Digitalisierung in der Prozessindustrie
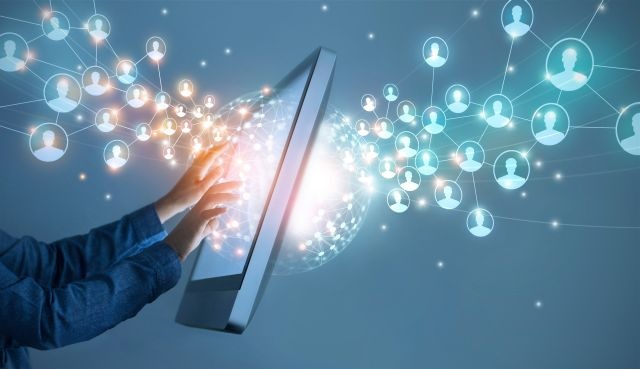
© Getty Images/iStock
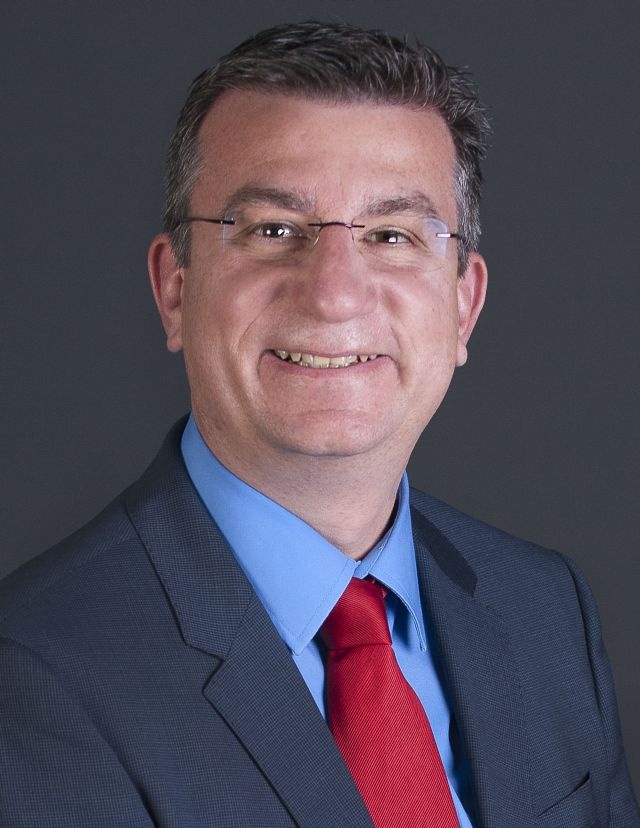
Carsten Gerke, Senior Vice President Strategic Partnerships, Bentley Systems: “Mit unseren auf die Prozessindustrie zugeschnittenen Lösungen bringen wir mehr Effizienz in den Digitalen Zwilling für den Anlagenbau.”
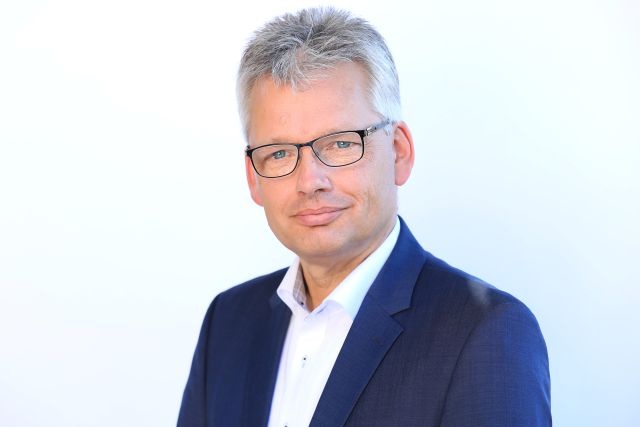
Bernd Kokkelink, Head of Comos Industry Solutions, Siemens: “Hand-over-Phasen zwischen Capex und Opex müssen geschlossen werden, um Daten-Inkonsistenzen zu vermeiden.“
Die Hürden auf dem Weg zur Digitalisierung sind hoch, wenn sich wirkliche Erfolge einstellen sollen. Mit der Zusammenarbeit von Siemens und Bentley Systems sollen Anwender der Prozessindustrie schneller und wettbewerbsfähiger auf den Weg in die digitale Transformation gebracht werden. CHEManager befragte dazu Bernd Kokkelink, Head of Comos Industry Solutions, Siemens, und Carsten Gerke, Senior Vice President Strategic Partnerships, Bentley Systems. Die Fragen stellte Volker Oestreich.
