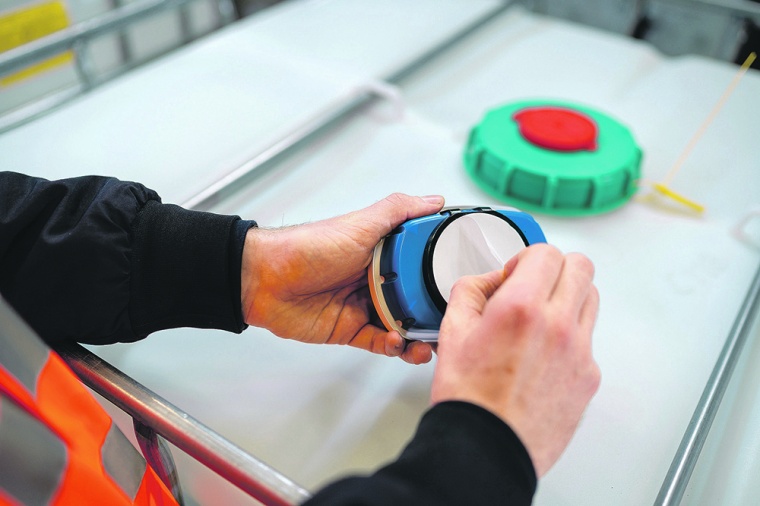
Durch die Digitalisierung der Lieferkette wird diese transparent, Prozesse werden optimiert und damit auch nachhaltiger. Wie das geht, zeigt die Erfindung des Dresdner Start-ups „Packwise“. Das Plug & Play-Gerät „Packwise Smart Cap“ macht analoge Flüssigkeitscontainer digital nachverfolgbar. Zur Nutzung des Geräts muss dieses dauerhaft mit dem Flüssigkeitscontainer verbunden werden, dazu wurde als Entwicklungspartner der Neuwieder Klebebandspezialist Lohmann mit ins Boot geholt. Welche Rolle das Hightech-Klebeband bei der Containerkommunikation spielt, erläutern Felix Weger, Produktmanager und Firmenmitbegründer von Packwise, und Peter Harendt, Leiter Technisches Marketing bei Lohmann.
Herr Weger, Sie vernetzen die Verpackung mit dem Internet. Wie genau geht das?
Felix Weger: Wir statten IBCs mit zusätzlicher Elektronik aus, die unabhängig von Hersteller und Inhalt sind. Das Anbringen ist dank dem Lohmann Klebesystem sehr einfach und kann so auch nachträglich auf bestehenden Containern geschehen. Zunächst wird die Packwise Smart Cap aktiviert. Dann entfernt man die Folie des Klebesystems und bringt die Smart Cap auf den Container auf. Nach circa fünf Minuten ist der Verbund geschaffen, das heißt man kann die Klebung fast nicht mehr lösen. Etwa zur gleichen Zeit sind die Container-Daten bereits auf dem Handy.
Dies ist eine besondere Klebelösung im Bereich der Sensorik. Herr Harendt, welche Bedeutung messen Sie dem Einsatz solcher spezieller Klebelösungen zu?
Peter Harendt: Hier sehen wir einen Trend, Sensorik verklebbar zu machen, der sich immer mehr etabliert hat. Erfolgreiches Kleben hat viel Vertrauen geschaffen und dadurch wurden viele neue Produkte möglich. Wir haben die aktuellen Verbindungsherausforderungen der Elektronik identifiziert, zum Beispiel die Verbindung von Klebelösungen mit Sensorik und Diagnosesystemen. Dazu gehören zum Beispiel die Medizin und andere Bereiche, in denen sich das Kleben als optimale Lösung gezeigt hat.
Mit Hilfe der Packwise Smart Cap erhält der Kunde mit wenig Aufwand sehr viele Daten über seine Containerflotte. Wie entstand diese innovative Idee?
F. Weger: Die Idee ist aus der beruflichen Herausforderung entstanden. Ich habe für einen IBC-Hersteller gearbeitet und wir haben unseren Kunden geholfen, die Verpackungen in Kreisläufen zu organisieren. Das klingt erst einmal sehr einfach. Aber wenn man einen Kunden hat, der tausende von Containern managt und das alles per Excel oder Telefon organisiert, war das sehr zeitraubend. Da kam uns die Idee, einen Sensor zu entwickeln, der den Container quasi überwacht. Mit der Smart Cap können wir den Füllstand, die Temperatur, den Standort und auch Bewegung messen. Damit können wir unseren Kunden exakt mitteilen, wo ihre Verpackungen sind und in welchem Zustand.
