Prozesstechnologie für hohe Ansprüche
Korrosive Medien werden vielfach in der chemischen Industrie eingesetzt. Sie stellen besondere Anforderungen an das Material von Apparaten.
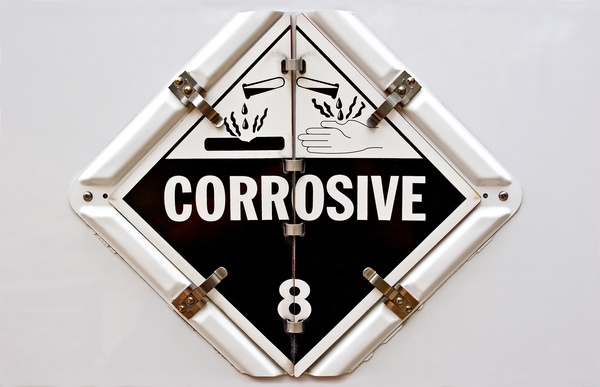
Um die Verfahren an individuelle Bedürfnisse anzupassen, sind Materialexpertise und Prozess-Know-how gefragt. Dabei müssen die verschiedenen Designkriterien genau abgestimmt und gewichtet werden. Wechselnde Rahmenbedingungen setzen hierbei immer wieder neue Schwerpunkte in der Verfahrensauswahl.
Sicherheit und Anlagenverfügbarkeit stehen bei korrosiven Anwendungen im Fokus. Anlagenstillstände kosten Zeit und Geld. Prozessingenieure konzentrieren sich deshalb darauf, die Komplexität der Verfahren zu minimieren und die Prozessbedingungen auf die Einsatzmöglichkeiten der Materialien abzustimmen. Fallspezifisch werden weitere Aspekte, wie z.B. Platzbedarf, Anfahrzeit und Leistungsbereich sowie Materialverfügbarkeit und Lieferzeit beleuchtet.
Energiepreise und Nachhaltigkeitsziele setzen neue Akzente
Neuer Schwerpunkt in Zeiten steigender Energiepreise, strengerer Emissionsrichtlinien und ambitionierter Nachhaltigkeitsziele ist die Effizienz in Bezug auf Energieeinsatz und Materialausbeute. Es gilt diese Faktoren optimal auszubalancieren, um aus den Investitionskosten einen möglichst hohen Anlagenwert zu generieren. Speziell bei Anwendungen mit korrosiven Medien müssen dabei Standzeiten und Servicekosten berücksichtigt werden. Wie diese Designkriterien Einfluss auf die Verfahrenswahl nehmen können, zeigen zwei Beispiele aus dem Salzsäurebereich.
Optimiert für Langlebigkeit und minimale Stillstandzeiten: die HCl-Synthese
Salzsäure wird typischerweise in speziellen Graphitapparaten erzeugt. In diesen HCl-Synthesen reagiert Chlor mit Wasserstoff stark exotherm zu Chlorwasserstoffgas (HCl). Eine integrierte Absorptionseinheit löst das HCl in Wasser und bildet Salzsäure. Über Jahrzehnte wurden diese Apparate optimiert, um den toxischen, hochkorrosiven und potenziell explosiven Bedingungen bei bis zu 2.500 °C standzuhalten. Das Sicherheitskonzept umfasst den vollautomatischen Start-, Zünd- und Abfahrvorgang und die kontinuierliche Überwachung aller sicherheitsrelevanten Prozessdaten sowie ein Aufstellungskonzept, das kurze Fluchtwege und sichere Druckentlastung gewährleistet. Zur Maximierung der Anlagenverfügbarkeit setzen SGL-Experten auf moderate Materialtemperaturen, sowie auf einen leicht zugänglichen, wartungsfreundlichen Brenner. So bieten spülbare Graphitbrennerrohre die einzigartige Möglichkeit, Salzverkrustungen während des laufenden Betriebs zu entfernen, und helfen damit, Stillstandzeiten zu vermeiden.
Mit Dampf zu mehr Effizienz
Eine signifikante Steigerung der Effizienz ermöglicht die patentierte Ecosyn-Synthese, welche die enorme Energie der Verbrennungsreaktion weitestgehend als Dampf zurückgewinnt. So kann pro Tonne umgesetzten Chlors eine Tonne Dampf erzeugt werden. Das adaptierte Design basiert auf dem Konzept des Großwasserraumkessels und ermöglicht die Kombination aus bewährtem Sicherheitskonzept, zuverlässiger Brennerrohrtechnologie und Wärmerückgewinnung. Zur Erzeugung von Dampfdrücken von über 10 barg wird Stahl als Konstruktionswerkstoff für den Ofen eingesetzt. Das Konzept des Großwasserraumkessels bringt den entscheidenden Konstruktionsvorteil, da alle prozessmedienberührenden Bauteile temperiert sind und somit die Gefahr von Korrosion durch kondensierte Salzsäure minimiert wird. Zudem werden keine Heißwasserkreislaufpumpen benötigt – ein weiterer Effizienzfaktor, der sich auch positiv auf die Verfügbarkeit und die Servicekosten auswirkt. Derzeit ist das Ecosyn-Konzept vor allem in der Chlor-Alkali-Industrie gefragt, wo der erzeugte Dampf direkt zur Eindampfung von Natronlauge eingesetzt werden kann.
