Promising Sales Profit Levers
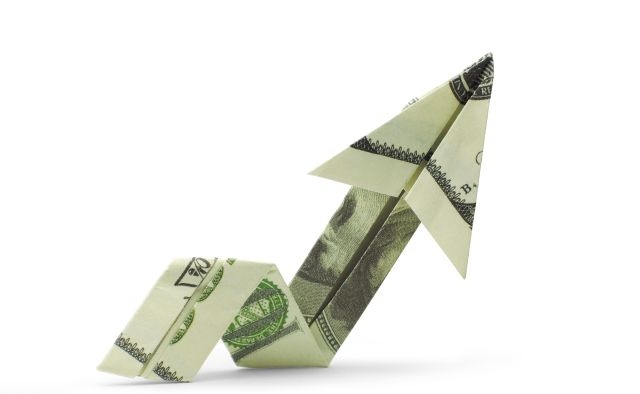
© BUTENKOV ALEKSEI/Shutterstock
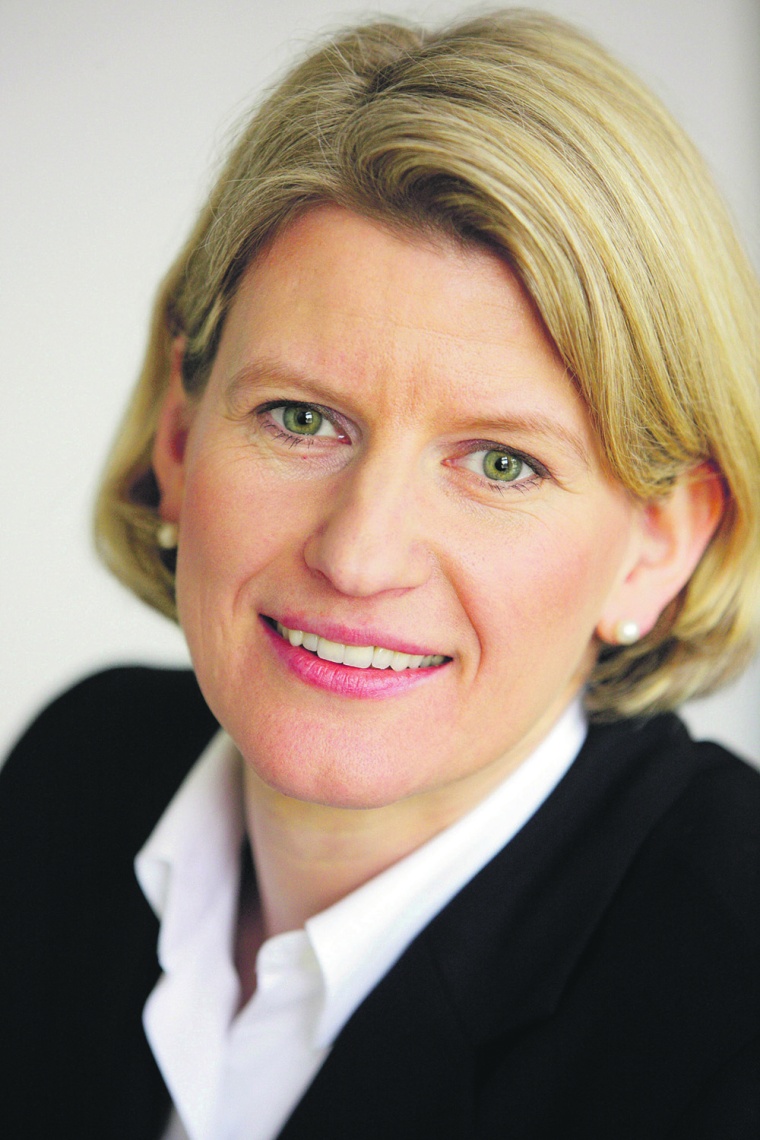
Andrea Maessen, Simon-Kucher & Partners
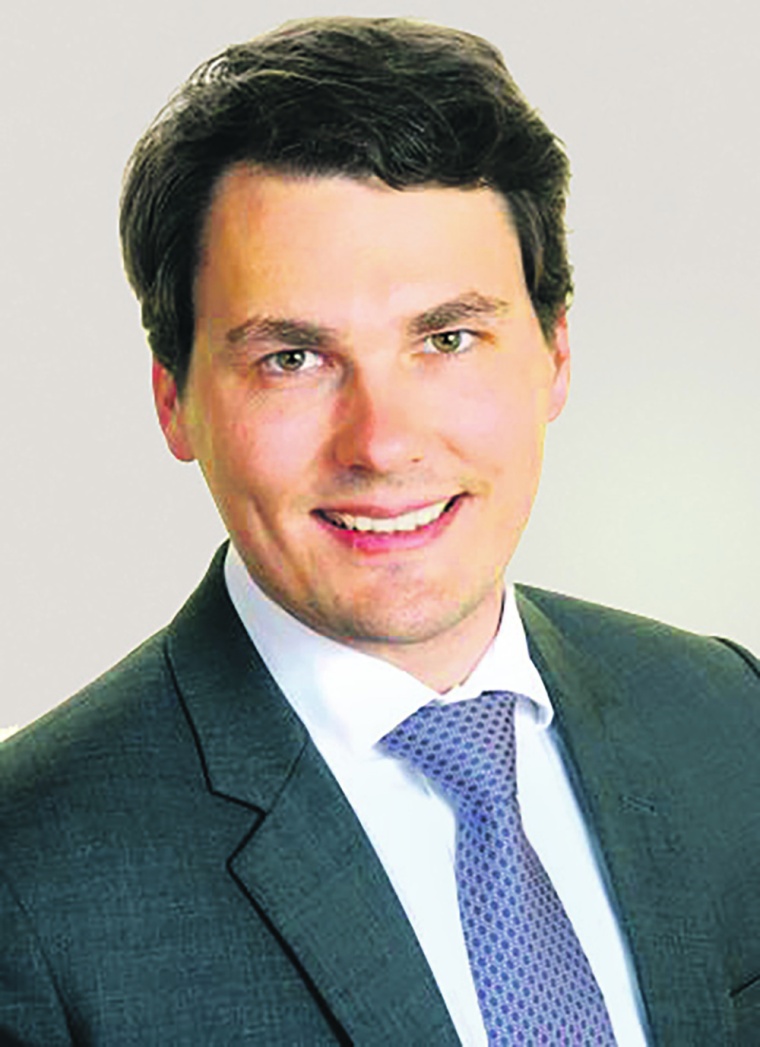
Jan Haemer, Simon-Kucher & Partners
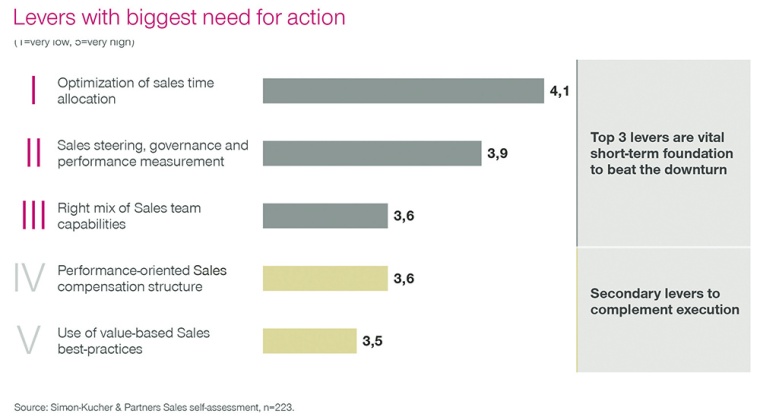
Fig. 1: Levers with biggest need for action in chemicals sales
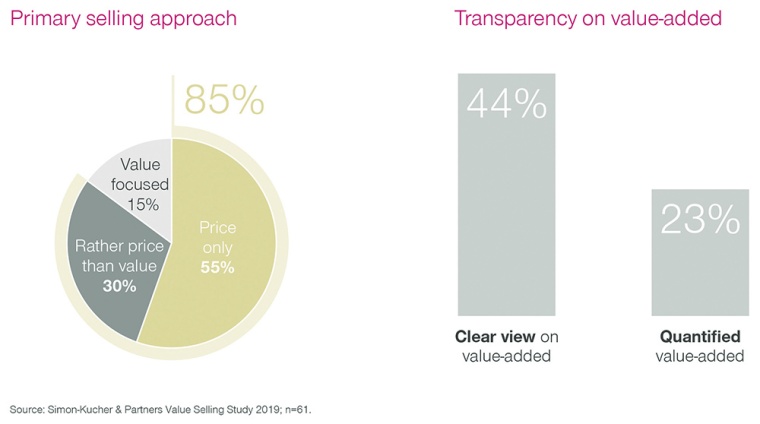
Fig. 2: Value selling in chemicals
At the end of the third quarter, the chemical industry continues to face an economic slowdown, compounded by international trade conflicts, increased political uncertainty, and fundamental changes to the value chain (e. g. the case of electro-mobility.) The higher the dependency on the automotive industry, the more German chemical producers are in a waiting mode on how the economy develops. Martin Brudermueller, CEO of BASF, described the current visibility on the business situation like “driving through a wall of fog”.
Profit warnings such as BASF’s have resonated beyond the industry. Such downturns usually lead to defensive strategies such as consolidation, cost-cutting, and strategic realignments. Unlike the financial crisis of 2009, the conditions for M&A activities remain favorable thanks to high liquidity and low interest rates. But the most promising profit levers — according to Simon-Kucher’s recent survey of private equity firms — are to be found on the revenue side rather than on the cost side.
Profit warnings such as BASF’s have resonated beyond the industry. Such downturns usually lead to defensive strategies such as consolidation, cost-cutting, and strategic realignments. Unlike the financial crisis of 2009, the conditions for M&A activities remain favorable thanks to high liquidity and low interest rates. But the most promising profit levers — according to Simon-Kucher’s recent survey of private equity firms — are to be found on the revenue side rather than on the cost side.
In other words, there is still untapped potential in sales, and a downturn offers chemical companies ample opportunities to improve their offense. Five strategies that can help to seize those opportunities on the revenue side are described below.