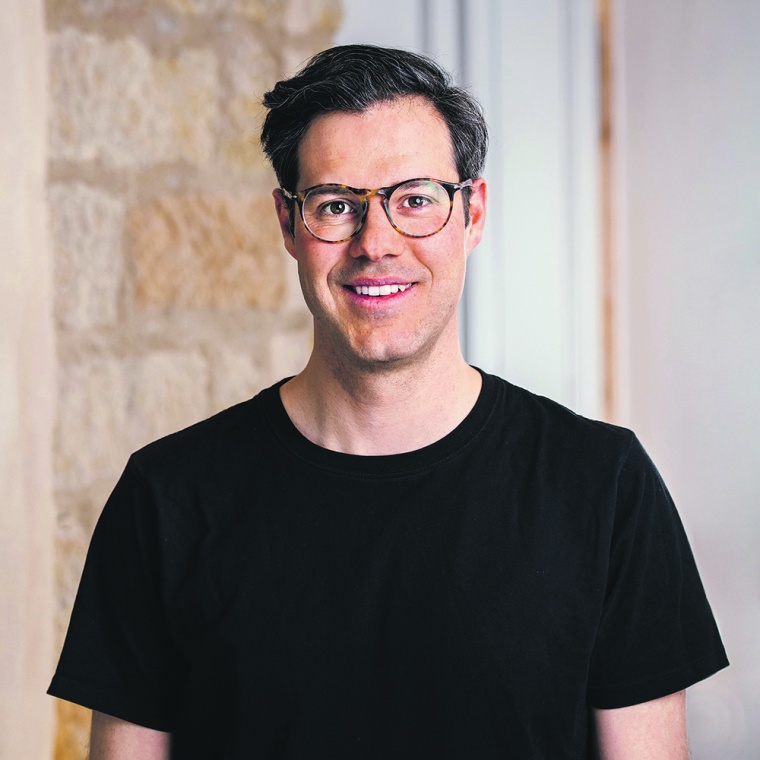
„Wir statten IBCs mit zusätzlicher Elektronik aus, die unabhängig von Hersteller und Inhalt sind.“
Ein wesentlicher Bestandteil der Smart Cap ist die Verbindung der einzelnen Komponenten. Wie kamen Sie zu Lohmann als Entwicklungspartner?
F. Weger: Anfangs dachten wir, die Smart Cap in den Containerdeckel zu setzen und haben einen Deckel mit der Sensorik entwickelt. Da diese Container Gefahrgut auf der Straße transportieren dürfen, war eine entsprechende Zulassung unserer Lösung nötig. Die Zulassungsbehörde erklärte uns jedoch, dies sei eine so starke Veränderung des Containers, dass alle Zulassungen bei allen Herstellern erneuert werden müssten. Das wäre auch aus finanziellen Gründen nicht möglich gewesen. Daraufhin haben wir nach neuen Lösungen gesucht. Ich erinnerte mich an einen früheren Kontakt mit Lohmann, bei einer komplexen Anwendung in Sachen Fotovoltaik-Modulen. Damals war ich erstaunt, was die Klebungen leisten. Nach der Schilderung unserer Anwendung ist die Klebelösung für die Smart Cap recht schnell mit Lohmann entstanden.
Welche besonderen Anforderungen muss ein Klebeband für diese spezielle Applikation erfüllen?
P. Harendt: Zunächst mussten wir die Anwendung genau verstehen. Welche Belastungen entstehen in der Klebung und welches ist die wesentliche Anforderung? Diese war primär, dass man bei diesen Con-tainern auf HDPE, also Polyethylen mit hoher Dichte, und damit auf eine sehr niederenergetische Oberfläche klebt. Damit erfolgte die Klebstoffauswahl nach den Prämissen: niederenergetische Oberfläche und raue Strukturen. Zudem muss unter Umgebungsbedingungen, also auch bei niedrigen Temperaturen, geklebt werden. Ein weiterer wesentlicher Punkt bei der Klebebandauswahl war es, zu verstehen, dass das Smart-Cap-System auf dem Con-tainer transportiert wird, das heißt das Klebeband muss auch Witterungseinflüssen standhalten, die wir so zunächst nur erahnen konnten. Auch gibt es starke Erschütterungen und Vibrationen während des Transports, bei der das Klebeband als Dämpferelement fungieren muss.
