Schnelligkeit und Sicherheit im Stückgutumschlag
Ob IBC, Paletten mit Fässern oder Sackware, im Dachser-Umschlaglager haben alle Versandstücke eines gemeinsam – sie werden im Eingang und Ausgang sowie bei der Hallenaufnahme von den Mitarbeitenden manuell gescannt.
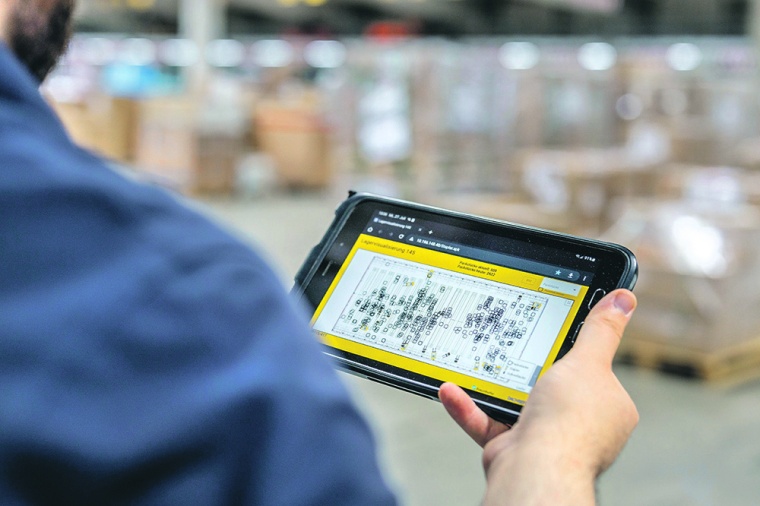
So wird ein reibungsloser Weitertransport gewährleistet. In zwei Umschlaglagern erfolgt dieser Prozess seit Kurzem voll automatisiert und damit schneller und transparenter, indem mit dem Einsatz neuer Technologien ein digitaler Zwilling aller Packstücke und Abläufe erzeugt wird. Von den Prozessverbesserungen profitieren Kunden, Mitarbeitende und Servicepartner gleichermaßen, denn Schnelligkeit und Sicherheit im Umschlaglager werden zusätzlich erhöht.
In den Umschlaglagern in Unterschleißheim im Norden Münchens sowie in Öhringen bei Heilbronn ist jedes Packstück mit einem quadratischen Datamatrix-Code in der Größe eines Bierdeckels versehen. Dieser Datamatrix-Code bildet die Basis von @ILO, einem Forschungsprojekt aus dem Dachser Enterprise Lab, das gemeinsam mit dem Fraunhofer Institut für Materialfluss und Logistik in Dortmund betrieben wird. @ILO steht für „Advanced Indoor Localization and Operations“ und beschreibt den neuen, digitalen Zwilling. Dieses digitale Abbild soll künftig vollautomatisch Echtzeitdaten zu jeder palettierten Sendung im europäischen Transportnetzwerk des Unternehmens liefern.
Mit dem System werden wichtige operative Kernprozesse digitalisiert – ein Meilenstein auf dem Weg zu effizienteren und nachhaltigeren Logistikoperationen, da eine neue Stufe der Transparenz über die Abläufe im Umschlaglager erreicht wird. Das innovative Projekt ist Teil des Forschungs- und Entwicklungsprogramms „Dachser Future Terminal“, mit dem Themen der Digitalisierung und Nachhaltigkeit mit innovativen Ideen vorangetrieben werden.
Vollautomatische Identifizierung
In den @ILO-Terminals werden Packstücke beim Eintritt, Aufenthalt und Verlassen des Umschlaglagers vollautomatisch identifiziert und im firmeneigenen Transportmanagementsystem erfasst. Manuelle Barcode-Scanvorgänge am Warenein- und -ausgang sind nicht mehr notwendig. Damit werden auch die Mitarbeitenden entlastet.
Technologische Basis sind Datamatrix-Codes auf der Oberseite eines jeden Packstücks sowie mehrere hundert optische Scaneinheiten im Deckenbereich der Umschlaghallen, die den gesamten Hallenboden erfassen. Diese liefern auf effiziente Weise die notwendigen Daten für ein digitales, jederzeit aktuelles Abbild des Umschlaglagers – den digitalen Zwilling.
