Sicherheitsgerichtete Signale in der Prozessindustrie mit Ethernet APL übertragen
Vorteile einer durchgehenden Ethernet-Kommunikation in Chemieanlagen
Ein großer Teil der industriellen Kommunikation geschieht schon jetzt über das Profinet- respektive Profisafe-Protokoll. Beide Standards werden daher auch in Zukunft eine wesentliche Rolle spielen. Vor diesem Hintergrund bietet Phoenix Contact im Bereich Profinet/Profisafe eine anwenderfreundliche Komplettlösung an, die sich aus funktional sicheren Steuerungen und sicheren I/O-Modulen für die besonderen Anforderungen der Prozessindustrie zusammensetzt. Die relevanten, internationalen Zulassungen wie ATEX, IEC Ex, UL oder DNV liegen vor. Darüber hinaus umfasst das Portfolio des Blomberger Unternehmens die notwendigen Produkte zum Aufbau einer Ethernet-Infrastruktur, die sich von speziellen industriellen Ethernet-Kabeln und -Steckern bis zu APL-Switches erstrecken.
OPC UA zur sicheren Kommunikation zwischen Systemen und Standorten
In aktuellen Prozessanlagen kommen viele verschiedene herstellerspezifische Systeme und Übertragungsprotokolle zum Einsatz. Es steht außer Frage, dass die unterschiedlichen Systeme miteinander kommunizieren müssen, um den modernen Produktionsprozessen gerecht zu werden. Was einfach klingt, erfordert jedoch einen deutlichen Aufwand. An dieser Stelle bietet sich OPC UA an. Der herstellerübergreifende Standard erlaubt die einfache Etablierung der Datenweiterleitung zwischen den einzelnen Systemen. Wichtig ist jedoch in diesem Zusammenhang zu wissen, dass sich eine OPC-UA-Übertragung wegen der technischen Eigenschaften nicht als komplettes Kommunikationsnetzwerk im Fertigungsumfeld eignet, sondern lediglich für den Austausch zwischen den verschiedenen Systemen. Im Produktionsprozess wird vielmehr Profinet beziehungsweise für sicherheitskritische Systeme Profisafe verwendet. Derzeit arbeiten die entsprechenden Organisationen bereits an Lösungen mit OPC UA, die sich ebenfalls im Fertigungsprozess nutzen lassen. Diese sind allerdings nicht für hoch performante Prozesse einsetzbar.
Bei der isolierten Betrachtung der Sicherheitssysteme wird schnell offensichtlich, dass OPC UA eine Lücke aufweist. Das Übertragungsprotokoll ist im ersten Schritt nur für den nicht-sicheren Datenaustausch ausgelegt. Aktuell beschäftigen sich die Organisationen auch hier mit der Entwicklung einer Lösung: Safety over OPC UA soll Abhilfe schaffen. Damit werden die für die funktionale Sicherheit relevanten Daten ebenfalls erstmals über OPC UA zwischen herstellerunabhängigen Systemen weitergeleitet werden können. Da Safety over OPC UA zum großen Teil auf Profisafe basiert, lässt sich ein auf der Profinet-/Profisafe-Kommunikation beruhendes Produktionssystem bestens einsetzen. Sowohl Profisafe ebenso wie Safety over OPC UA verwenden das Black-Channel-Prinzip. Der Vorteil dieses Ansatzes liegt darin, dass die bestehenden Mechanismen von OPC UA weiterhin genutzt werden können. Der Black Channel ergänzt sie lediglich um die zusätzlichen sicherheitsrelevanten Teile. Außerdem lässt sich die vorhandene Hardware-Infrastruktur weiter einsetzen und muss nicht um Komponenten erweitert werden. Durch das Prinzip von Safety over OPC UA ist auch eine sichere Übertragung zwischen unterschiedlichen Standorten über das Internet möglich. Das gilt ebenfalls für einen dezentralen, sicherheitsgerichteten Datenaustausch, der mit einer konventionellen Verdrahtung nicht ohne weiteres umzusetzen war. Als physikalische Kommunikationskanäle kommen Kupferkabel, Rückwandbusse, Lichtwellenleiter oder drahtlose Lösungen wie WLAN in Betracht.