CHEManager: Herr Gerke, Herr Kokkelink, die Digitalisierung in der Prozessindustrie voranbringen, Veränderung ermöglichen und Mehrwert schaffen: Diese Ziele haben sich Siemens und Bentley Systems für ihre Zusammenarbeit gesetzt. Wie sieht diese Zusammenarbeit aus, was bringen beide Firmen ein und wie ist der aktuelle Stand der Dinge?
Bernd Kokkelink: Nach wie vor ist das Thema Durchgängigkeit ein zentraler Punkt. Damit jede Anlage so profitabel wie möglich ist, müssen Hand-over-Phasen zwischen Capex und Opex geschlossen werden, um Daten-Inkonsistenzen zu vermeiden. Genau das war der Ausgangspunkt für die strategische Allianz zwischen Siemens und Bentley, die auf einem sehr komplementären Software-Portfolio basiert, mit dem Ziel, die Möglichkeiten für eine bessere Datennutzung zu erweitern und digitale Zwillinge effizienter zu machen.
CHEManager: Herr Gerke, Herr Kokkelink, die Digitalisierung in der Prozessindustrie voranbringen, Veränderung ermöglichen und Mehrwert schaffen: Diese Ziele haben sich Siemens und Bentley Systems für ihre Zusammenarbeit gesetzt. Wie sieht diese Zusammenarbeit aus, was bringen beide Firmen ein und wie ist der aktuelle Stand der Dinge?
Bernd Kokkelink: Nach wie vor ist das Thema Durchgängigkeit ein zentraler Punkt. Damit jede Anlage so profitabel wie möglich ist, müssen Hand-over-Phasen zwischen Capex und Opex geschlossen werden, um Daten-Inkonsistenzen zu vermeiden. Genau das war der Ausgangspunkt für die strategische Allianz zwischen Siemens und Bentley, die auf einem sehr komplementären Software-Portfolio basiert, mit dem Ziel, die Möglichkeiten für eine bessere Datennutzung zu erweitern und digitale Zwillinge effizienter zu machen.
Carsten Gerke: Die Zusammenarbeit von Bentley Systems und Siemens umfasst nicht nur die Prozess- und Fertigungsindustrie, sondern auch die Bereiche Energie, Gebäudetechnik, Mobilität und die Digitale Stadt, in denen wir Synergien nutzen und mit gemeinsam entwickelten Lösungen für den Digitalen Zwilling Mehrwert für Industrie und Infrastrukturprojekte weltweit schaffen.
Siemens bringt hierbei die physikalische Welt der Automatisierung und IoT samt Software-Lösungen ein. Bentley System ergänzt mit seinem Software-Portfolio die virtuelle Welt insbesondere im 3D-Bereich und Informationsmanagement.
Unsere komplementären Technologien und unsere Expertise machen nicht nur unsere beiden Unternehmen, sondern auch unsere Kunden weltweit schneller und wettbewerbsfähiger auf dem Weg in die digitale Transformation. Unser „Digital Co-Venture“ und die daraus resultierenden gemeinsamen Produktentwicklungen erschließen unseren Kunden das wahre Potenzial der Digitalisierung. Mit unseren eigens auf die Prozessindustrie zugeschnittenen Lösungen bringen wir gemeinsam mehr Effizienz in den Digitalen Zwilling für den Anlagenbau.
Der Begriff „Digitaler Zwilling“ ist schnell gesagt und klingt plausibel. Wenn man von der “Industrie 4.0-Verwaltungsschale” spricht, klingt das Ganze schon herausfordernder – und doch gehört beides zusammen. Wie helfen Sie Ihren Kunden, den technischen Aufwand bei der Digitalisierung und der Erstellung digitaler Zwillinge in überschaubaren Grenzen zu halten?