Alle erfassten Informationen fließen in das Herzstück des digitalen Zwillings, die @ILO-Software. Neue spezielle KI-basierte Algorithmen interpretieren die im Sekundentakt von den optischen Scaneinheiten erfassten Daten, um so das automatische Identifizieren, Lokalisieren und Vermessen aller Packstücke in Echtzeit zu gewährleisten. Funkbasierte Lösungen wie RFID (Radio-Frequency Identification) und BLE (Bluetooth Low Energy) wurden ebenfalls getestet. Diese Lösungen konnten die Anforderungen jedoch nicht erfüllen.
Die Datamatrix-Codes übermitteln dieselben Informationen zur Sendung wie die aktuell üblichen NVE-Barcodes, die manuell in den Umschlaglagern abgescannt werden. Eine korrekte und vollständige Gefahrgutkennzeichnung muss allerdings weiterhin separat und gemäß den entsprechenden Vorschriften erfolgen.
Ortung bis auf den Meter genau
Eine Innovation in diesem Terminal ist die metergenaue Ortung aller Paletten in Echtzeit in den Fußballfeld-großen Umschlaglagern. Dadurch verkürzen sich Beladeprozesse deutlich, Suchprozesse entfallen – insbesondere die Fahrer im Nahverkehr profitieren davon. Über den Computer, Smartphone-Apps, E-Ink-Displays, 3D-Visualisierungen oder künftig eventuell auch Laserprojektionen und AR-Brillen lassen sich sowohl die Stellplätze von Packstücken als auch die Position von Flurförderzeugen in Echtzeit visualisieren und bringen die Digitalisierung zu den Mitarbeitenden ins Umschlagterminal.
Logistics Operatives erhalten auf speziellen Displays Leitinformationen für den innerbetrieblichen Transport. Diese können auch mit ergänzenden Informationen wie bspw. den zusätzlichen Gefahrguthinweisen, priorisierten Verladeanweisungen oder mit einem Foto des Packstücks angereichert werden. So erhöhen sich auch Qualität und Sicherheit der Umschlagprozesse.
Eine Neuheit ist zudem die sog. automatische „Verheiratung“ der Flurförderzeuge und Packstücke. @ILO erkennt die Aufnahme einer Palette mit einem Flurförderzeug automatisch. Sobald ein Packstück vom Fahrzeug aufgenommen und registriert wird, wird die hinterlegte Information abgerufen und auf einem Display am Flurförderzeug angezeigt. Die Mitarbeitenden haben auf diese Weise immer im Blick, wohin die Palette transportiert werden soll – und bekommen einen Hinweis, sollte die Palette am falschen Ort abgestellt worden sein.
„Manuelle Barcode-Scanvorgänge am Warenein- und -ausgang sind nicht mehr notwendig.“
Steigerung der Effizienz
Ein weiteres technologisches Highlight des Terminals soll die vollautomatische und permanente Vermessung aller Packstücke werden. Der digitale Zwilling kann Länge, Höhe und Breite der unterschiedlichen Packstücke mit hoher Genauigkeit ermitteln. Möglich macht das der auf künstlichen neuronalen Netzen entwickelte Bildverarbeitungsansatz der Software.
In den beiden Pilotanlagen Unterschleißheim und Öhringen führt die große Zahl an Messpunkten und -daten zu einer höheren Messgenauigkeit, ohne dabei die Transportprozesse im Umschlaglager zu stören oder gar Messstationen anfahren zu müssen. Wenn dieses bisher wohl einzigartige Verfahren in eine Praxistauglichkeit überführt werden kann, lassen sich die ermittelten Volumendaten künftig bspw. von intelligenten Algorithmen nutzen, um Fahrer sowie die Beschäftigten im Umschlaglager bei der Verladungs- und Tourenplanung zu unterstützen. Damit kann die Auslastung von Wechselbrücken, Trailern und Nahverkehrsfahrzeugen noch weiter erhöht werden. Dies würde dann zu einer Reduzierung von Transportkilometern und somit auch zu einer Vermeidung unnötiger CO2-Emissionen führen – ein Ziel, das Dachser im Rahmen seines Nachhaltigkeitsengagements in zahlreichen Projekten verfolgt.