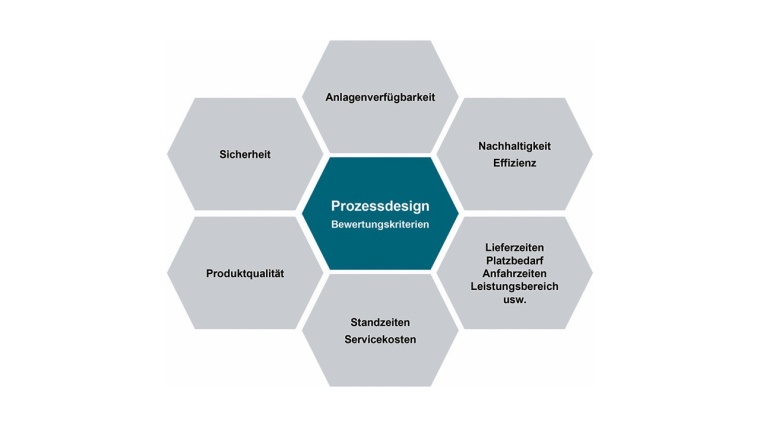
Zwei Konzepte, viele Möglichkeiten: die Salzsäurerückgewinnung
Verdünnte Salzsäure tritt in vielen chemischen Prozessen als Nebenprodukt auf. Soll sie vollständig in Chlorwasserstoff und Wasser getrennt werden, reicht eine einfache Destillation nicht aus, da die beiden Stoffe ein Azeotrop bilden. Um die azeotrope Konzentration zu überwinden, kann die Extraktivdestillation oder das Druckwechselverfahren eingesetzt werden. Ein Blick auf die charakteristischen Merkmale dieser beiden Konzepte zeigt, dass die Entscheidung zwischen ihnen von diversen Faktoren abhängt. Die oft herangezogene, vereinfachte Gegenüberstellung von Betriebs- und Investitionskosten greift oft zu kurz.
Speziell die Bewertung der Anlagenverfügbarkeit ist ein wichtiger Aspekt. Bei Extraktivverfahren, die Salze als Schleppmittel einsetzen, spielt das Ausfallrisiko aufgrund von möglichen Salzausfällungen eine Rolle. Große Abstände zum Kristallisationspunkt reduzieren aber die Effizienz und Ausbeute. Schwefelsäure als Schleppmittel kann die Lebenszeit der Graphitapparate reduzieren. Ein weiteres Prozessrisiko stellen Verunreinigungen dar, die mit dem Schleppmittel reagieren und zu Ablagerungen führen.
Auch bei der Produktqualität unterscheiden sich die beiden Verfahren. Das Druckwechselverfahren setzt kein Schleppmittel ein, das zur Erhöhung der Siedetemperatur führt. So können deutlich höhere HCl-Gasdrücke erzeugt werden, die gegebenenfalls einen Verdichter mit Trocknungseinheit überflüssig machen. Das Ergebnis: Kosten und Komplexität der nachgeschalteten Anlage werden signifikant reduziert, Schleppmittelverunreinigungen und ihre negativen Effekte ausgeschlossen. Die Trennkolonne zur Wasserausschleusung, die im Druckwechselverfahren benötigt wird, steigert zwar die Investitionskosten, ermöglicht aber höhere Ausbeuten und damit höhere HCl-Rückgewinnungsraten, da Abwasser mit sehr niedrigen HCl-Konzentrationen erzeugt werden kann. Dies bringt Vorteile bei der Abwasserbehandlung und führt zu Kosteneinsparungen bei Betreibern, die hohe Transportkosten für die Bereitstellung der Salzsäure aufwenden. Hohe HCl-Rückgewinnungsraten wirken sich zudem nachhaltig auf die Chlorid-Kreislaufwirtschaft aus.
Das Hauptaugenmerk liegt bei den beiden vorgestellten Verfahren auf dem Energiebedarf. Beim Extraktivverfahren, das einen grundlegend niedrigeren Energiebedarf im Vergleich zum Druckwechselverfahren aufweist, bietet sich zur Wasserabtrennung eine mehrstufige Eindampfung an. Eine Möglichkeit, die Komplexität und den Platzbedarf der Anlage zu minimieren, ist die Konzentrierung des Schleppmittels unter erhöhtem Druck. Der erzeugte Dampf kann dabei direkt im HCl-Destillationsbereich eingesetzt werden. Der Betrieb bei erhöhter Temperatur und Druck mag Einfluss auf den Konstruktionswerkstoff haben, verringert aber das Risiko, den Kristallisationspunkt zu unterschreiten. Interessant ist zudem die Verwendung eines Brüdenverdichters in einem Sekundarkreislauf. Durch den Einsatz von Strom kann dabei auf einen Großteil der eingesetzten Dampfmenge verzichtet werden. Dies trägt vor allem bei Einsatz regenerativer Stromquellen zur Nachhaltigkeit bei. Auch das Druckwechselverfahren ermöglicht vielfältige Arten der Wärmeintegration. Die Wasserdestillation erfolgt typischerweise im Vakuum bei niedrigen Temperaturen, was Optionen zur Nutzung von Abwärmeströmen bietet. Hier können ebenfalls Konzepte der Brüdenkompression eingesetzt werden, um das Verfahren weiter energetisch zu optimieren.