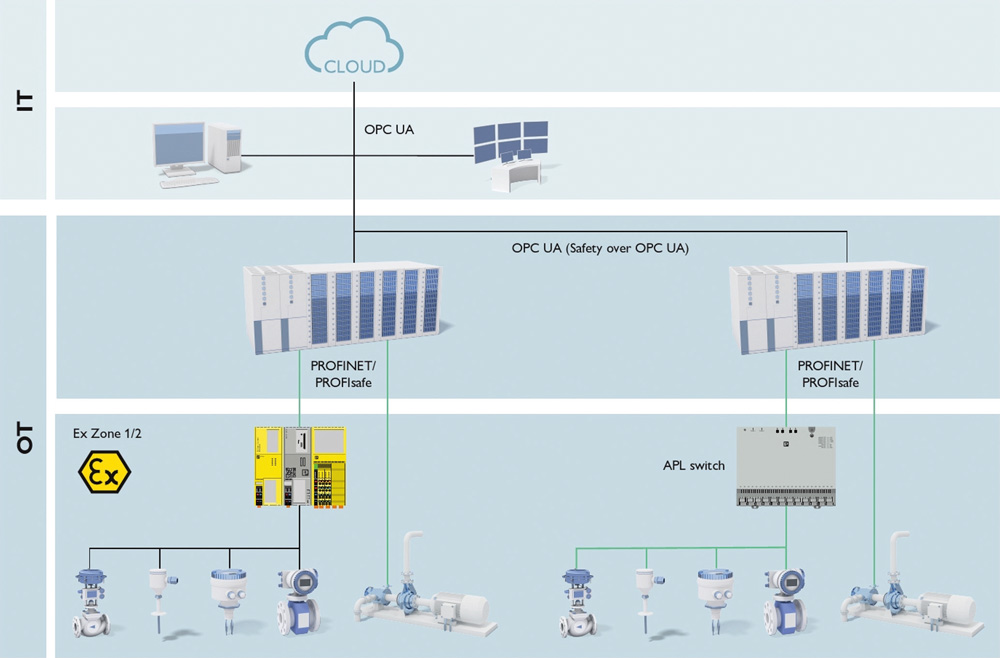
Mit APL zusätzliche Messwerte aus dem Ex-Bereich weiterleiten
Ein anderer Punkt, der für die Verwendung von Profinet/Profisafe spricht, ist die Einführung des Advanced Physical Layers (APL) in die Prozessindustrie. Mit dieser physikalischen Schicht lassen sich Daten via Ethernet in explosionsgefährdete Bereiche bis Zone 0 weiterleiten. Dazu werden bis dato spezielle Feldbussysteme oder die klassische 4…20 mA-Technik genutzt. Für APL erweist sich ferner der Wegfall von mehreren Analog-/Digitalwandlungen der Messsignale auf dem Weg vom Sensor bis zur Steuerung als Vorteil. Als Worst Case treten bei der klassischen 4…20 mA-Technik bis zu fünf Analog-/Digitalwandlungen auf, bis das Signal die Steuerung erreicht hat. Durch den Einsatz von APL reduziert sich die Anzahl auf eine Wandlung beim Erfassen im Sensor. Dadurch erhöht sich die Genauigkeit der Messsignale deutlich.
In der Prozessindustrie besteht schon seit langem die Notwendigkeit, in den Anlagen mehr als nur die Prozesswerte aufzunehmen. Dabei geht es beispielsweise um eine Remote-Konfiguration oder einfach um zusätzliche Messwerte, welche in den meist komplexen Messgeräten/-sensoren ohnehin vorliegen. Aus diesem Grund wurden in der Vergangenheit 4…20 mA-Messgeräte/-Sensoren mit eingebauter HART-Schnittstelle verwendet. Über das klassische 4…20 mA-Analogsignal lassen sich so weitere Informationen übertragen. Dies funktioniert durch die Aufmodulation der Informationen auf das 4…20 mA-Signal. Allerdings zeigt sich die Technik als langsam und – sofern die Steuerung nicht HART-fähig ist – als aufwendig integrierbar.
Mit Profisafe über APL, also einer Ethernet-basierten Kommunikation, sind derartige Anwendungsfälle einfach realisierbar und bieten zudem einen erheblichen Spielraum für zusätzliche Anwendungen, z. B. eine vorausschauende Wartung (Predictive Maintenance). Durch die Weiterleitung von Daten und Energie über lediglich zwei Drähte stellt APL eine gute Option dar, um bisherige 4…20 mA-Applikationen abzulösen. Je nach genutztem APL-Switch lassen sich bis zu 50 Feldgeräte gleichzeitig mit Energie und Daten versorgen. Die ersten verfügbaren APL-Switches umfassen zwischen acht und 32 Anschlussmöglichkeiten für Feldgeräte. Erste mit APL und Profisafe kompatible Feldgeräte stehen bereits in den Startlöchern und dürften ab 2023 erhältlich sein.
Der mit APL erzielbare Datendurchsatz kann sich ebenfalls sehen lassen. Dabei wird eine Vollduplex-Übertragung verwendet. In Verbindung mit den maximalen Kabellängen sind Datenraten bis 10 MBit/s möglich. Das reicht aus, damit neben den Prozesswerten eine Vielzahl zusätzlicher Informationen zur Verfügung gestellt werden kann.
Unterstützung bei der Prozessoptimierung
Werden die beiden Entwicklungen zusammengebracht, ergibt sich ein schlüssiges Gesamtbild für moderne Prozessanlagen. Profisafe dient dem funktional sicheren Datenaustausch zwischen den einzelnen Sicherheitskomponenten sowie in Verbindung mit Safety over OPC UA zwischen den Systemen verschiedener Hersteller. Denkbar ist sogar eine sichere Kommunikation zwischen unterschiedlichen Standorten via VPN-Tunnel (Virtual Private Network) über das Internet. Darüber hinaus lassen sich die Safety-Daten über Funkstandards wie WLAN weiterleiten. Kommt APL hinzu, ist eine durchgehende sichere Datenübertragung über Profisafe vom Sensor/Aktor bis in die Cloud möglich.
Neben den sicherheitsrelevanten Daten bietet sich eine durchgehende Ethernet-Kommunikation an, um auf einfache Weise Daten einzusammeln, die zum einen bei der Prozessoptimierung unterstützen können. Beispielsweise gibt es in diesem Bereich schon Ansätze zur Verbesserung der HAZOP-Qualität. Auf der anderen Seite stellt die vorausschauende Wartung ein Thema dar, das von den zusätzlich erfassten Daten profitieren wird. Phoenix Contact bietet den Anwendern hier ein komplettes Ökosystem von der Cloud über die Safe-PLC bis zu den Safe-I/Os und den APL-Switches an – ist also der optimale Partner für die Ethernet-basierte Zukunft der Prozessindustrie.
Autor: Manuel Ungermann, Strategisches Produktmarketing Safety – Automation Infrastructure, Phoenix Contact Electronics
Downloads
Kontakt
Phoenix Contact GmbH & Co.KG
Flachsmarktstr. 8
32825 Blomberg
Nordrhein-Westfalen, Deutschland
+49 5235 341 713
+49 5235 341 825