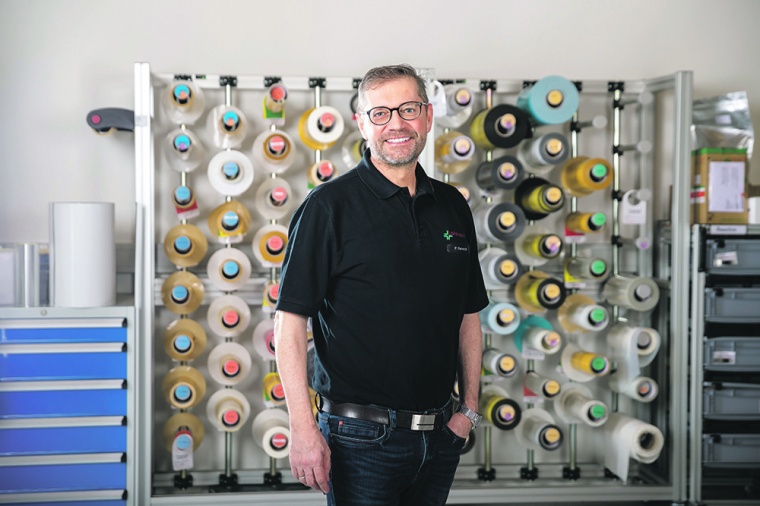
„Erfolgreiches Kleben hat viel Vertrauen geschaffen und dadurch wurden viele neue Produkte möglich.“
Wie wurde die Eignung der Klebelösung geprüft?
P. Harendt: Wir haben in unseren Laboren mit verschiedenen Klebebandvarianten Voruntersuchungen durchgeführt. Dazu gehörten beispielsweise Abzugstests für die Ermittlung der maximalen Festigkeit. Auch die niederenergetische Oberfläche haben wir getestet, um gegebenenfalls Vorbehandlungsmethoden für den späteren Prozess zu evaluieren. Da die Geräte aber später von Hand und durch jedermann aufgeklebt werden müssen, war schnell klar, dass allein ein geeignetes Haftklebstoffsystem für die volle Festigkeit sorgen muss. Also keine Primer oder andere physikalische Vorbehandlungsmethoden. Weiterhin haben wir die Medienbeständigkeit gegen mögliche äußere Einflüsse getestet. Alle diese Faktoren wurden zunächst hier auf Laborebene getestet, um das richtige Klebeband auszuwählen und danach erfolgte die Eignungsprüfung am Bauteil.
Wie ging es nach der Spezifikation des Klebebands weiter?
F. Weger: Wir haben das Produkt unserem Fertigungspartner übergeben und waren überrascht, als wir später im Prozess bemerkten, dass noch weitere Wertschöpfungsschritte dazu gekommen sind. So ist zusätzlich noch ein sehr sensibler RFID-Tack verklebt. Dort ist ebenso eine Klebelösung von Lohmann genutzt worden, die neben der Klebung auch für den nötigen Abstand der RFID-Antennen zu metallischen Komponenten sorgt.
⇒⇒⇒⇒⇒⇒⇒⇒⇒⇒⇒⇒⇒⇒⇒⇒⇒⇒⇒⇒⇒⇒⇒⇒⇒⇒⇒⇒⇒⇒⇒⇒⇒⇒⇒⇒⇒⇒⇒⇒⇒⇒⇒⇒⇒⇒⇒⇒⇒⇒⇒⇒⇒⇒⇒⇒⇒⇒
Zur Person
Felix Weger ist Mitgründer des IoT-Unternehmens Packwise und arbeitet derzeit als Produktmanager. Für die Produktentwicklung und Vermarktung ist er seit Januar 2017 verantwortlich. Dabei hat er den gesamten Produktlebenszyklus im Blick und analysiert die Bedürfnisse des Marktes und der Kunden in der chemischen Industrie. Vor seiner Tätigkeit bei Packwise war der Diplom-Volkswirt als Produktionsleiter bei Werit in Deutschland und UK tätig.
⇒⇒⇒⇒⇒⇒⇒⇒⇒⇒⇒⇒⇒⇒⇒⇒⇒⇒⇒⇒⇒⇒⇒⇒⇒⇒⇒⇒⇒⇒⇒⇒⇒⇒⇒⇒⇒⇒⇒⇒⇒⇒⇒⇒⇒⇒⇒⇒⇒⇒⇒⇒⇒⇒⇒⇒⇒⇒
Peter Harendt ist seit 20 Jahren bei Lohmann und leitet den Bereich Technical Marketing. Als Klebfachkraft (European Adhesive Specialist) besitzt er ein breitgefächertes Wissen in Sachen Haftklebetechnik, entwickelt Klebelösungen und stellt sie für Kunden international zur Verfügung. Harendt baut zudem für Lohmann das sog. „Bonding Engineer College“ auf, ein Trainingsprogramm, das darauf abzielt, haftklebetechnisches Wissen Mitarbeitenden, Kunden und Partnern auf vielfältige Weise zu vermitteln
⇒⇒⇒⇒⇒⇒⇒⇒⇒⇒⇒⇒⇒⇒⇒⇒⇒⇒⇒⇒⇒⇒⇒⇒⇒⇒⇒⇒⇒⇒⇒⇒⇒⇒⇒⇒⇒⇒⇒⇒⇒⇒⇒⇒⇒⇒⇒⇒⇒⇒⇒⇒⇒⇒⇒⇒⇒⇒