Sustainability in Production is Key - What Does Flow Chemistry Bring to the Table?
Numerous articles have been published within the last years in chemical science and business media (including this one) on the advantages of continuous reactions, aka flow chemistry.
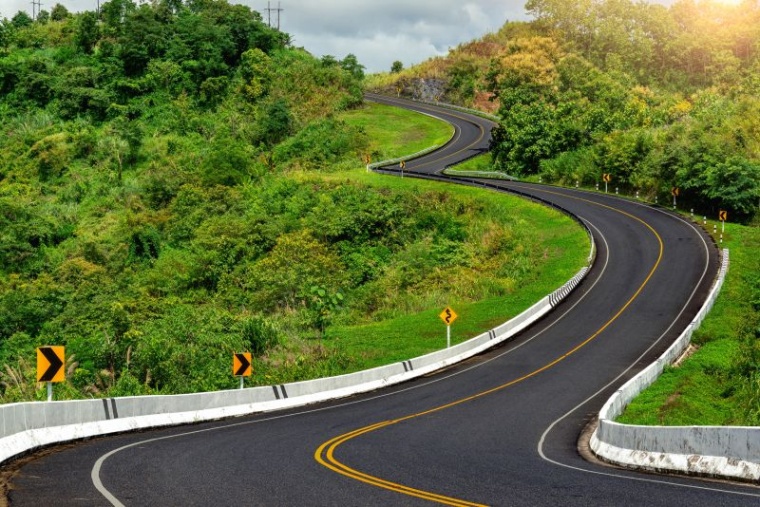
Numerous articles have been published within the last years in chemical science and business media (including this one) on the advantages of continuous reactions, aka flow chemistry. While the innovative technology has long since outgrown its infancy, it is still struggling to find widespread use outside of laboratories and technical centers. Now, with sustainability being named everywhere as the new guiding light for the industry, a paradigm shift from batch to flow reactions is likely to happen. Or isn’t it?
Over the course of at least a decade, flow chemistry has been praised in many headlines as a promising standard technology for production in the chemical and pharmaceutical industries and as a driver of sustainability. “Flow Chemistry Opens up New Possibilities“, “A Technology on the Upswing“, “Unique Opportunity for Innovation and Improvement”, “Key Technology for Sustainable Processes”, “A Mature Technology still on the Rise” – just to mention a few of them. Undoubtedly, flow chemistry, also known as microreaction or millireaction technology, does have several advantages for chemical and pharmaceutical production, and all of them have a sustainability component, be it safety, resource and energy efficiency, product quality, selectivity or flexibility.
Pros and Cons
The advantages of flow chemistry are fast and good mixing and excellent heat transfer, enabling higher selectivity and yields while lowering raw material requirements. Besides, the number of by-products and the energy demand for their separation (downstream processing) is reduced – about 70% of energy costs correspond to the separation of by-products. Regarding safety, fast, explosive, and highly exothermic reactions involving toxic substances can be run in much smaller reactor volumes than batch reactors.
"Continuous flow technology can improve the robustness, sustainability and safety of many chemical processes. It is an enabling technology that allows the safe generation and use of hazardous intermediates, as well as operation under high temperatures and pressures," explains David Cantillo, flow chemistry expert and area leader at the Research Center Pharmaceutical Engineering (RCPE) at the University of Graz, Austria.
Thus, the contribution of flow chemistry for designing chemical processes with a lower environmental footprint compared to batch production stimulates justified hope for society’s need of a greener, more sustainable and safer chemical industry. Various aspects of flow chemistry also support the design of novel strategies for the transformation from an exclusively fossil-based to a biobased industry, or at least to a more sustainable chemical industry, with applications ranging from commodity to specialty chemicals to fine chemicals, including agrochemical and pharmaceutical intermediates and active ingredients.
However, on the flip side, there are challenges and limitations that hamper a broader application of flow reactors in industry that may explain why flow chemistry is still not as common in chemical and pharmaceutical production as it should be, given its benefits.
During a recent roundtable discussion on the topic of sustainability in chemical and pharmaceutical production organized by CHEManager, participants from several manufacturers as well as service and technology providers shared their views on flow chemistry. One key finding from this discussion may not come as a surprise: Safety, and not sustainability considerations are still the most important, if not — as for many manufacturers — the only criteria when deciding to run a reaction in a flow reactor.
Microreaction technology can improve the safety profile of a reaction, as hazardous and reactive reagents can be handled more safely and highly exothermic chemistry can be better controlled in a microreactor (or millireactor, depending on the tube diameter) due to smaller volumes and to higher heat and mass transfer.