B. Kokkelink: Den Begriff „Digitaler Zwilling“ haben wir in den letzten Jahren erfolgreich im Markt geprägt. Mittlerweile hat er längst Einzug in die Industrie gehalten und revolutioniert dort die Abläufe entlang der gesamten Wertschöpfungskette. Als virtuelles Abbild der realen Anlage ermöglicht er eine nahtlose Verknüpfung der einzelnen Prozessschritte.
Der Begriff „Digitaler Zwilling“ ist schnell gesagt und klingt plausibel. Wenn man von der “Industrie 4.0-Verwaltungsschale” spricht, klingt das Ganze schon herausfordernder – und doch gehört beides zusammen. Wie helfen Sie Ihren Kunden, den technischen Aufwand bei der Digitalisierung und der Erstellung digitaler Zwillinge in überschaubaren Grenzen zu halten?
B. Kokkelink: Den Begriff „Digitaler Zwilling“ haben wir in den letzten Jahren erfolgreich im Markt geprägt. Mittlerweile hat er längst Einzug in die Industrie gehalten und revolutioniert dort die Abläufe entlang der gesamten Wertschöpfungskette. Als virtuelles Abbild der realen Anlage ermöglicht er eine nahtlose Verknüpfung der einzelnen Prozessschritte.
Der Schlüssel zum Digitalen Zwilling liegt für uns in der Entwicklung eines durchgängigen Datenmodells vom Anlagenengineering bis hin zum Betrieb. Doch gerade hier besteht für Betreiber von Bestandsanlagen die größte Herausforderung. Jede Industrieanlage ist durch eine kumulative Datenentwicklung gekennzeichnet. In allen Phasen des Asset-Lebenszyklus werden enorme Mengen an Daten und Informationen generiert. Diese sind über eine Vielzahl von Softwareanwendungen, Datenbanken und Papierdateien im gesamten Unternehmen und vor Ort verteilt. Folglich sind die Informationen, die den Entscheidungsträgern zur Verfügung stehen, oft ungenau, veraltet, unvollständig, inkonsistent und / oder schlecht synchronisiert. Die fehlende Datenintegration schafft Herausforderungen und Ineffizienzen, die zu massiven Fehlentscheidungen führen kann.
„Unser Ansatz ist ein wichtiger Schritt auf dem Weg zur Digitalisierung der Prozessindustrien, ohne die bestehende physische oder virtuelle Umgebung zu stören.“
Bernd Kokkelink
C. Gerke: Wirklich kompliziert sind nur die Back-End-Prozesse bei der Digitalisierung und diese nehmen wir unseren Kunden ab. Für den Anwender selbst wird die Erstellung des Digitalen Zwillings durch die einfach zugängliche Cloud-Umgebung zum Kinderspiel.
Wir bringen alle vorhandenen Daten aus dem Planungsprozess auf einer Plattform als Cloud-Service zur Aggregation für später gelagerte Prozesse zusammen. Diese Daten der Engineeringtechnologie (ET) können dann intelligent mit Daten aus dem Betrieb (OT) oder der Informationstechnologie (IT) verknüpft werden. Die Daten aus der Planungs- und Bauphase stellen sozusagen die digitale DNA von jeglicher Infrastruktur dar. Heute sind diese meist vergraben in unterschiedlichen Datensilos, zum Beispiel in Schemata, 3D-Modellen oder Listen. Durch das Zusammenführen kommt der richtige Einblick in die Anlage und ein intuitiver Zugang zu allen entscheidungsrelevanten Daten wird möglich.
Von den Daten als dem Gold des 21. Jahrhunderts ist immer wieder die Rede, aber Daten ändern sich und es gibt sie im Überfluss. Wie helfen Siemens und Bentley Systems ihren Kunden in der Prozessindustrie, Daten wirtschaftlich zu nutzen?