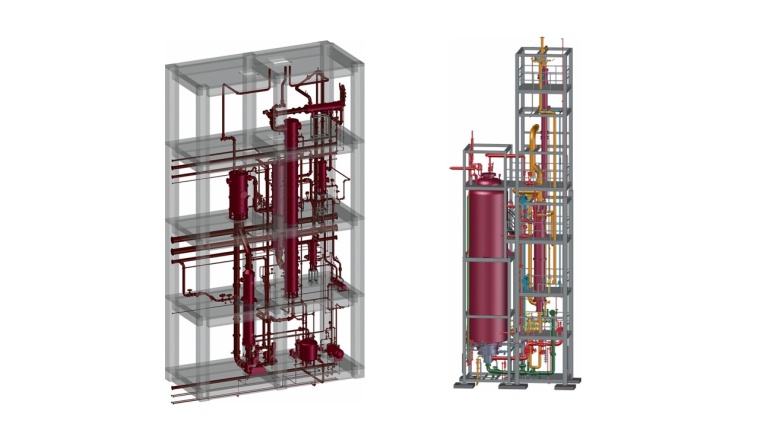
Individuelle Lösungen für nachhaltigen Erfolg
Wie die beiden gezeigten Anwendungen verdeutlichen, ist die Auswahl geeigneter Verfahren in der Prozesstechnik groß und eine ganzeinheitliche Herangehensweise zwingend notwendig. Die Auswahl, Gewichtung und Priorisierung der einzelnen Designkriterien erfordern einen engen Austausch, besonders wenn mit den Aspekten der Nachhaltigkeit und Effizienz weitere Faktoren an Bedeutung gewinnen. Die Experten von SGL Carbon gestalten gemeinsam mit ihren Kunden optimal angepasste Systeme.
Autor: Christian Woltz, SGL Carbon
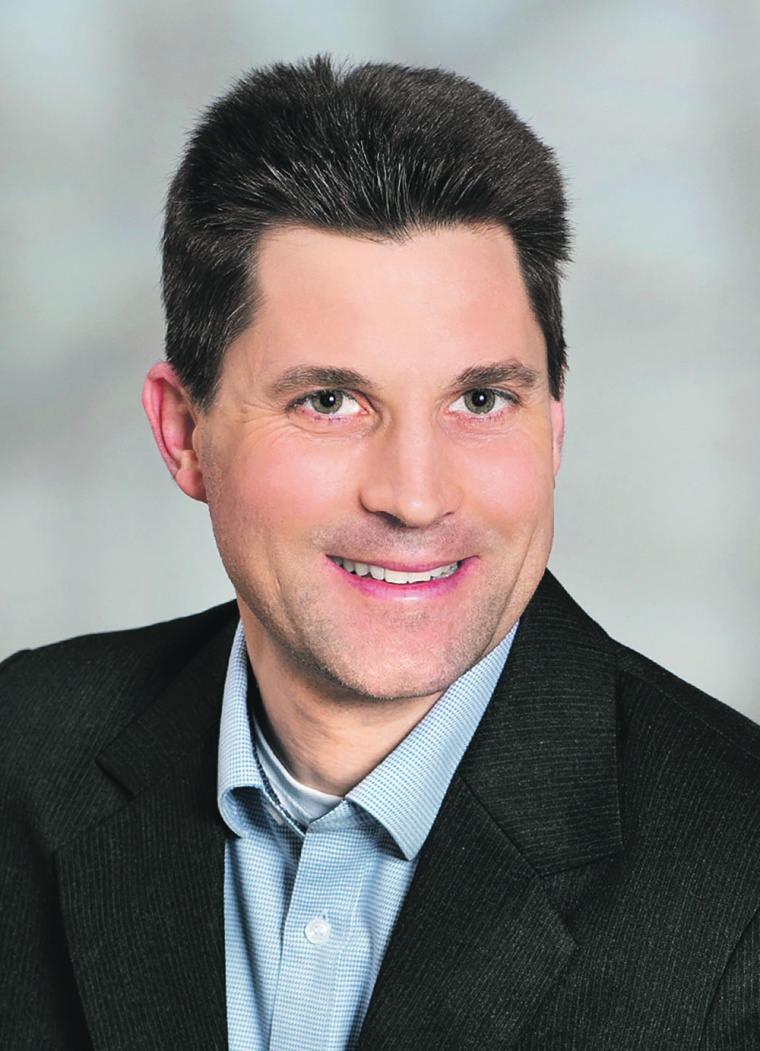