Peter Markus, Senior Director Marketing & Sales / Key Account Management at Midas Pharma and a chemist with 30-years industry experience, explains: “The motivation was always safety. Flow processes have been used for hazard-driven chemistry, because the reaction mixture could be reduced to small volumes at the moment of flow, hence less risk of damage in case of an event.”
Annegret Vester, Chief Sustainability Officer of German chemical company CHT, and a chemist whose vision is a sustainable future for the chemical industry, regards safety as one significant aspect of sustainability. “We have established microreaction technology in Germany for many years for the production of H-siloxanes, i.e. organosiloxanes with Si-bonded hydrogen atoms, and it works excellently. For siloxanes, the introduction of microreaction technology had a clear focus on occupational safety. We thought that we could do a lot more with flow chemistry, but we had to recognize that our large and diverse portfolio of products and technologies is more suitable for batch processes because for flow processes you need a certain throughput. If you have a large-volume product, flow chemistry is unbeatable, it’s actually more sustainable than batch production. With 5,000 products in our portfolio, you can imagine that they do not all run on a large scale, but there are a lot of product changes every day.”
Sustainability in general is not necessarily seen as top priority for choosing a chemical manufacturing process, but any improvement of occupational safety or process efficiency automatically enhances the sustainability performance of a process.
Indeed, most large-volume processes use continuous reactions due to the efficiency benefits. At a smaller scale — maybe even at a scale of about 10,000 t/a — batch reactors dominate as establishing a continuous process is expensive and requires a substantial upfront investment that can only be justified when the production scale is large.
Vester’s statement is congruent with others. For instance, Daniel Wagner, Head of CMC Synthetics Early Development Germany at Sanofi, said: “When it comes to flow chemistry, sustainability is not the only important aspect for us, key is also the advantage to accelerate the scale-up from smaller to larger batch sizes.”
And Ulrich Mayerhoeffer, Head Technical Evaluation and Development at Swiss Contract Development and Manufacturing Organization (CDMO) Arxada, told CHEManager in a previous survey: “We are strong believers in the benefits of flow chemistry.” But he admits that technology selection is mainly driven by process safety, quality, sustainability, and overall economic considerations, with safety as the strongest driver towards a flow process. Although advantages in terms of process parameter control are often also beneficial product quality-wise and the strengths of flow chemistry are clearly demonstrated in reactions where the control of side product formation or the preservation of stereo-information are vital. The CDMO space in pharmaceuticals and fine chemicals is still dominated by batch and semi-batch processes performed in multipurpose plants.
But why are benefits like product quality, control of side product formation or preservation of stereo-information not enough reason to switch from batch to flow? Especially in the pharma or agrochemical sector, where many products require multistep syntheses, that could be performed in sequence or in parallel by connecting different flow reactors?
Hurdles to Overcome
The reasons for the hesitancy of many manufacturers to adopt microreaction technology can be manifold, including, as mentioned above, the high initial investment for the flow equipment and infrastructure, but also the lack of standardization and compatibility among different flow systems and components, or the lack of expertise and training among chemists and engineers. This applies in particular to new processes for which there is no comparison with batch processes, and, in addition, it usually takes several years for new technologies to find their way into standard educational literature.
Another aspect that is particularly significant in the pharmaceutical sector is the high level of regulation. The development and approval of a synthesis process for pharmaceutical chemicals by the regulatory authorities is a lengthy and costly process. Many companies are therefore reluctant to replace an established and audited process with a new one.
According to Kai Rossen, Chief Scientific Officer at EuroAPI, the former CDMO business of Sanofi, the regulatory context with its strong impact on the quality of the products as well as the responsible control of waste streams is important. Rossen said: “The last 20 years have shown a re-discovery of flow chemistry. The application of flow chemistry enables reactions that could not be performed in a simple batch process and are thus a critical tool in finding the optimum for the synthesis of a compound, such as an API.”
In addition, batch processes in dedicated or in multipurpose reactors have been optimized in many areas to such an extent that they no longer have any significant disadvantages in terms of efficiency and sustainability compared to flow processes. Ulrich Scholz, Head of Chemical Development at Boehringer Ingelheim Pharma, described one such experience: “We tried to show that flow chemistry is superior. We had several examples, but in the end realized that although the flow process works well, the batch process is not much worse or even got better with a catalytic upgrade.”