C. Gerke: Wie bereits von Herrn Kokkelink angedeutet, wissen wir alle, dass nicht die Menge der verfügbaren Daten das Problem ist. Die Herausforderung ist, dass die Datenfluten in unterschiedlichsten Formaten zu fundierten, transparenten Informationen zusammenfließen, auf deren Grundlage bessere Entscheidungen für mehr Wachstum getroffen werden können. Eigentümer und Betreiber von Anlagen haben erkannt, dass ein Digitaler Zwilling nur verlässlich und leistungsstark ist, wenn die Synchronisation mit sich ändernden aktuellen Bedingungen in der realen Welt gegeben ist. Die einmalige Erfassung und Darstellung der realen Welt einschließlich der IoT-Inputs reicht nicht aus, um die digitale DNA der Infrastrukturanlage zu verstehen, die in den technischen Spezifikationen der Anlagen enthalten sind und Verbesserungen zu analysieren, zu modellieren, zu simulieren. Und genau hierin liegen die gemeinsamen Stärken von Bentley Systems und Siemens, die wir im sogenannten „Performance Digital Twin“ wirtschaftlich nutzbar machen.
Von den Daten als dem Gold des 21. Jahrhunderts ist immer wieder die Rede, aber Daten ändern sich und es gibt sie im Überfluss. Wie helfen Siemens und Bentley Systems ihren Kunden in der Prozessindustrie, Daten wirtschaftlich zu nutzen?
C. Gerke: Wie bereits von Herrn Kokkelink angedeutet, wissen wir alle, dass nicht die Menge der verfügbaren Daten das Problem ist. Die Herausforderung ist, dass die Datenfluten in unterschiedlichsten Formaten zu fundierten, transparenten Informationen zusammenfließen, auf deren Grundlage bessere Entscheidungen für mehr Wachstum getroffen werden können. Eigentümer und Betreiber von Anlagen haben erkannt, dass ein Digitaler Zwilling nur verlässlich und leistungsstark ist, wenn die Synchronisation mit sich ändernden aktuellen Bedingungen in der realen Welt gegeben ist. Die einmalige Erfassung und Darstellung der realen Welt einschließlich der IoT-Inputs reicht nicht aus, um die digitale DNA der Infrastrukturanlage zu verstehen, die in den technischen Spezifikationen der Anlagen enthalten sind und Verbesserungen zu analysieren, zu modellieren, zu simulieren. Und genau hierin liegen die gemeinsamen Stärken von Bentley Systems und Siemens, die wir im sogenannten „Performance Digital Twin“ wirtschaftlich nutzbar machen.
B. Kokkelink: Unser Ansatz ist ein wichtiger Schritt auf dem Weg zur Digitalisierung der Prozessindustrien und der der Digitalisierung des Anlagenbaus im Speziellen, ohne die bestehende physische oder virtuelle Umgebung zu stören.
Die Anforderungen an Daten und Systeme sind im Lebenszyklus einer Anlage unterschiedlich. Im Entstehungsprozess einer Anlage von der Planung bis zum FAT und dann zum Betrieb sind verschiedene Partner involviert, die unterschiedliche Blicke auf die Anlage haben. Wie können Sie sicherstellen, dass Daten konsolidiert werden, den Ansprüchen aller Stakeholder genügen, möglichst nur einmal erfasst, aber dann zuverlässig gepflegt werden?
B. Kokkelink: Wie gesagt, liegt der Schlüssel unseres Erachtens in einer Cloud-basierten Lösung mit offener Architektur, die eine Reihe von Mikrodienstleistungen bereitstellt, darunter Prozess- und Anlagentechnik, physische Layout-Modellierung, Projekt- und Konstruktionsplanung, Wartung und Asset-Performance-Modellierung. Wichtig ist hierbei die Unterstützung durch das Zusammenfassen von Daten von zugrunde liegenden Services sowie verwandten Anwendungen, um Datendopplungen innerhalb der Lösungsarchitektur zu vermeiden. Durch intelligentes scannen und interpretieren bekommen alle Projektbeteiligten den Zugriff auf traditionell unzugängliche Daten. Services zur Validierung und Verknüpfung von Daten mit anderen Informationen, kombiniert mit Änderungsverfolgung, verbessern die Genauigkeit, Vollständigkeit und Vertrauenswürdigkeit von Asset-Daten und -Dokumentation.