Ein Projekt mit viel Potenzial
Die ersten Ergebnisse sind sehr positiv und deuten darauf hin, dass mit dem @ILO-Terminal eine neue Stufe der Supply Chain Visibility erreicht werden kann. Diese neue Art der Transparenz über alle Warenbewegungen im Umschlaglager und die damit verbundenen Optimierungsmöglichkeiten sollen zukünftig auch Kunden und Partnern verfügbar gemacht werden.
Der Schlüssel zur Entwicklung dieser Innovation für die Stückgutlogistik ist die enge Zusammenarbeit im Dachser Enterprise Lab. Über vier Jahre haben erfahrene Logistikfachleute von Dachser und kreative Fraunhofer-Wissenschaftler gemeinsam an dem digitalen Zwilling gearbeitet. Zum Einsatz kommen Algorithmen, die auf künstlicher Intelligenz basieren. Sie lassen das Internet der Dinge und die Vision von Industrie 4.0 und Logistik 4.0 auch in der Stückgutlogistik Wirklichkeit werden. Zu den Herausforderungen in diesem Umfeld zählten die starke Heterogenität der Umschlaghallen, unterschiedliche Packstückvolumina und das hohe Palettengewicht.
Bereits in den ersten Tests hat sich gezeigt, dass die Mitarbeitenden in den Umschlaglagern, aber auch die Fahrer mit dem System wertvolle Zeit sparen und damit Abläufe im Terminal noch effizienter gestalten. Zudem wird die künftige, automatische Vermessung der Packstücke und eine entsprechende, KI-unterstützte Ladevorplanung helfen, den Lkw optimal zu beladen. Damit kommen Packstücke mit chemischen Produkten noch schneller und mit weniger CO2-Emissionen ans Ziel.
Autor: Michael Kriegel, Department Head Dachser Chem Logistics, Dachser, Kempten
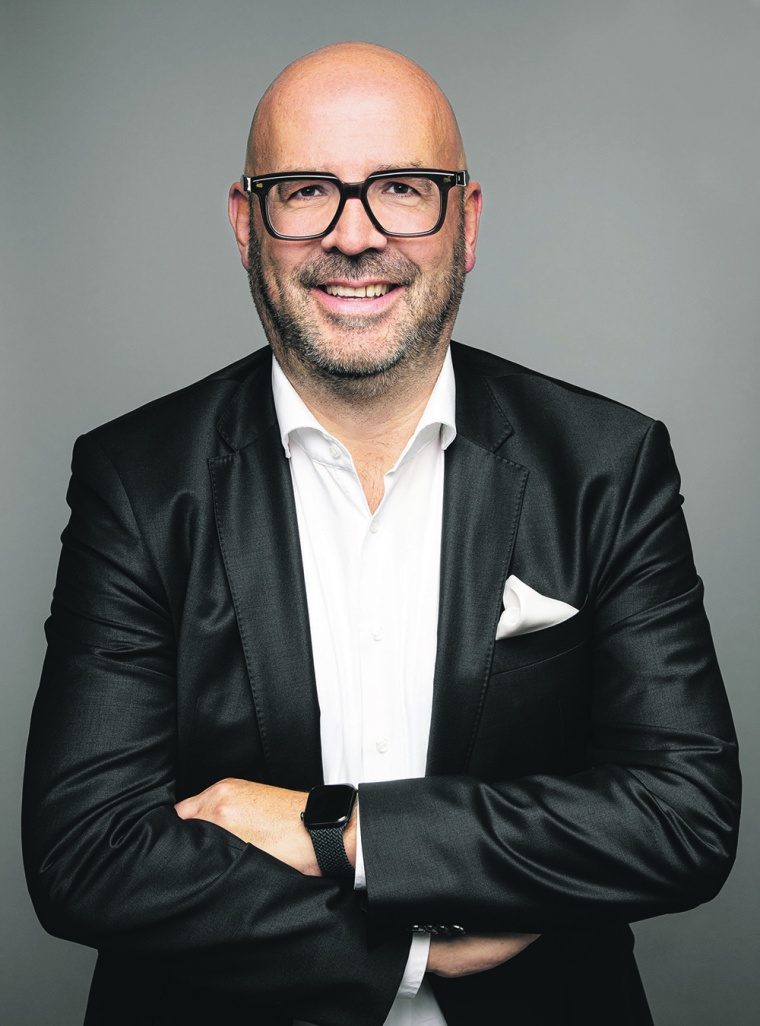
„Mit dem Terminal kann eine neue Stufe der Supply Chain Visibility erreicht werden.“