But the adoption of continuous flow technologies for pharmaceutical applications is now strongly advocated by regulatory authorities such as the US Food and Drug Administration (FDA) and the European Medicines Agency (EMA). This may lead to faster regulatory approval which could lead to quicker adoption of flow processes for the manufacture of pharmaceutical chemicals.
One reason for the hesitancy to implement flow technology may simply be the resistance to change. Thomas Riermeier, Senior Vice President & General Manager, Health Care at Evonik, said: “We invested in flow chemistry years ago and built a modular pilot plant. As a CDMO company, Evonik had evaluated the technology for customer projects, and we’ve seen an increasing customer interest in more sustainable solutions. But as of now, a real breakthrough is yet to occur.” According to Riermeier, the decisive factor was that customers preferred the established process at that time.
For Riermeier, it is not a black and white decision, but the crucial success factor is: “How can we expand our chemistry toolbox making processes as efficient as possible? I believe, we have to face it with an open-minded setup towards technologies — if continuous flow, or classic batch — and by doing so favor those with the most positive sustainable impact.”
A risk-averse mindset may predominate particularly among seasoned chemists who have not been educated or trained in this technology. Although flow chemistry is not a novel technique and many of the top commodity chemicals by volume are produced in continuous plants, fine chemicals and pharmaceuticals production are still almost exclusively dominated by batch manufacturing.
So, as the lack of know-how in the field and the late adoption of the technology are perceived as major hurdles, general education and proper training in flow chemistry in the early chemistry curricula would contribute to a more widespread technology transfer and faster adoption. An indicator of the technology’s maturity status is recent job offers from the pharmaceutical industry, where skills in flow chemistry are often required. However, these challenges and limitations are being addressed by ongoing research and development
Silver Linings
Flow chemistry can be considered a green technology because flow reactions can be performed in a sustainable way, with advantages for safety, efficiency, waste reduction, the avoidance of hazardous chemicals, continuous product formation, and easy recovery and reuse of the catalyst. It, therefore, could be a powerful ally in achieving the 12 Principles of Green Chemistry.
Significant efforts have been made globally to develop the manufacturing flexibility and robustness of processes used to produce chemicals in a continuous way. Andreas Foerster, managing director of Dechema — the German Society for Chemical Engineering and Biotechnology — explains: “Since the early research in microreaction engineering the field has evolved and diversified. Millimeter instead of micrometer structures are more often used in continuous production equipment today. Such channels sufficiently provide the advantages of microreactors while being more robust for example in the handling of solids, which remains challenging in microstructures.” Förster adds: “In this sense, microreactors are used in production processes in the form of modular continuous production units or flow chemistry set-ups containing such structured devices.”
Yet, despite these developments, a major challenge for the fine chemical and pharmaceutical industry is the established application of flow technology to commercially relevant examples. The identification of opportunities to apply micro or millireactors to current processes is critical to the success of this technology for pharmaceutical and fine chemical companies.
There are, however, examples that may indicate that flow chemistry is really a technology on the upswing and may proceed faster than expected. For instance, in the spring of 2023, Italian CDMO Flamma Group announced to invest $200 million over the next three years to expand its capabilities and add innovative technologies which will include expanding its existing flow chemistry capabilities in Italy. And in summer of 2023, Axplora, a pharmaceutical CDMO established previously by the merger of German CDMO PharmaZell and French CDMO Novasep, said that it has completed the installation of a new cGMP flow chemistry pilot unit at its German site in Leverkusen, costing more than €1 million. Axplora, a partner of pharmaceutical and biotech companies for the production of complex active pharmaceutical ingredients (APIs), sees special technologies like flow chemistry as a differentiating factor. Ester Masllorens, Chief Technology Officer of Axplora, explains: “Continuous processing is a key enabling technology for the future of pharmaceutical manufacturing, strongly supported by regulatory bodies such as the FDA. This technology has high potential to enhance sustainability, improve control and quality as well as reduce costs and time to market.”
Conclusion
The decision for or against it falls within a narrow range of criteria and parameters that have to be fulfilled in order to make technical and economic sense for manufacturers of chemicals and pharmaceuticals. Flow chemistry is not a one-size-fits-all technology, but it is an innovative, yet matured technology that offers numerous advantages and benefits to transform chemical production in a sustainable way. Hence, flow chemistry in pharmaceuticals and fine chemicals manufacturing is gaining momentum, however, it will not prevail rapidly but rather in a step-by-step kind of marathon walk with twists and turns along its way. As a new generation of chemists and managers is eager to embrace green and sustainable chemistry — especially in new processes — the long-term prospects are clear: Flow chemistry is here to stay.
Michael Reubold, CHEManager