Evolution of Technology
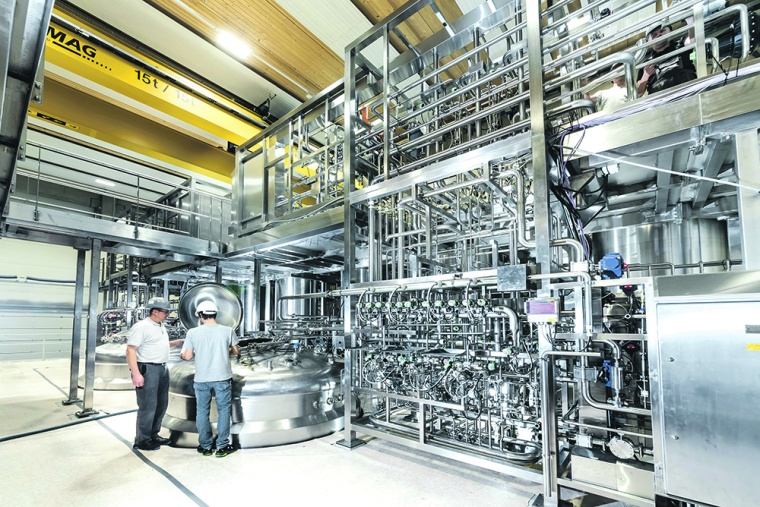
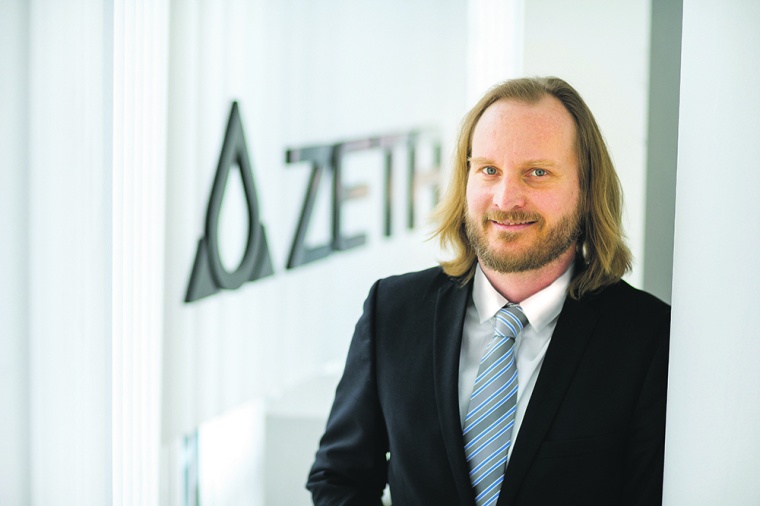
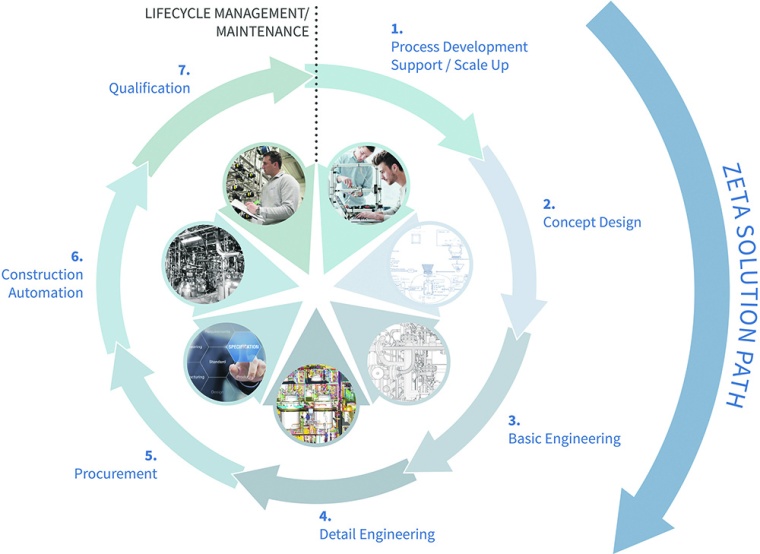
In terms of development of high-value pharmaceuticals pharma industry is pressed for time: there is a huge demand for new reliable and innovative solutions to guarantee maximum yield in shortest time. On the way to production at industrial scale, numerous planning steps are essential, by requiring deep process understanding and experience. Apart from that, the implementation from basic engineering to commissioning at the customer's site is going to be executed either at green field or by exact fitting into existing facilities.
Competent plant engineering has to include the development of new technologies, intelligent parallelization of process units, hub optimizing and last but not least a high level of flexibility thus allowing realization of projects in short time. Therefore, pharma industry needs a partner providing the best strategy for the customer by comprehensive engineering and services.
The development of pharmaceutical products and the optimal production processes are challenging the pharma industry. Projects need to be realized in shortest time. Despite of time pressure it has to be considered that occurring mistakes at an early stage may have a high impact later on. This causes significant extra costs and the up-scaling from lab to pilot scale turns out to be problematic as well. Plant engineers often face a dilemma in being requested to accept operational guarantees while not having the possibility to influence the planning process. This is why they are interested in contributing their expert knowledge as early as possible, in order to identify problems in a timely manner and to make processes more efficient. Because of that, Zeta decided to assign the individual elements of the range of services to the different development stages of a medicinal product. Concept design, basic and detail engineering are the most important pillars of the company’s “solution path” (see graphic).
