Transformation of Business Models and Processes in the Chemical Industry
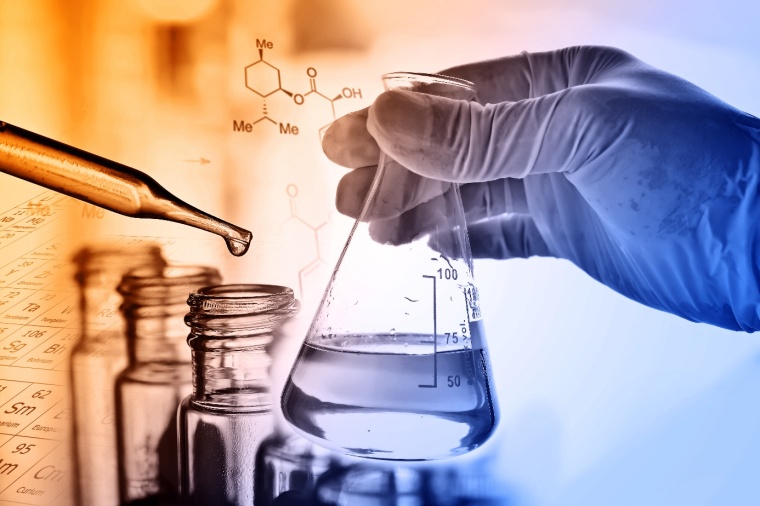
In a connected world where every chemical company is becoming a technology company, outcome-based business models; end-to-end process automation, integration, and collaboration with extended ecosystems; as well as strategic agility in response to market opportunities and needs will become the new paradigms for a sustainable future. Read more!