Increase Active Selling Time for Sales Reps and Technicians
Increase Active Selling Time for Sales Reps and Technicians
Chemical companies know from the production side of the business that short response times are key to success, to solve distress faster than competition, to protect the business, or win a deal. The same standards should apply to the commercial side. Yet, a recent Simon-Kucher study revealed that efficient use of selling time is seen as the most important improvement lever in sales.
Take the situation at a producer of specialty aromatics. Salespeople used to spend 50% of their day dealing with administrative tasks and internal meetings, which significantly delayed a quick reaction to customers. The answer to help the salespeople was a set of clear prioritization rules for customers based on margin and growth potential, combined with a standardized process flow to create more “room to operate” for the day-to-day business.
Meanwhile, the majority of technicians’ time was spent sampling and testing before the first commercial offer is submitted in the last third of the sales cycle. During this stage, the limited customer contact of technicians led to a considerable loss of efficiency. Increasing the customer-facing time from 10% to 30% and encouraging closer cooperation between sales reps and technicians helps to significantly shorten the sales cycle and grow revenues faster than planned.
Direct the Sales Activities more Pro-actively
Direct the Sales Activities more Pro-actively
Another of our studies showed that two thirds of chemical companies are not satisfied with how they direct the activities of their sales force. Four out of five say that they spend too much time explaining results and target deviations and too little time on forward looking sales activities. In addition, the data landscape remains a challenge due to limitations of the CRM set-up or usage, where sometimes even basic functionalities are not sufficiently covered for effective steering.
Early transparency on leading indicators such as the value and number of outstanding offers in the sales pipeline and expected win rates is vital for proactive direction and for taking corrective measures if needed.
Furthermore, companies need to have a clear view of what their most attractive market segments are and use activity benchmarks to drive higher sales efficiency. For example, a manufacturer of additives mobilized its sales force by providing simplified and mobile access to real-time data, such as incoming orders and steer its pipeline more effectively.
Strengthen Customer Focus and Value-selling
Strengthen Customer Focus and Value-selling
In a recent survey, we found that some 85% of chemical companies admitted that they feel their sales teams sell more on price rather than on value. An economic slowdown intensifies this price pressure even further. More than half of the companies surveyed said that their sales teams lack basic understanding of the added value of their own offerings relative to the competition. This makes their value messaging unclear and inconsistent, and creates an acute need for action.
One manufacturer of packaging solutions equipped its entire sales team with a value calculator, so that salespeople could systematically align sales talks with customer needs and elements of added value. The tablet-based tool helped calculate the potential cost savings per customer from applying the proposed product solution. By providing a structured basis for customer communication, the company boosted the confidence of the sales team in implementing customer-specific price increases with minimal volume losses.
Market and Monetize Innovations even faster
Market and Monetize Innovations even faster
Innovation is an important pillar of the chemical industry’s competitiveness. But when it comes to taking commercial aspects of innovations into account, the most appropriate description of how chemical companies usually behave is “too little, too late.” A popular excuse for not including the customer perspective early on is that the company lacks the resources. But without taking commercial considerations into account, the innovation pipeline usually gets so full that it can render the whole stage gate processes ineffective. This, in turn, is reflected in the results which miss their targets.
A fiber manufacturer recently introduced a project classification that helped to differentiate between a “quick & dirty”, a “pragmatic” or an “exhaustive” commercial approach to innovations. The classification was based on several criteria: the size and competitive intensity of the target market; the company’s own technological know-how; the budgets required; and the risk from product portfolio effects and cannibalization. Resources are then allocated per category. The “quick & dirty” approach relies on existing available information, expert judgement of cross-functional teams, and the use of internal benchmarks. The “pragmatic” approach supplements “quick & dirty” with customer workshops or exploratory interviews with prospects as well as an extensive quantification of value. This helps to shorten the time to market, especially for a number of smaller customer projects. For the ground-breaking innovations, additional resources support the development of full-scale launch strategies.
Upgrade the Sales Model with Digital Marketplaces
Upgrade the Sales Model with Digital Marketplaces
Digital marketplaces are rapidly gaining importance in the chemical industry. Beyond industry-vertical players like Chemondis and Chembid, ecosystem market players like Alibaba and Amazon Business are taking aim at chemicals. The benefits of digital marketplaces for your sales model are twofold: they help to optimize cost-to-serve and to accelerate growth.
Let’s start with cost-to-serve: Assume that selling, general and administrative (SG&A) costs are below 4% of sales in upstream chemicals and 5-7% further downstream. Commissions range from below 0.5% to about 5% of sales on online platforms like Alibaba, depending on the service level. The potential cost-savings are huge.
Digital marketplaces can also help accelerate growth, because they cater to mid-sized and small customers much more efficiently and thus free up resources. Beyond this, platforms also enlarge the accessible profit pool by serving distributors’ customers directly.
There is plenty of opportunity from forward defensive strategies in sales. If the chemical industry were as precise in optimizing sales processes as it is in production, safely navigating through this economic slowdown won’t be an issue.
Details of the studies mentioned in this article can be requested from the authors.