The earliest point in time where the engineers dock on to the life cycle of a biopharmaceutical agent is when a customer has mastered its production process at lab scale (pre-clinical phase). Even at this early stage it is worth analyzing processes with a view to industrial-scale production and develop a concept for a pilot plant. Afterwards, all services along the “solution path” aim for support through the entire process of clinical studies, the parallel scale-up to industrial scale and the customized plant engineering in order to assist a professional product launch in shortest time.
Production of Monoclonal Antibodies
One of the fastest growing sectors in pharmaceutical industry is the production of monoclonal antibodies (mAB). The rapid growth of mAB demand requires efforts to increase production capacities as well as product titers. The production processes run in multiple stages – from low-volume seed cultures via intermediate cultures up to the production cultures in 25 m3 bioreactors.
The medication for the treatment of paroxysomal nocturnal hemoglubinuria (PNH) is also based on mAB. The drug is one of the most expensive therapies worldwide with annual therapy costs of some €400,000. For the development of an ultra-modern fermentation plant for the production of these mAB the services of the solution path were successfully applied.
The end-to-end management of the entire project – from basic to detail engineering and the handling of production, automation and qualification – resulted in increased efficiency as time-consuming interfaces could be saved. In order to manufacture and simulate the actual plant set-up, Zeta had to initially extend its premises and invested in a new manufacturing complex with 430 m2 providing all utilities for dynamic testing. The time-line for the project was very tight: 22 months only from basic engineering up to commissioning at the premises of the customer.
Industrial Scale-Up
The scale-up of the fermentation process from 50 l to 32,000 l was realized in close cooperation between the process and automation engineering teams working on the creation of functional specifications. The design complexity of the entire fermentation plant was reduced in detail engineering by development of an innovative master-copy concept. The high effort and costs of planning were kept to a minimum by mirroring the various bioreactor units. Due to the innovative concept the project term could be reduced by some 16 weeks.
Technical precision ensured by the modular super skid design simplified mechanical and electrical installation work. Furthermore, the skid design made a thorough functional test of each individual skid as a self-contained unit possible, thus significantly reducing the expenditure for the trip and installation at the customer's site. The entire plant (including wiring and piping) was planned and visualized as a modular system in the 3D model as early as the engineering phase, and interfaces between the individual skids were optimized. Due to confined space conditions at the customer’s site the automation specialists had to develop a control cabinet design to guarantee a smooth production process at a narrow space.
In addition, a fully integrated IT environment is important for end-to-end and thus time-saving processing of all process data. Data recording ensures full traceability – from mechanical engineering specification, to supply chain management of order placement in the ERP system, testing and documentation by the executive quality department, and commissioning of the individual components for the production process. In the course of qualification, the executive quality department also provided documentation in compliance with FDA and GMP requirements for the project to the fullest satisfaction of the customer.
Solution Path Benefits in Fast-track Projects
The planning of appropriate engineering steps according to quality by design (QbD) considers critical quality aspects (CQA) from the beginning and aims for increased process safety. In order to meet customer requirements completely, a precise coordination between the customer and all relevant experts is needed, who have to cooperate in a common team beyond the boundaries of the company.
The early initial analysis is particularly interesting for start-up companies that deal with the development of pharmaceutically active biomolecules. In joint workshops critical issues that need to be addressed are identified. This service represents a special value, since the project outcome is hard to predict at this stage.
The benefit of this approach is, that experts from different disciplines are working closely together without any external interface – except the one to the customer. This facilitates the complete engineering and development procedure as well as the realization of industrial production. The one-stop solution enables the pharma industry to meet the tight timeline of scale-up production and to execute projects on a fast-track in 22 months – even if it starts at green field.
most read
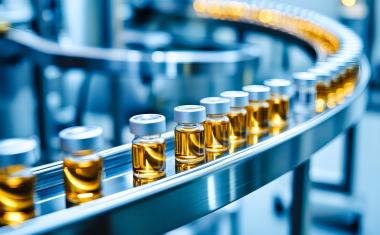
Pharma Outlook 2025
The environment for pharma in 2025 is diverse and challenging: New treatment options are being brought to market in ever shorter cycles.
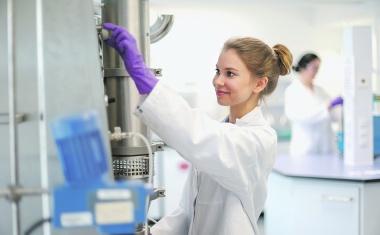
Fostering Innovation and Collaboration
Valerie Diele-Braun, CEO of IMCD, shares her vision for sustainability, global expansions, and strategic direction in an exclusive CHEManager International interview.

Specialty Chemicals in a Shifting World
Jennifer Abril, President & CEO of SOCMA, discusses the impact of new tariffs and the importance of regional supply networks in the specialty chemical industry.
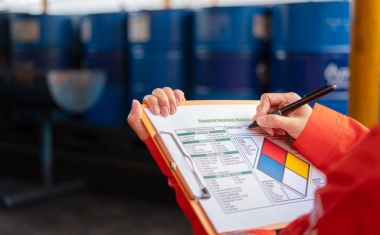
Substances of Concern
The EU Chemicals Strategy for Sustainability (CSS) highlights the shift to a hazard-centric approach in EU chemical regulation, emphasizing 'Substance of Concern' over risk-based measures.
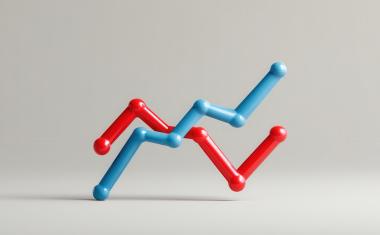
Q1 2025 Chemical Industry: Diverging Trends
The first quarter of 2025 highlights a continued divergence between the European and US chemical industries.