. Bio-surfactants are already mentioned as an important area where there is a lot of activity both on the products themselves and on biochemical production routes.
What could be the next innovation leap and which new solutions can you imagine?
S. Asplund: I wish I knew the answer to that! This is partly what we hope to see when scientists and industrial players come together at the CESIO conference. From my perspective I can see many possibilities, but maybe the next leap will not be a new class of surfactants or even chemicals, but rather come in the way we develop and manufacture our products. I am thinking of the lightning-fast development we now see in fields like artificial intelligence and computing power. We are at the verge of a revolution, which is likely to transform every field of industry, including chemicals, and of course surfactants. Imagine being able to reliably predict the properties of molecules or even formulations directly based on molecule structure drawings!
Sustainability has become a buzz word in many industries. What are the most important aspects of sustainability in the surfactants industry?
S. Asplund: I think it is more than a buzz word, sustainability is critically important to the whole industry, definitely including surfactants. Until now the surfactant industry has mainly focused on the ecological aspect, as already discussed we use renewable raw materials, develop more biodegradable products etc. Sustainability has two other important pillars though, and it is becoming more and more clear that the challenges we are facing involve all three pillars; ecological, social and economic aspects.
If we look at raw material sourcing it is obvious to strive for renewable sources but this only works if the supply chain of the needed biomaterials come with sustainable social and economic conditions. A clear example is oils & fats; while surfactant production is a relatively small use compared to food or bio-fuels it is still critically important for our industry to establish a sustainable supply chain of natural oils like palm, coco and soya.
If we look at the product side the public debate, or “buzz” probably has most direct impact on value chains ending up in private consumption like home- and personal care although industrial users are also looking for sustainable solutions. A key here is communication along the value chain. Many consumers are increasingly looking at the origin of products, requiring transparency from suppliers and development of reliable and manageable certification standards for e.g. fair trade and eco-labels.
Will natural or renewable raw materials for "greener" surfactants play a larger role in the future? How can they create value for the surfactants industry?
S. Asplund: Natural raw materials are indeed already used and their importance will increase further. As just discussed though, “bio-based” is not sufficient to make a raw material source sustainable. Many consumers are looking for “greener” and the industry is trying to meet this demand while of course also providing the expected high performance and low cost. At the same time, scientists, regulators and industry stakeholders are trying to determine what is truly sustainable — clearly a challenging situation.
Having said that, new raw materials bring a lot of new opportunities and it is not just about oils and fats. The emerging bio-economy is providing building blocks with new functionality and a different pricing logic than traditional chemicals. We also see new synthesis opportunities and altogether this opens paths to novel surfactants with unique properties.
With regulations becoming tighter and raw material sourcing becoming more sophisticated, what are major challenges the surfactants industry is facing and how could these challenges be turned into opportunities?
S. Asplund: Surfactants are fascinating materials with their affinity to interfaces, tendency to form aggregates and interaction with other ingredients. This also means that they are challenging to handle and “standard testing” for regulatory purposes can even be misleading. An important aspect of our industry organization, CESIO, is to provide knowledge and ensure that regulations are developed based on facts, good science and correct testing.
As regulations and raw material chains develop, there will be both restrictions and new opportunities opening up. This not only affects surfactants, but we will see many changes in solvents, polymers and other ingredients. The surfactants industry has a tremendous expertise in bringing ingredients together in advanced formulations, and therefore, well positioned to help downstream users with these changes and at the same time develop new business opportunities.
most read

Specialty Chemicals in a Shifting World
Jennifer Abril, President & CEO of SOCMA, discusses the impact of new tariffs and the importance of regional supply networks in the specialty chemical industry.
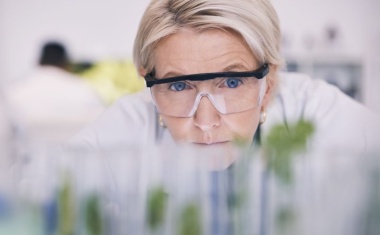
The Future of Demand for Chemicals
The chemical industry is shifting to sustainability-related products, with demand growing 4.5 times faster than conventional ones. Companies must revise their market strategies to capitalize on this opportunity.
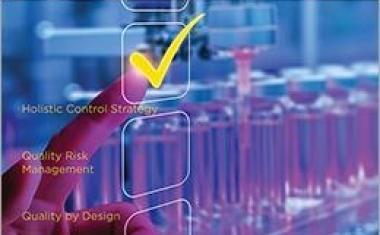
ISPE Good Practice Guide: Validation 4.0
The Validation 4.0 Guide provides a comprehensive approach to ensuring product quality and patient safety throughout a pharmaceutical product's lifecycle.
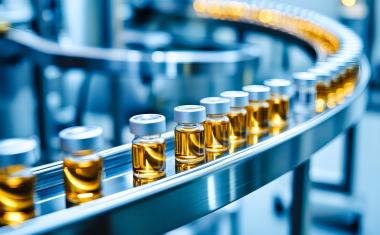
Pharma Outlook 2025
The environment for pharma in 2025 is diverse and challenging: New treatment options are being brought to market in ever shorter cycles.

“Access to Talent is a Crucial Factor”
In an interview with CHEManager, Edgardo Hernandez, President of Lilly Manufacturing, explains the strategy behind the ambitious investment project.