B. Kokkelink: Wie gesagt, liegt der Schlüssel unseres Erachtens in einer Cloud-basierten Lösung mit offener Architektur, die eine Reihe von Mikrodienstleistungen bereitstellt, darunter Prozess- und Anlagentechnik, physische Layout-Modellierung, Projekt- und Konstruktionsplanung, Wartung und Asset-Performance-Modellierung. Wichtig ist hierbei die Unterstützung durch das Zusammenfassen von Daten von zugrunde liegenden Services sowie verwandten Anwendungen, um Datendopplungen innerhalb der Lösungsarchitektur zu vermeiden. Durch intelligentes scannen und interpretieren bekommen alle Projektbeteiligten den Zugriff auf traditionell unzugängliche Daten. Services zur Validierung und Verknüpfung von Daten mit anderen Informationen, kombiniert mit Änderungsverfolgung, verbessern die Genauigkeit, Vollständigkeit und Vertrauenswürdigkeit von Asset-Daten und -Dokumentation.
„Die Herausforderung ist, dass die Datenfluten in unterschiedlichsten Formaten
zu fundierten, transparenten Informationen zusammenfließen.“
Carsten Gerke
C. Gerke: Es braucht eine gute Gesamtstrategie für die Anlage aus jeder Perspektive, zu jeder Zeit und überall. Dazu bedarf es einer offenen Plattform mit einheitlichem Schema. Unabhängig davon, ob Betriebsleiter, Anlagenplaner oder -betreiber, alle profitieren gleichermaßen von zuverlässigen, kontinuierlich aktualisierten Daten und kontextualisierten, visualisierten Asset-Informationen, die ihnen in einer zielgruppenorientierten Benutzerschnittstelle zur Verfügung stehen.
Wie ist der aktuelle Entwicklungsstand von PlantSight, wie wurden bei der Entwicklung spätere Anwender mit einbezogen und wie ist aktuell die Akzeptanz dieses „Systems der Systeme“? Bei welchen Leitkunden gibt es Erprobungen und mit welchem Erfolg?
C. Gerke: In PlantSight vereinigen sich reale und virtuelle Welt zu einer alles übergreifenden Digital Twin Plattform, die bereits jetzt auf dem Markt verfügbar ist. Wie bei Cloud-basierten Lösungen üblich, werden funktionale Erweiterungen kontinuierlich zur Verfügung gestellt. Das Zusammenführen unterschiedlichster Datensätze auf der Plattform wurde mit bestehenden Siemens und Bentley Kunden beziehungsweise mit deren Daten ausführlich getestet.
Wie ist der aktuelle Entwicklungsstand von PlantSight, wie wurden bei der Entwicklung spätere Anwender mit einbezogen und wie ist aktuell die Akzeptanz dieses „Systems der Systeme“? Bei welchen Leitkunden gibt es Erprobungen und mit welchem Erfolg?
C. Gerke: In PlantSight vereinigen sich reale und virtuelle Welt zu einer alles übergreifenden Digital Twin Plattform, die bereits jetzt auf dem Markt verfügbar ist. Wie bei Cloud-basierten Lösungen üblich, werden funktionale Erweiterungen kontinuierlich zur Verfügung gestellt. Das Zusammenführen unterschiedlichster Datensätze auf der Plattform wurde mit bestehenden Siemens und Bentley Kunden beziehungsweise mit deren Daten ausführlich getestet.
B. Kokkelink: Nach der ersten offiziellen Vorstellung von PlantSight auf der Hannover Messe konnten weitere Siemens-interne Kunden sowie führende Prozessindustrieunternehmen als Piloten gewonnen werden, die auch für die bereits geplanten nächsten Entwicklungsschritte wichtige Feedbackgeber waren. So freuen wir uns, dass wir auf der im Oktober stattfindenden Bentley Year & Infrastructure Conference in Singapur neue Use-Cases mit dem Ziel präsentieren zu können, die digitale Zuverlässigkeit weiter zu erhöhen. Hier kommen auch erste Anwender zu Wort, die von ihren Erfahrungen mit PlantSight berichten.
