Mineralöl-Raffinerie Dollbergen: Raffination von Vakuumdestillaten
Rechtzeitig zum 50jährigen Bestehen der Mineralöl-Raffinerie Dollbergen (MRD) wurde am Standort Dollbergen im März 2005 die neue Prozessanlage „Erweiterte Selektiv-Raffination“ mechanisch fertig gestellt und mit der Inbetriebsetzung der Anlage begonnen.
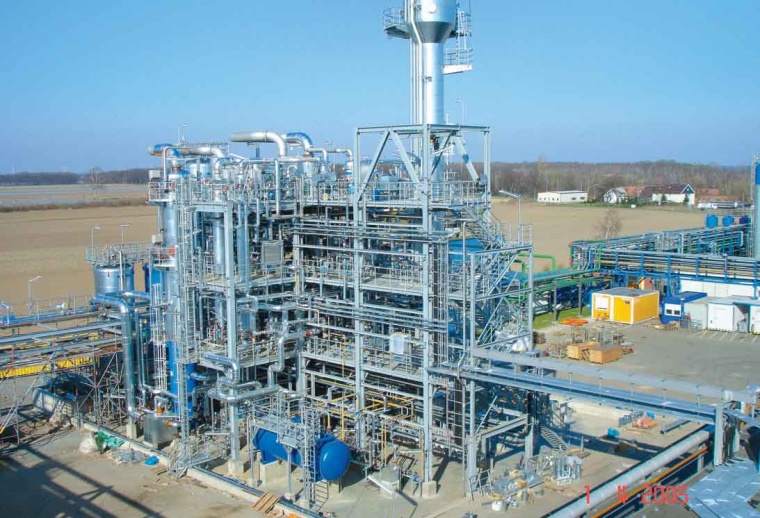
Innerhalb eines Realisierungszeitraumes von nur 12 Monaten hinsichtlich der Planung, Errichtung und Beginn der Inbetriebsetzung der Anlage konnte das Projekt mit Unterstützung durch den international erfahrenen Anlagenbauer Chemieanlagenbau Chemnitz (CAC) erfolgreich umgesetzt werden. Die Inbetriebnahme leitet für die MRD eine neue Epoche der „Re-Refining-Technologie“ ein.
Mit der innovativen MRD Solvent- Extraktions-Technologie zur Raffination von Vakuumdestillaten aus Gebrauchtölen erfüllt die MRD vollständig die Anforderungen an ein modernes Aufbereitungsverfahren für Gebrauchtöle zur Produktion qualitativ hochwertiger Basisöle, die in ihren Eigenschaften den klassischen Solventraffinaten aus Erdöl teilweise sogar überlegen sind. Das ökologisch und ökonomisch innovative Verfahren hat folgende Vorteile: _ Abfallfreies Verfahren _ Deutliche Verbesserung der Basisölqualitäten _ Bedeutender Beitrag zur umweltverträglichen Lösung der Abfallproblematik _ Verminderung von Geruchsemissionen _ Umsetzung des Kreislaufwirtschaftsgesetzes.
„Erweiterte Selektiv-Raffination“
Die „Erweiterte Selektiv-Raffination“ arbeitet nach dem Prinzip der Flüssig-Flüssig- Extraktion. Als Einsatz dienen Vakuum-Destillate aus der innerhalb des Schmierölproduktionsstranges bestehenden und der „Erweiterten Selektiv- Raffination“ vorgeschalteten Prozessanlage Flashdestillation. Diese werden in einem der anfallenden Menge angepassten Produktionszyklus verarbeitet. Vor Eintritt in die eigentliche Extraktionskolonne wird das jeweilige Destillat in einem Absorber durch Dampf von Resten gelösten Sauerstoffs befreit. Danach wird das Destillat im unteren Bereich der Extraktionskolonne aufgegeben. Im Gegenstrom zum schwereren Lösungsmittel, NMethyl- Pyrrolidon, welches am Kopfbereich der Extraktionskolonne aufgegeben wird, steigt das Destillat auf und wird durch das Herauslösen von unerwünschten aromatischen Kohlenwasserstoffen und anderen Verunreinigungen befreit. Die lösungsmittelhaltige Raffinatphase verlässt die Extraktionskolonne am oberen Ende und wird der nachgeschalteten Raffinatrückgewinnungssektion, welche aus einer Destillations- und Strippkolonne besteht, vom Lösungsmittel befreit. Das so gewonnene Raffinat „Kernsolvat“ wird zur weiteren Verwendung in die außerhalb der Prozessanlage angeordneten Produkttanks verpumpt. Am Boden der Extraktionskolonne wird kontinuierlich die sog. Extraktphase abgezogen, auf eine definierte Temperatur gekühlt und in einem Trennbehälter von sich abscheidendem Sekundärraffinat getrennt. Letzteres wird auf die Extraktionskolonne zurückgeführt und damit die Prozessausbeute optimiert. Die Extraktphase aus dem Sekundär-Trennbehälter wird der Extraktrückgewinnungssektion zugeführt und vom Lösungsmittel befreit. Die Extraktrückgewinnungssektion besteht ebenfalls aus einer Destillations- und Stippkolonne. Das anfallende Extrakt wird zur weiteren Verwendung als Raffinerieinterner Energieträger oder Schweröl-Mischkomponente in den außerhalb der Prozessanlage angeordneten Zwischenlagertank verpumpt. Das in der Raffinat- und Extraktrückgewinnungssektionen innerhalb der Destillationskolonnen abdestillierte trockene Lösungsmittel wird auf den Lösungsmittelbetriebstank zurückgeführt. Das in den Raffinat- und Extraktrückgewinnungssektionen innerhalb der Strippkolonnen abdestillierte feuchte Lösungsmittel wird der Lösungsmitteltrocknungskolonne zugeführt und dort von überschüssigem Wasser befreit. Das nunmehr von Wasser befreite „trockene“ Lösungsmittel wird ebenfalls auf den Lösungsmittelbetriebstank zurückgeführt. Von dort kann das trockene Lösungsmittel erneut für die Extraktion in der Extraktionskolonne eingesetzt werden.
