Ergebnis einer erfolgreichen Zusammenarbeit zwischen Endanwender und Dichtungshersteller
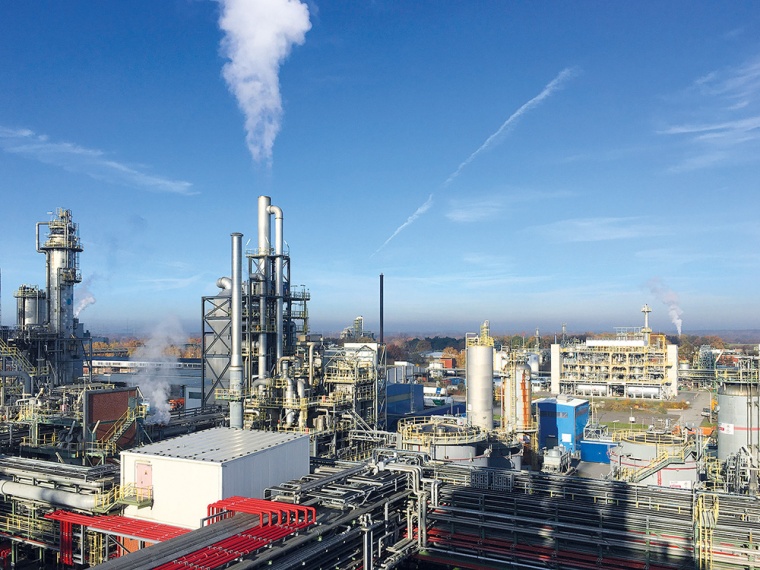
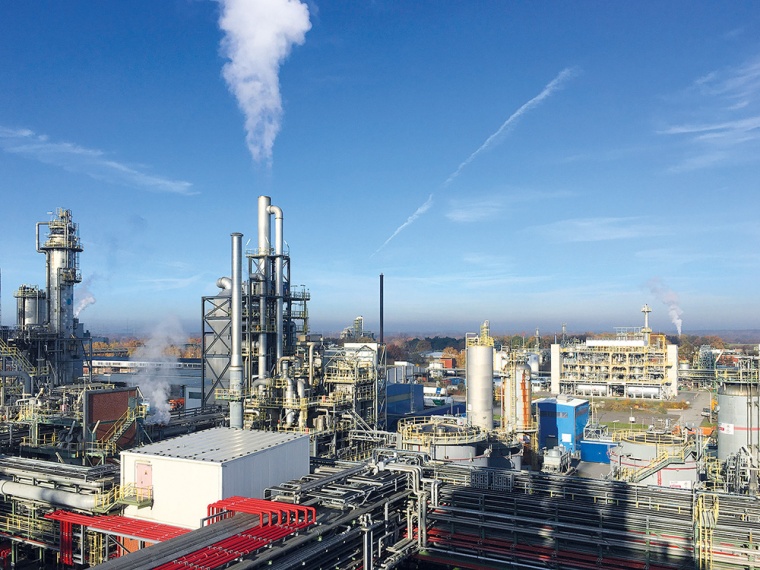
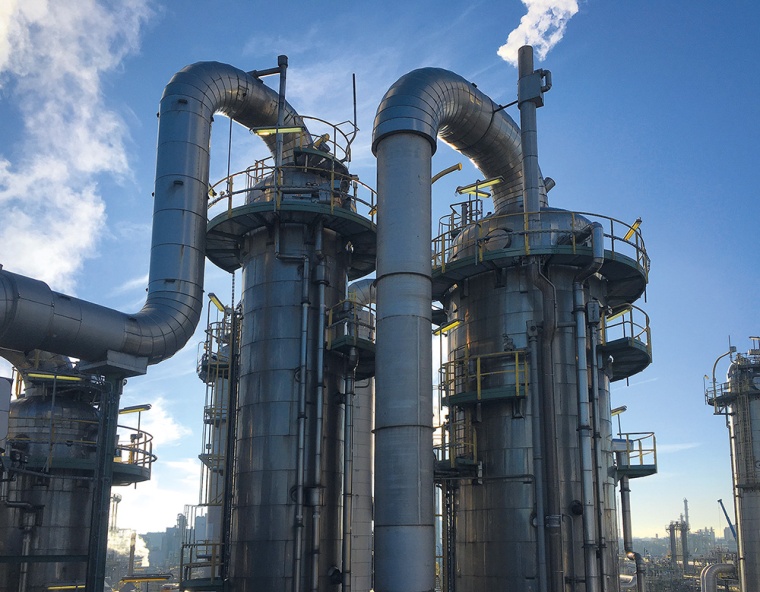
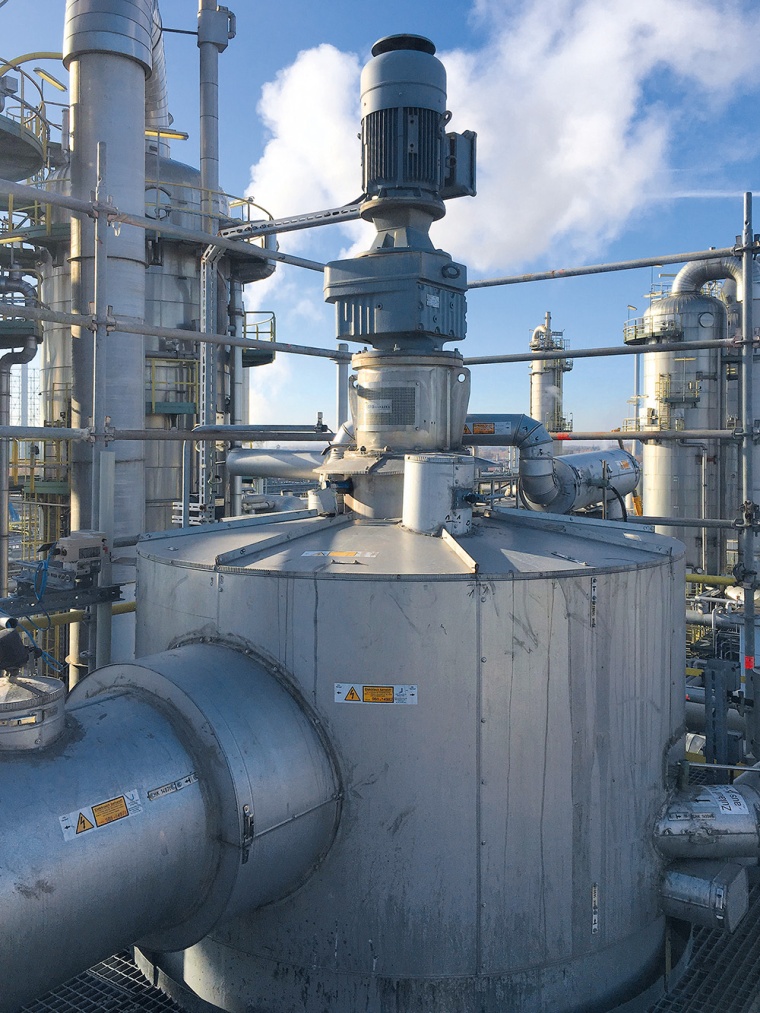
Standzeiten gehören zu den wichtigsten Themen in der produzierenden Industrie – und dabei gleichzeitig im Fokus: Maintenance-Kosten reduzieren. Evonik beauftragte die Fa. Chetra Dichtungstechnik ein Konzept zur Standzeitverbessrung der Gleitringdichtungen bei diesen Pumpen zu erstellen. Das Münchener Unternehmen stimmte mit der Technikleitung, dem Betriebsingenieur und zuständigen Meister von Evonik die Anforderungen und Möglichkeiten hierzu ab.
Der Dichtungsspezialist empfahl die Verwendung von gasgeschmierten Doppel-Gleitringdichtungen der Typen „370G“ und „877 GS“ betrieben mit API Plan 74.