Mit immer mehr verfügbaren Daten, besseren Algorithmen und immer höheren Rechenleistungen sind die Wettervorhersagen in den letzten Jahren immer besser geworden. Lassen sich durch Simulation auch komplexe Produktionsprozesse in der Prozessindustrie besser vorhersagen und optimieren – was beim Wetter ja (noch) nicht möglich ist?
B. Kokkelink: Die Simulation von Anlagen und Prozessen ist eine sehr wichtige Erfolgskomponente der Siemens Digitalisierungsstrategie. Die kürzlich bekannt gegebene Übernahme von Process Systems Enterprise (PSE), einem weltweit führenden Anbieter von Software und Dienstleistungen für hochentwickelte Prozessmodellierung, unterstreicht unseren Anspruch, die Produktionsprozesse unserer Kunden weiter zu optimieren. So wurden mit PSE neue modellbasierte Lösungen für Überwachung, Vorhersage und Monitoring von Anlagen entwickelt, für Soft Sensing, die Vorausberechnung der Anlagenperformance, Echtzeit-Optimierung und Operator Training. Diese Lösungen basieren auf der Verbindung von leistungsstarken Prozessmodellen, fundiertem Prozesswissen auf der einen Seite und Echtzeit- und historischen Prozessdaten auf der anderen.
Mit immer mehr verfügbaren Daten, besseren Algorithmen und immer höheren Rechenleistungen sind die Wettervorhersagen in den letzten Jahren immer besser geworden. Lassen sich durch Simulation auch komplexe Produktionsprozesse in der Prozessindustrie besser vorhersagen und optimieren – was beim Wetter ja (noch) nicht möglich ist?
B. Kokkelink: Die Simulation von Anlagen und Prozessen ist eine sehr wichtige Erfolgskomponente der Siemens Digitalisierungsstrategie. Die kürzlich bekannt gegebene Übernahme von Process Systems Enterprise (PSE), einem weltweit führenden Anbieter von Software und Dienstleistungen für hochentwickelte Prozessmodellierung, unterstreicht unseren Anspruch, die Produktionsprozesse unserer Kunden weiter zu optimieren. So wurden mit PSE neue modellbasierte Lösungen für Überwachung, Vorhersage und Monitoring von Anlagen entwickelt, für Soft Sensing, die Vorausberechnung der Anlagenperformance, Echtzeit-Optimierung und Operator Training. Diese Lösungen basieren auf der Verbindung von leistungsstarken Prozessmodellen, fundiertem Prozesswissen auf der einen Seite und Echtzeit- und historischen Prozessdaten auf der anderen.
Bereits heute haben wir eine sehr gute Interaktion zwischen PSE’s gProms Oilfield und unserer Operations Intelligence Lösung XHQ, um einen digitalen Simulationszwilling zu liefern. XHQ sammelt und organisiert dabei die Daten, verwaltet die Visualisierung und stellt alle relevanten Informationen für gPROMS bereit, so dass entsprechende Simulationsläufe ausgelöst werden können.
C. Gerke: Dies ist sicherlich das Ziel und ein interessantes Anwendungsfeld des Digitalen Zwillings. Zunächst werden wir uns aber auf die etablierten Prozesse konzentrieren und den Betreibern konkrete, verbesserte Betriebsergebnisse liefern. Genau hierin liegt der Anspruch und das Versprechen unserer gemeinsam entwickelten Lösungen zum „Performance Digital Twin“: Intelligentere Produkte und intelligentere Anlagen erzeugen immer umfangreichere Auslastungs- und Effektivitätsdatenmengen. Der digitale Performancezwilling erfasst diese Daten im Betrieb, aggregiert und analysiert sie, um mittels integrierten Artificial Intelligence- und Machine Learning-Technologien in der Simulation der virtuellen Anlage eine fundierte Entscheidungsfindung für effizientere Produkt- und Produktionslebenszyklen und damit mehr Wachstum zu ermöglichen. Dieses ermöglicht dann auch eine Rückkopplung zu den Planungs- / Engineeringphasen, um hier eine performanceoptimierte Auslegung von Beginn an sicherzustellen. Aber Sie haben Recht – wir stehen erst am Anfang einer ganz spannenden neuen Welle von Anwendungsmöglichkeiten des Digitalen Zwillings!