Das Projekt
Die Ergebnisse der Verfahrensentwicklung wurden in Zusammenarbeit mit einem in der Raffinerietechnik führenden Ingenieurunternehmen in ein vorläufiges „Basic Engineering“ umgesetzt und sind die wesentliche Grundlage für alle weiteren daran anknüpfenden Aktivitäten zur Vorbereitung des Projektes zur Planung und Errichtung der „MRD-Selektiv- Raffination“. In Folge des Innovationscharakters des Verfahrens, welches abfallfrei, umweltfreundlich und ressourcenschonend ist, erhielt die MRD 2001 eine finanzielle Förderung von 1,55 Mio. € bei der EU im Rahmen des LIFE-Umweltprogramms. Mit Verkauf der MRD an den neuen Eigentümer, die Mustad International Oil Recycling Group, im Jahre 2003 und einer damit verbundenen Zusammenführung des technologischen Know-how’s führte zu einer gemeinsamen Optimierung des Verfahrenskonzeptes. Dementsprechend wurde das Projekt in „Erweiterte Selektiv- Raffination“ umbenannt. Der Investitionsaufwand für die Gesamtprojektumsetzung wurde durch MRD mit 13 Mio. € ermittelt. Eine weitere finanzielle Förderung in Höhe von 0,84 Mio. € erhielt MRD 2004 im Rahmen des „Forschungs- und Entwicklungsprogramms“ des Landes Niedersachsen. Ohne diese Zuschüsse wären Investitionen dieser Größenordnung für mittelständische Unternehmen finanziell nicht realisierbar.
Die Projektabwicklung
Der nun für eine zügige Projektumsetzung zur Verfügung stehende Realisierungszeitraum von nur 12 Monaten hinsichtlich der Planung, Errichtung und Beginn der Inbetriebsetzung der Anlage war mit den bei MRD vorhandenen personellen Ressourcen nicht sicherzustellen und bedurfte der externen Unterstützung durch ein raffinerieerfahrenes Anlagenbauunternehmen. Hierbei hat sich das Unternehmen Chemieanlagenbau Chemnitz (CAC) als der maßgebliche Partner empfohlen und im Sinne einer partnerschaftlichen Zusammenarbeit mit MRD dieser anspruchsvollen Herausforderung gestellt. Der durch MRD an CAC beauftragte Leistungsumfang beinhaltete neben dem gesamten Detail Engineering, die Beschaffung aller für die Anlage erforderlichen Lieferungen und Leistungen sowie die Durchführung der Baustellenleitung / Montageüberwachung. Die Planung der Anlage erfolgte bei CAC in Chemnitz unter der technischen und kommerziellen Anleitung seitens MRD. Zur Sicherstellung der Projektziele in dem hierfür vorgesehen Termin- und Kostenrahmen wurde ein gemeinsames Projektteam gebildet, welches sich aus Mitarbeitern der MRD und CAC zusammensetzte. Zur Unterstützung des Projektcontrollings wurde Prolynx Projektmanagement & Support als Partner eingebunden. Die Gesamtprojektleitung wurde durch MRD gerade unter dem Gesichtspunkt der mit CAC geschlossenen Vertragsform „Reimbursable“ und dem für MRD daraus resultierenden alleinigen Risiko wahrgenommen. Gleichermaßen sollte die Berücksichtigung der mit der Planung und Errichtung der Anlage verbundenen verfahrenstechnischen, betreiberund instandhaltungsrelevanten Anforderungen sichergestellt werden. Von allen am Projekt beteiligten Partnern wurde hinsichtlich der Erbringung von Ingenieur-, Liefer- und Montageleistungen ein Höchstmaß an Kompetenz, Flexibilität und Verantwortung abverlangt. Hierbei sind besonders die Kompetenz und das Engagement der am Projekt beteiligten CAC-Mitarbeiter hervorzuheben. Durch den Einsatz der bei CAC für die Planung derartiger Anlagen verfügbaren modernen Planungswerkzeuge (PDS, Design Review, Statikprogramm für Ausrüstungen, etc.) konnte die Umsetzung des Detail Engineerings in kürzester Zeit realisiert werden. Beweis dafür waren die sich überschneidenden extrem kurzen Projektabwicklungsphasen des Detail Engineerings und der Beschaffung von nur sechs Monaten sowie ein Liefer- und Montagezeitraum von nur acht Monaten. Die bisherigen Projektziele wurden durch die konsequente Umsetzung der Abwicklungsstrategie durch das integrierte Projektteam MRD/CAC innerhalb der vorgegebenen Kosten und Terminen erreicht. Die für eine Anbindung der neuen Anlage erforderlichen Infrastrukturmaßnahmen wurden parallel zur Planung und Errichtung der Anlage „Erweiterte Selektiv-Raffination“ erfolgreich Abgeschlossen.