Gasgeschmierte Gleitringdichtungen sind anspruchsvoll, haben aber gerade in einer Acrylsäureanlage den Vorteil, dass im Fall einer Leckage Luft kein „ungebetener Gast“ im Medium ist. Bei den vorherigen Anwendungen mit einem flüssig geschmierten API Plan 53A sah dies anders aus, da das Produkt kontinuierlich in das Sperrmedium diffundierte. Das führte dazu, dass das Thermosyphongefäß in regelmäßigen Abständen gereinigt werden musste und die Gleitringdichtung darüber hinaus versagte, weil auch Produkt in die dynamischen O-Ringe der Gleitringdichtung eindrang und diese zerstörte was dann zum Ausfall des Dichtungssystems führte.
Modifizierte gasgeschmierte Gleitringdichtungen
Nach diversen Tests wurden die gasgeschmierten GLRD Typ 370 G und 877GS in den Durchmessern 33, 43, 53, 64, 65, 85, 95 und 100 mm speziell auf die Gegebenheiten von Evonik modifiziert und ausgelegt. Im Hinblick auf das abzudichtende Medium wurden die GLRD mit hochbeständigen Werkstoffen ausgeführt.
Die zuvor eingesetzten GLRD hatten eine MTBR (Standzeit) von einigen Monaten bis max. einem Jahr; im höheren t-Bereich in aller Regel < 6 Monate. Die erste Chetra-GLRD, Typ 370G-043 lief auf Anhieb > 2 Jahre.
Aufgrund der guten Ergebnisse hat Evonik sukzessive umgerüstet, so dass mittlerweile in nahezu allen Anlagenpumpen gasgeschmierte GLRD des Münchener Dichtungsspezialisten eingebaut sind. Neben einer deutlichen Verbesserung des MTBR konnte eine Reduzierung der Maintenance-Kosten erreicht werden. Zudem läuft die Produktion in der Anlage längerfristig störungsfrei. Die robuste Konstruktion und Verwendung massiver Gleit-/Gegenringe senkt die Reparaturkosten, das Cartridge-Design der GLRD ist angepasst an DIN – und Ansi-Einbauräume.
Weitere Verbesserungen gewünscht
Aber nicht nur die Verbesserung der Standzeiten an Pumpen stand im Pflichtenheft. Evonik besitzt auch einige Rührwerke in den Anlagen an denen Verbesserungen nötig waren. Auch hierbei handelte es sich um eine Anwendung in der Acrylsäure-Anlage, in diesem Fall um einige Rührer, bei denen z. T. 2–3 Mal pro Jahr die Doppel-Gleitringdichtung zur Reparatur anfiel.
Wie im vorherigen Fall erfolgte eine enge Abstimmung zwischen allen Beteiligten. Die Analyse ergab, dass dieser Einsatzfall besser mit einer Rührwerks-Patrone mit mehreren aneinander gereihten Wellendichtringen statt einer herkömmlichen Doppel-GLRD gelöste werden kann. Als zusätzliche Anforderung kam Konformität mit Atex und der TA-Luft hinzu.
Als erster Einsatz wurde die schwierigste Stelle – der „bad actor“ ermittelt und eine Chetra-Dichtung Typ 500-100 vorgesehen. Nach einer Standzeit dieser Dichtung von einem Jahr wurde ein Stillstand angesetzt, der zur Befundung der Dichtung genutzt wurde.
Das Ergebnis zeigte folgendes:
- praktisch keinen messbaren Verschleiß
- alle Dichtelemente ohne Befund
- optimale Leckagewerte
Die Dichtungspatrone wurde gesäubert und wieder in Betrieb genommen – bis heute, Jahre später – läuft die Dichtung ohne Ausfälle.
Fazit
Zwischenzeitlich wurden weitere Abmessungen in Dw: 80, 100, 125, 150 und 180 des Chetra Dichtungstyps „500“ eingebaut und laufen störungsfrei. Weitere Optimierungen z. B. an Gleitringichtungssystemen von Vakuummaschinen sind geplant. Dank der hervorragenden Zusammenarbeit zwischen dem Anwender und dem Dichtungslieferanten sind solche Ergebnisse möglich. Hierzu zählen auch In-house-Schulungen bei Evonik bezüglich der Dichtungen sowie der Fahrweise. Mittlerweile hat Chetra ein Service Center ganz in der Nähe des Chemieparks Marl eingerichtet um in der Reaktionszeit noch schneller sein zu können